Finding Qualified Contractors
Choosing the right contractor for your roof repair is crucial for ensuring the longevity and safety of your home. A poorly executed repair can lead to further damage, costly future repairs, and even safety hazards. Taking the time to thoroughly vet potential contractors will save you significant time, money, and stress in the long run.
Finding a qualified contractor involves careful consideration of several key factors. It’s not just about the lowest price; it’s about experience, expertise, and a commitment to quality workmanship. A thorough vetting process will help you find a contractor who can deliver a lasting solution to your roof repair needs.
Essential Qualifications of a Roof Repair Contractor
Identifying a qualified contractor requires looking beyond just marketing materials. Several key qualifications should be prioritized to ensure you’re hiring someone capable and trustworthy. These qualifications demonstrate a commitment to professional standards and customer satisfaction.
- Extensive Experience: Look for contractors with a proven track record of at least 5-10 years of experience in roof repair and maintenance. This indicates familiarity with various roofing materials and techniques, as well as the ability to handle unexpected challenges.
- Positive Online Reviews and Testimonials: Check online review platforms like Yelp, Google My Business, and the Better Business Bureau for feedback from previous clients. Consistent positive reviews indicate a history of satisfactory service and customer satisfaction.
- Appropriate Licensing and Insurance: A valid contractor’s license ensures compliance with local regulations and demonstrates professional legitimacy. Comprehensive insurance, including workers’ compensation and liability coverage, protects you from potential financial losses in case of accidents or damages.
- Detailed Written Estimates: A professional contractor should provide a clear, detailed written estimate outlining all aspects of the repair, including materials, labor costs, and a projected timeline. Avoid contractors who provide vague or incomplete estimates.
- Warranty on Workmanship and Materials: A reputable contractor will offer a warranty on both their workmanship and the materials used. This warranty provides protection against defects or failures within a specified period, offering peace of mind.
Contractor Interview Checklist
Before making a hiring decision, conduct thorough interviews with several potential contractors. This checklist will guide you through essential questions and considerations.
Item | Details |
---|---|
Years of Experience | Verify experience through references and online reviews. |
Licensing and Insurance | Request copies of licenses and insurance certificates. Verify their validity with the relevant authorities. |
References | Contact previous clients to inquire about their experiences. |
Detailed Estimate | Compare estimates from multiple contractors, ensuring clarity and comprehensiveness. |
Warranty Information | Review warranty details carefully, noting the duration and coverage. |
Payment Terms | Clarify payment schedules and methods. Avoid contractors requiring full upfront payment. |
Project Timeline | Discuss realistic timelines and potential delays. |
Clean-up Procedures | Inquire about their post-repair clean-up procedures. |
Verifying Contractor Licenses and Insurance
Verifying a contractor’s license and insurance is a critical step in protecting yourself from potential risks. Failure to verify these credentials can leave you vulnerable to financial and legal liabilities.
Contact your state’s licensing board or contractor’s state registration board to verify the contractor’s license status and confirm that it’s current and valid. Request copies of their liability insurance and workers’ compensation insurance certificates. Confirm that the policies are active and provide adequate coverage for the scope of the roof repair project. You should also ask for proof of general liability insurance, which protects you from financial losses if the contractor causes damage to your property. For example, if a contractor’s worker accidentally damages your landscaping during the repair, their general liability insurance should cover the costs of repair or replacement.
Cost Estimation and Budgeting
Accurately estimating the cost of roof repairs is crucial for both homeowners and contractors. A transparent and detailed cost breakdown ensures a smooth project and avoids unexpected expenses. Understanding the various methods for cost estimation and the factors influencing the final price is essential for informed decision-making.
Methods for Estimating Roof Repair Costs
Several methods exist for estimating roof repair costs, each offering varying levels of precision. Choosing the right method depends on the complexity of the repair and the information available.
- Square Footage Method: This method calculates the cost based on the area of the roof needing repair. A price per square foot is established, factoring in materials and labor. This is a simple method, suitable for smaller, straightforward repairs. For example, if the repair area is 100 square feet and the cost per square foot is $15, the estimated cost would be $1500. This method, however, can be inaccurate for complex repairs requiring specialized materials or extensive labor.
- Detailed Itemized Estimate: This method involves a comprehensive breakdown of all materials and labor costs. Each component, from shingles and underlayment to labor hours for tear-off, repair, and cleanup, is individually priced. This provides a more accurate estimate, particularly for larger or more complex projects. A detailed itemized estimate allows for better budgeting and transparency.
- Hourly Rate Plus Materials: This method calculates the cost based on the contractor’s hourly rate and the cost of materials. The contractor estimates the number of hours required for the repair and adds the cost of the necessary materials. This approach is often used for smaller repairs where precise material quantities are difficult to determine beforehand. The accuracy of this method relies heavily on the contractor’s accurate assessment of the required labor hours.
Sample Roof Repair Budget Breakdown
The following is a sample budget breakdown for a typical roof repair project involving the replacement of 100 square feet of damaged shingles:
Item | Quantity | Unit Cost | Total Cost |
---|---|---|---|
Shingles | 3 squares (1 square = 100 sq ft) | $40/square | $120 |
Underlayment | 100 sq ft | $1/sq ft | $100 |
Flashing | As needed | $20 | $20 |
Nails | As needed | $10 | $10 |
Labor (Tear-off, installation, cleanup) | 8 hours | $50/hour | $400 |
Waste disposal | $50 | $50 | |
Total Estimated Cost | $700 |
Note: This is a simplified example. Actual costs may vary significantly depending on location, materials used, and the complexity of the repair.
Factors Impacting Roof Repair Costs
Several factors can significantly influence the overall cost of a roof repair. Understanding these factors allows for more realistic budgeting and avoids potential surprises.
- Extent of Damage: The size and severity of the damage directly impact the amount of materials and labor required. A small leak might only require minor repairs, while extensive damage might necessitate a full roof replacement.
- Roof Access: Difficult roof access, such as steep slopes or limited access points, can increase labor costs as it requires more time and specialized equipment.
- Material Costs: The type and quality of materials used significantly affect the overall cost. High-quality, long-lasting materials are generally more expensive than lower-grade options.
- Labor Rates: Labor rates vary depending on location, contractor experience, and demand. Experienced contractors generally charge higher hourly rates.
- Permits and Inspections: Depending on local regulations, permits and inspections might be required, adding to the overall project cost.
- Unexpected Issues: During the repair process, unforeseen issues such as rotted decking or structural problems might be discovered, leading to additional costs.
Types of Roof Repairs: Contractor For Roof Repair
Roof repairs are a necessary part of homeownership, and understanding the common types can help you budget effectively and communicate clearly with your contractor. This section Artikels five frequently needed repairs and details the processes involved.
Contractor for roof repair – Many roof issues stem from weather damage, age, or poor installation. Addressing these problems promptly prevents more extensive and costly repairs down the line. Regular inspections, ideally annually, are crucial for early detection and proactive maintenance.
Damaged Shingle Repair
Repairing a damaged shingle involves several steps to ensure a lasting fix. First, the damaged shingle must be carefully inspected to assess the extent of the damage. Minor cracks or curling can often be addressed with roofing cement, while more significant damage may require complete shingle replacement. If replacement is necessary, the surrounding shingles need to be carefully loosened to allow for the insertion of the new shingle. Once the new shingle is in place, roofing cement is used to seal the edges and ensure a watertight seal. Finally, the area should be inspected to confirm the repair is secure and aesthetically consistent with the rest of the roof. This process is generally straightforward for homeowners with basic DIY skills, but hiring a professional is recommended for larger repairs or complex roof designs.
Asphalt Shingle Repair Methods
Asphalt shingle repairs typically involve replacing individual damaged shingles or patching smaller areas. For single shingle replacement, the damaged shingle is removed, and a new shingle is installed, ensuring proper alignment and overlapping with adjacent shingles. Roofing cement is used to secure the new shingle and create a watertight seal. Larger areas of damage might necessitate a patch repair using specialized roofing underlayment and asphalt cement to cover the affected area, ensuring a smooth transition with the existing shingles. This method is cost-effective for localized damage and can be completed relatively quickly.
Tile Roof Repair Methods
Tile roof repairs differ significantly from asphalt shingle repairs due to the nature of the material. Damaged tiles are usually replaced individually. This process can be more complex than asphalt shingle repair due to the weight and fragility of the tiles. Care must be taken to avoid damaging surrounding tiles during removal and installation. In some cases, specialized tools and techniques may be required, particularly for clay or concrete tiles. Moreover, the repair often necessitates working at heights, which requires appropriate safety precautions and possibly specialized equipment like scaffolding. The cost of tile repair is generally higher than asphalt shingle repair due to the labor intensity and the cost of the replacement tiles.
Flashing Repair
Flashing, the waterproof material used around chimneys, vents, and other roof penetrations, is crucial for preventing leaks. Damaged or missing flashing is a common cause of roof leaks. Repairing flashing involves removing the damaged section and replacing it with new flashing material, ensuring a tight seal to prevent water infiltration. This often requires careful work around the existing structure to avoid further damage. Improper flashing repair can lead to significant water damage, making professional repair essential.
Gutter and Downspout Repair
Gutters and downspouts are vital for directing rainwater away from the house. Clogs, leaks, or damage to these systems can lead to water damage to the roof, walls, and foundation. Repairs can range from simple cleaning of clogs to replacing damaged sections of gutters or downspouts. Severe damage may require complete gutter or downspout replacement. Regular maintenance of gutters and downspouts is crucial for preventing costly repairs.
Contractual Agreements and Legal Aspects
Protecting your interests and ensuring a successful roof repair project requires a well-defined contract. This section details the crucial elements of a roofing contract and the legal implications of overlooking essential clauses. Understanding these aspects will empower you to make informed decisions and avoid potential disputes.
Essential Clauses in a Roof Repair Contract
A comprehensive roof repair contract should safeguard both the homeowner and the contractor. The following clauses are essential for a legally sound and protective agreement. Missing even one can lead to unforeseen complications and disputes.
- Parties Involved: Clearly identify the homeowner and the contractor, including their full legal names and addresses.
- Scope of Work: A detailed description of the repairs, including materials, methods, and specific areas to be addressed. This should be precise enough to prevent misunderstandings about the extent of the work.
- Payment Schedule: A clear Artikel of payment milestones tied to specific stages of completion. This could include a down payment, progress payments, and final payment upon project completion and satisfactory inspection.
- Project Timeline: Realistic start and completion dates, along with provisions for potential delays due to unforeseen circumstances (e.g., inclement weather). Include a clause defining how delays will be handled and if there are penalties for exceeding the agreed-upon timeline.
- Warranty and Guarantees: Specify the length and scope of the warranty on materials and workmanship. This ensures recourse if the repairs fail prematurely.
- Dispute Resolution: A mechanism for resolving disagreements, such as mediation or arbitration, to avoid costly litigation.
- Permits and Licenses: A statement confirming the contractor’s responsibility for obtaining necessary permits and licenses. This protects the homeowner from potential legal repercussions.
- Insurance: Confirmation that the contractor carries adequate liability and workers’ compensation insurance, protecting both parties from financial liability in case of accidents or damages.
- Changes and Modifications: A clause detailing the process for making changes to the original scope of work, including how changes will affect the timeline and payment schedule.
- Termination Clause: Conditions under which either party can terminate the contract, outlining the responsibilities of each party in case of termination.
Sample Contract Outlining Payment Schedules and Project Timelines
This is a simplified example and should be reviewed and adapted by legal professionals for your specific situation.
Roof Repair Contract
This agreement is made between [Homeowner Name], residing at [Homeowner Address] (hereinafter “Homeowner”), and [Contractor Name], residing at [Contractor Address] (hereinafter “Contractor”).1. Scope of Work: Repair of roof leaks at [Specific location(s) on roof]. Includes [List materials and specific repairs].
2. Payment Schedule:
a. 25% down payment upon contract signing.
b. 50% upon completion of tear-off and underlayment installation.
c. 25% upon final inspection and completion of all repairs.
3. Project Timeline: Project to commence on [Start Date] and be completed by [Completion Date].
4. Warranty: Contractor provides a [Number]-year warranty on all materials and workmanship.
[Other essential clauses as Artikeld above]
Signatures:
Homeowner:_________________________ Date:_________________
Contractor:_________________________ Date:_________________
Legal Implications of Hiring an Unlicensed Contractor
Hiring an unlicensed contractor carries significant legal and financial risks. Depending on your location, this could lead to fines for the homeowner, void warranties, difficulty obtaining insurance coverage for the completed work, and a lack of recourse if the work is faulty or not completed as agreed. It’s crucial to verify a contractor’s license and insurance before engaging their services. In many jurisdictions, working without a license is illegal and can result in penalties for both the contractor and the homeowner. Always obtain proof of licensure and insurance before signing any contract.
Materials and Supplies
The selection of appropriate materials is crucial for a successful and long-lasting roof repair. Using high-quality materials not only ensures the longevity of the repair but also contributes to the overall structural integrity and aesthetic appeal of your roof. Understanding the properties and applications of various roofing materials is essential for making informed decisions.
The durability and performance of roof repairs are directly linked to the quality of the materials used. Inferior materials are more susceptible to damage from weather elements, leading to premature deterioration and costly re-repairs. Choosing high-quality materials, while often representing a higher upfront cost, ultimately proves more economical in the long run by extending the lifespan of your roof and minimizing future maintenance expenses.
Common Roofing Materials and Their Specifications
Selecting the right roofing materials depends heavily on several factors, including climate, roof type, and budget. The following list details some commonly used materials and their key characteristics.
- Asphalt Shingles: These are the most common roofing material due to their affordability and ease of installation. Specifications vary, but generally include a fiberglass or organic base mat coated with asphalt and surfaced with mineral granules. Different shingle types offer varying levels of durability and lifespan, from 20 to 50 years. Factors such as thickness, granule size, and composition influence their performance and resistance to weather conditions.
- Metal Roofing (Aluminum, Steel, Copper): Metal roofs are known for their exceptional durability and longevity, often lasting 50 years or more. They are highly resistant to fire, wind, and hail damage. Specifications include gauge (thickness), coating type (e.g., zinc, aluminum), and color. Copper roofs, while the most expensive, offer unparalleled longevity and aesthetic appeal.
- Tile Roofing (Clay, Concrete): Tile roofs are renowned for their beauty, durability, and fire resistance. Clay tiles are generally more expensive than concrete but offer superior longevity. Specifications include size, shape, color, and weight. Proper installation is crucial due to their weight and fragility.
- Wood Shakes and Shingles: These natural materials provide a rustic aesthetic, but require more maintenance than other options. They are susceptible to rot, insect infestation, and fire damage unless treated properly. Specifications include wood type (e.g., cedar, redwood), thickness, and treatment (e.g., fire-retardant). Regular inspections and maintenance are essential.
- Underlayment: This crucial component is installed beneath the roofing material to provide an additional layer of protection against moisture. Specifications include material type (e.g., felt, synthetic), weight, and water resistance. High-quality underlayment significantly enhances the roof’s longevity and prevents leaks.
Selecting Roofing Materials Based on Climate and Roof Type, Contractor for roof repair
Climate and roof type significantly influence the choice of roofing materials. For example, a steep-sloped roof in a high-wind area might benefit from the durability of metal roofing, while a low-sloped roof in a region with heavy rainfall might require a material with superior water resistance, such as clay tiles or high-quality asphalt shingles with enhanced waterproofing. Areas with extreme temperature fluctuations may require materials with superior thermal properties to minimize expansion and contraction. Consideration should also be given to local building codes and regulations, which may dictate specific material requirements.
For instance, a coastal region with high humidity and salt spray might benefit from a corrosion-resistant metal roofing system, while a region with frequent hailstorms would necessitate a hail-resistant asphalt shingle or metal roofing. Similarly, a flat roof in a snowy climate may require a material designed to withstand the weight of accumulated snow, such as a robust membrane system. Careful consideration of these factors ensures the selection of materials that provide optimal performance and longevity in the specific environmental conditions.
Project Timeline and Scheduling
Effective project scheduling is crucial for a successful roof repair. A well-defined timeline ensures the project progresses smoothly, minimizes disruptions, and helps manage expectations. This section Artikels a typical timeline, considers the impact of weather, and addresses potential delays and mitigation strategies.
A typical roof repair project, depending on the scale and complexity, can be completed within a timeframe ranging from a few days to several weeks. Factors such as the size of the roof, the extent of damage, material availability, and the contractor’s workload significantly influence the duration.
Sample Project Timeline
The following timeline provides a general framework for a medium-sized roof repair project. Specific timelines will vary based on the unique aspects of each project.
Day | Activity |
---|---|
1 | Initial assessment and contract signing. Material ordering. |
2-3 | Preparation: Debris removal, area protection, and necessary safety measures. |
4-7 | Repair work: This phase includes addressing the identified damage, such as replacing shingles, repairing flashing, or patching leaks. The duration depends on the extent of the damage. |
8 | Final inspection and cleanup. |
Weather Conditions and Project Timeline
Weather significantly impacts roof repair projects. Inclement weather, such as heavy rain, snow, or strong winds, can cause delays. For instance, work cannot safely proceed during a thunderstorm or when high winds pose a risk of falling debris. Furthermore, prolonged periods of rain can delay the drying of materials, extending the overall project timeline. Contractors typically build contingency time into their schedules to accommodate potential weather-related delays.
Potential Delays and Mitigation Strategies
Several factors beyond weather can lead to project delays. These include material shortages, unexpected damage discovered during the repair process, and scheduling conflicts with other projects.
- Material Shortages: Ordering materials well in advance helps mitigate this risk. The contractor should proactively confirm material availability before commencing the project.
- Unexpected Damage: Thorough initial assessments are vital. However, unforeseen damage might be discovered during the repair process, requiring additional time and resources. A contingency plan should be in place to address such situations.
- Scheduling Conflicts: Effective communication and scheduling are essential to avoid conflicts with other projects the contractor might be working on. A clear project timeline shared with the client helps manage expectations.
To minimize delays, clear communication between the contractor and client is paramount. Regular updates on the project’s progress and any potential delays should be provided. Proactive planning, contingency budgeting, and flexible scheduling can significantly contribute to completing the project on time and within budget.
Safety Procedures During Repairs
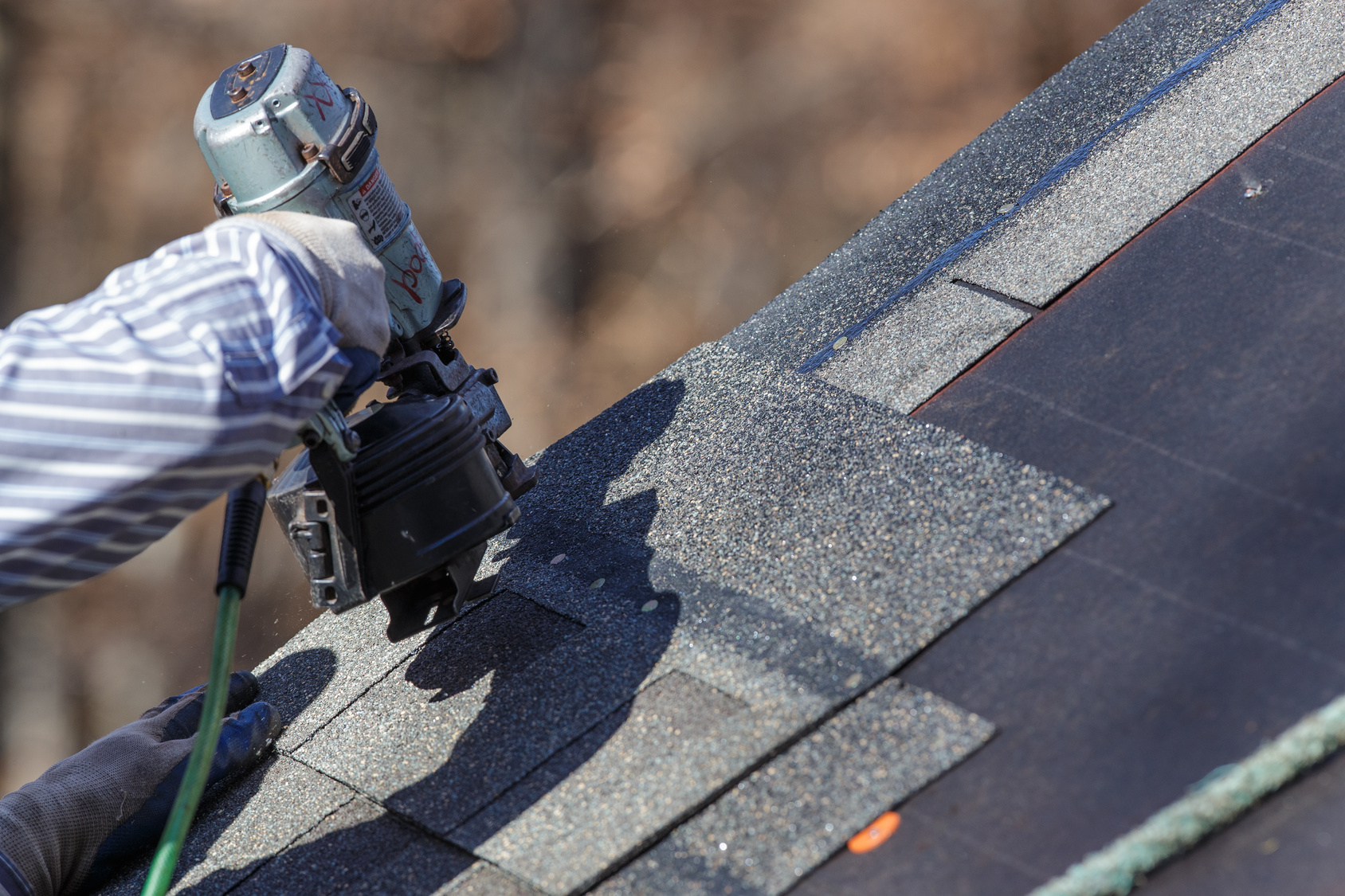
Roof repairs, while necessary for maintaining a home’s structural integrity and preventing costly damage, inherently involve risks. Prioritizing safety for both homeowners and contractors is paramount throughout the entire project. This section details essential safety precautions and a comprehensive safety plan to mitigate potential hazards.
Homeowners and contractors alike must understand and adhere to established safety protocols to ensure a safe and efficient roof repair process. Neglecting these precautions can lead to serious injuries or fatalities. A proactive approach to safety is crucial for a successful project.
Safety Precautions for Homeowners During Roof Repairs
While homeowners should not directly participate in the repair work itself, their safety is still a significant concern. Maintaining a safe environment around the work area is crucial for preventing accidents.
- Clear the area beneath the work zone of any obstructions, including furniture, vehicles, and debris. This prevents potential injury from falling objects.
- Keep children and pets away from the work area. The active work zone presents a significant fall hazard and risk of injury from falling tools or materials.
- Alert neighbors about the ongoing repairs. This is especially important if the work involves potentially noisy equipment or activities that might cause disruption.
- Ensure adequate lighting in the work area, particularly if the repairs are conducted during low-light conditions. This improves visibility and reduces the risk of accidents.
- If using a ladder to access the roof for observation, ensure it’s properly positioned and secured on stable ground, and that you are comfortable with its use. Always follow the manufacturer’s safety instructions.
Contractor Safety Plan for Residential Roof Repairs
A well-defined safety plan is essential for contractors to ensure the well-being of their team and the property. This plan should be communicated clearly to all involved and strictly adhered to.
- Pre-work Site Assessment: A thorough inspection of the roof and surrounding area should be conducted before work begins to identify potential hazards such as unstable structures, electrical lines, or dangerous debris. This assessment informs the development of a site-specific safety plan.
- Personal Protective Equipment (PPE): All workers must wear appropriate PPE, including hard hats, safety glasses, work gloves, and high-visibility clothing. This ensures protection against falls, impacts, and exposure to hazardous materials.
- Fall Protection: The implementation of a robust fall protection system is non-negotiable. This may include safety harnesses, anchor points, and lifeline systems. Regular inspections of this equipment are vital to guarantee its functionality and safety.
- Tool Safety: Tools should be regularly inspected for damage and maintained in good working order. Proper storage and handling procedures should be established to prevent accidental injuries. Power tools should be used according to manufacturer’s instructions.
- Emergency Procedures: A clear emergency plan should be established, including procedures for handling injuries, contacting emergency services, and securing the worksite in case of an accident. This plan should be readily accessible to all workers.
- Weather Monitoring: Work should be suspended immediately in case of inclement weather conditions such as high winds, rain, or lightning. Contractor should have a plan for securing the work area in the event of sudden weather changes.
Proper Fall Protection Equipment and Techniques
Falls are a leading cause of injury in roofing work. Therefore, utilizing appropriate fall protection equipment and techniques is of paramount importance. Failure to do so can have devastating consequences.
Fall protection systems typically consist of a full-body harness, anchor points securely attached to a stable structure, and a lifeline connecting the harness to the anchor point. The anchor point must be capable of withstanding significant weight and should be inspected regularly for any signs of wear or damage. Different types of fall arrest systems exist, such as those with shock-absorbing lanyards, designed to minimize the impact force during a fall. Proper training on the correct use and inspection of fall protection equipment is essential for all workers. Regular inspections and maintenance of the equipment are also crucial for ensuring its effectiveness and safety.
Proper training and regular inspections are vital to ensure the effectiveness and safety of fall protection equipment.
Post-Repair Maintenance and Inspection
Proper post-repair maintenance and regular inspections are crucial for extending the lifespan of your roof and preventing costly future repairs. By diligently following a maintenance schedule and promptly addressing any potential problems, you can ensure your roof remains a reliable and protective barrier for your home for many years to come. This section details essential inspection procedures and maintenance practices for various roofing materials.
Post-Repair Roof Inspection Checklist
A thorough inspection after roof repairs is essential to verify the quality of the work and identify any potential issues. This checklist provides a structured approach to ensure all aspects of the repair are satisfactory.
- Examine the repaired area for any loose or missing shingles, tiles, or flashing.
- Check for any signs of water leakage, such as stains or dampness on the ceiling or walls below the repair area.
- Inspect the surrounding areas for any damage that may have been overlooked during the repair process.
- Verify that all materials used are consistent with the agreed-upon specifications in the contract.
- Confirm that all debris and waste materials have been properly removed from the property.
- Assess the overall appearance of the repaired area, ensuring it blends seamlessly with the rest of the roof.
- Check for proper alignment and secure fastening of all components.
- Review the warranty documentation provided by the contractor, paying close attention to coverage and limitations.
Recommended Maintenance Procedures for Different Roofing Materials
Different roofing materials require specific maintenance procedures to maintain their integrity and longevity. Failing to follow these guidelines can lead to premature deterioration and costly repairs.
- Asphalt Shingles: Regular cleaning of debris, such as leaves and branches, is crucial. Inspect for loose or damaged shingles and replace them promptly. Consider professional cleaning and moss removal every few years, particularly in humid climates. Annual inspections are recommended.
- Tile Roofs (Clay or Concrete): Regular cleaning is important to remove dirt, moss, and algae buildup. Inspect for cracked or broken tiles and replace them as needed. Professional cleaning might be necessary every few years depending on the climate and environmental conditions. Annual inspections are recommended.
- Metal Roofs: Regularly inspect for rust, corrosion, or dents. Clean the roof periodically to remove debris and prevent buildup. Loose fasteners should be tightened, and any damaged sections should be repaired or replaced. Annual inspections are recommended.
Signs of Potential Problems Requiring Further Attention
Even after professional repairs, certain signs may indicate underlying issues requiring further attention. Promptly addressing these problems can prevent more extensive and costly damage.
- Persistent Leaks: If you notice persistent water leaks after the repairs, it’s crucial to contact the contractor immediately. This could indicate incomplete or faulty repairs.
- Sagging or Uneven Roofline: Sagging or uneven areas on the roof could indicate structural problems or underlying damage that requires further investigation and repair.
- Unusual Noises: Unusual creaking, cracking, or banging noises from the roof, especially during windy conditions, could signify loose or damaged components requiring immediate attention.
- Increased Energy Bills: A significant increase in energy bills after roof repairs might suggest improper insulation or inadequate sealing, leading to heat loss or gain.
- Visible Damage: The appearance of new cracks, holes, or missing materials on the roof, even in areas not directly related to the initial repair, should be addressed promptly.
Warranty and Guarantees
Securing a comprehensive warranty or guarantee is a crucial aspect of any roof repair project. It provides vital protection for your investment and safeguards you against potential future issues stemming from faulty workmanship or substandard materials. Understanding the different types of warranties available and the process for filing a claim is essential for ensuring your peace of mind.
A warranty, in essence, is a written promise from the contractor guaranteeing the quality of their work and/or the materials used for a specified period. Guarantees often function similarly, though the specific terms can vary. The extent of coverage offered depends on the type of warranty and the contractor’s policies. Choosing a contractor who offers a robust warranty is a key indicator of their confidence in their work and commitment to customer satisfaction.
Types of Warranties
Warranties typically fall into several categories. These may include material warranties, which cover defects in the materials themselves, and workmanship warranties, which cover issues resulting from improper installation or execution of the repair. Some contractors offer a combined warranty encompassing both aspects. The duration of these warranties can vary considerably, ranging from a few years to a decade or more, depending on the materials used and the contractor’s policies. For example, a manufacturer might offer a 20-year warranty on specific roofing shingles, while the contractor’s workmanship warranty might cover the installation for 5 years. It’s vital to review the specific terms of each warranty carefully.
Warranty Claim Process
Filing a warranty claim typically involves documenting the issue with photographic evidence and a detailed written description of the problem. This documentation should be submitted to the contractor within the timeframe specified in the warranty agreement. The contractor will then review the claim and, if the damage falls under the warranty’s coverage, will schedule the necessary repairs. It’s advisable to maintain a copy of all relevant documentation, including the original warranty agreement, photos, and communication records with the contractor, for your records. Disputes regarding warranty claims can be resolved through mediation or, if necessary, legal action, though this is a less desirable outcome. A clearly defined warranty claim process, as Artikeld in the contract, will help facilitate a smoother resolution should any issues arise.
Dealing with Insurance Claims
Filing an insurance claim for roof damage can seem daunting, but a systematic approach can significantly simplify the process and ensure a smoother experience. Understanding the steps involved, communicating effectively with your insurance provider, and knowing the role of your contractor are crucial for a successful claim. This section will guide you through each stage.
Filing an Insurance Claim for Roof Damage
The first step is to promptly report the damage to your insurance company. This typically involves contacting them by phone or through their online portal. You will need to provide details about the incident, including the date and time of the damage, the extent of the damage, and any contributing factors (e.g., storm, tree fall). After the initial report, your insurance company will likely assign an adjuster to assess the damage. You should keep detailed records of all communication with your insurer, including dates, times, and the names of individuals you spoke with. It’s also advisable to take comprehensive photos and videos documenting the damage from various angles before any repairs are attempted. These visual records are crucial for supporting your claim. Finally, you will need to complete any necessary claim forms provided by your insurer, ensuring all information is accurate and complete.
Communicating with Insurance Adjusters
Effective communication with insurance adjusters is essential for a successful claim. Be prepared to clearly and concisely explain the extent of the damage and provide supporting documentation, such as photos, videos, and repair estimates from your contractor. Be polite and professional in all your interactions, even if you encounter delays or disagreements. If you disagree with the adjuster’s assessment, politely explain your reasoning and provide supporting evidence. It’s helpful to maintain a calm and respectful demeanor throughout the process, even if the process is frustrating. Keep detailed records of all communications with the adjuster, including the date, time, and a summary of the conversation. Consider sending follow-up emails to confirm agreements and ensure a clear paper trail.
The Contractor’s Role in the Insurance Claim Process
Your contractor plays a vital role in navigating the insurance claim process. They can provide crucial information to support your claim, including detailed estimates of the repair costs and a breakdown of the materials and labor involved. They can also help you understand the insurance adjuster’s assessment and negotiate any discrepancies. A reputable contractor will be familiar with insurance claim procedures and can assist you in gathering the necessary documentation. In some cases, the contractor may directly communicate with the insurance adjuster to expedite the process. Choosing a contractor with experience in dealing with insurance claims can streamline the entire process and minimize potential delays. It is advisable to select a contractor before initiating the claim process to ensure a smoother and more efficient resolution.
Finding Reviews and Testimonials
Finding reliable reviews and testimonials is crucial when selecting a roof repair contractor. Online platforms offer a wealth of information, but navigating this landscape requires a discerning eye to separate genuine feedback from misleading or fabricated comments. Careful scrutiny is essential to ensure you’re making an informed decision based on trustworthy sources.
Online reviews and testimonials provide valuable insights into a contractor’s reputation, work quality, and customer service. Reputable review sites such as Google My Business, Yelp, Angie’s List, and Better Business Bureau (BBB) allow past clients to share their experiences, both positive and negative. Checking these platforms provides a broad overview of a contractor’s history and performance. Searching for the contractor’s name and location on these platforms should yield a comprehensive picture of their public perception.
Verifying the Authenticity of Online Reviews
Determining the authenticity of online reviews is paramount. While many reviews are genuine, some may be fabricated to inflate a contractor’s reputation. Several strategies can help in verifying the authenticity of reviews. Looking for detailed and specific accounts, rather than generic praise, is a key indicator of genuine feedback. A truly authentic review will often include specific details about the project, the contractor’s approach, and the overall outcome. Conversely, vague or overly enthusiastic reviews, lacking concrete details, may be suspicious. Additionally, a consistent pattern of positive reviews without any negative feedback should raise concerns, suggesting potential manipulation. Checking the reviewer’s profile for consistency across multiple platforms can also help to verify authenticity. If a reviewer consistently praises the same contractor across various platforms, it lends more credibility to the review. However, if a profile appears new or lacks other reviews, it warrants further scrutiny.
Identifying Potential Red Flags in Online Reviews
Several red flags can indicate potentially unreliable or fabricated reviews. A sudden surge in overwhelmingly positive reviews within a short period could be a sign of review manipulation. Similarly, an unusually high number of five-star reviews without any lower ratings should raise suspicion. Conversely, a significant number of consistently negative reviews, especially if they describe similar issues (e.g., poor workmanship, lack of communication, or failure to honor warranties), should be taken seriously. Generic reviews lacking specific details or personal experiences are another potential red flag. Pay close attention to reviews that seem overly scripted or lack specific details about the work performed. Finally, be wary of reviews that focus heavily on price alone, neglecting other important aspects such as quality of work and customer service. A contractor who consistently underbids competitors might compromise on quality to maintain profitability.
Frequently Asked Questions
What is the average lifespan of a roof?
The lifespan varies greatly depending on the roofing material, climate, and maintenance. Asphalt shingles typically last 15-30 years, while tile roofs can last 50 years or more.
How can I tell if I need a roof repair versus a full roof replacement?
Minor leaks, a few damaged shingles, or curling shingles often indicate repair needs. Extensive damage, significant age, or widespread deterioration usually necessitates a full replacement.
What should I do if my contractor doesn’t complete the work as agreed?
Review your contract carefully. If the contractor breaches the agreement, attempt to resolve the issue through communication. If this fails, consider legal action or mediation.
Can I get financing for roof repairs?
Many contractors offer financing options, or you can explore home improvement loans from banks or credit unions. Check your credit score and compare interest rates before committing.