Average Asphalt Roof Cost Per Square Foot
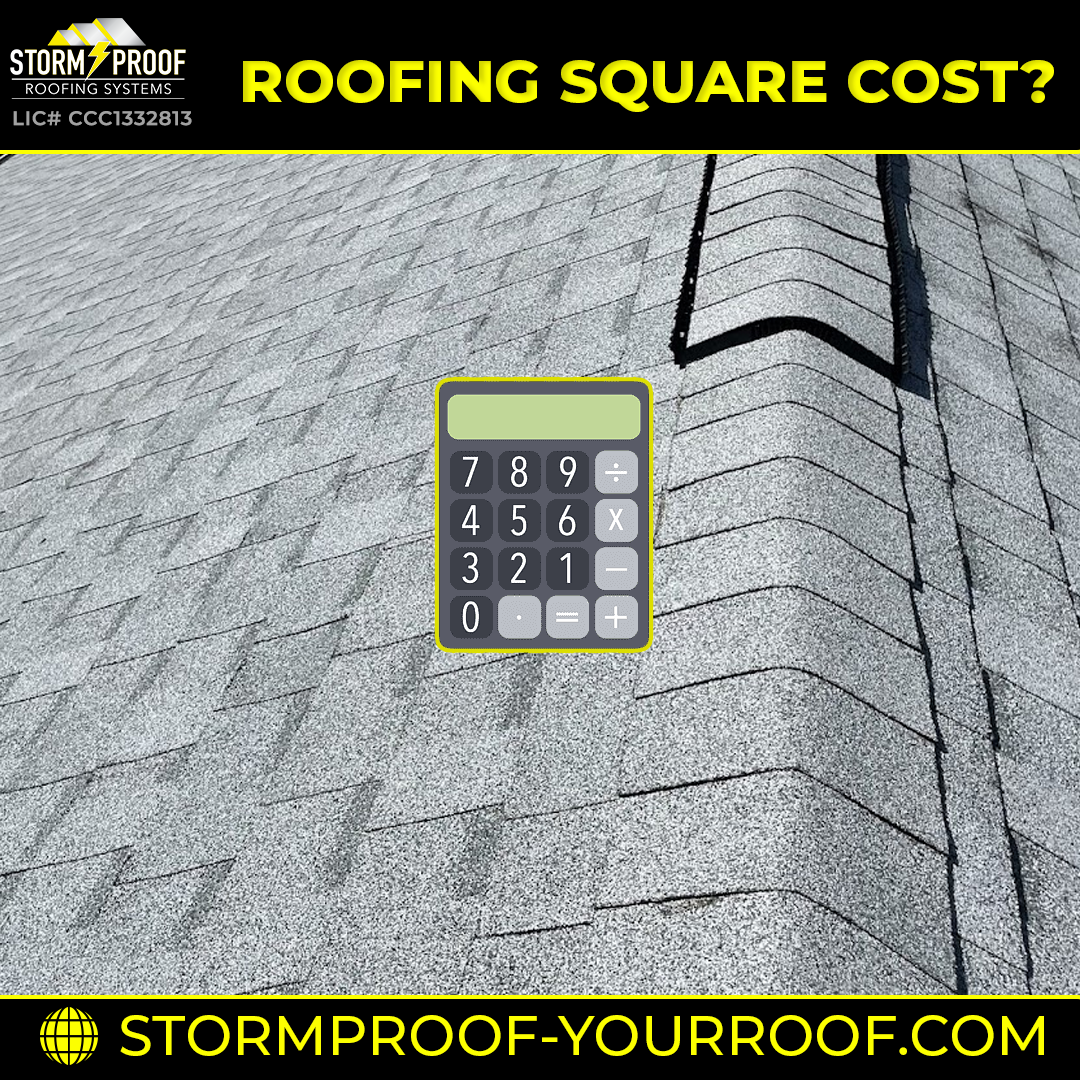
Asphalt shingles remain a popular roofing choice across the United States due to their affordability and relatively easy installation. However, the cost of an asphalt roof varies significantly depending on several factors. Understanding these factors can help homeowners budget effectively for their roofing projects. This section will explore the average cost per square foot of asphalt roofing and the elements that influence price fluctuations.
Average Asphalt Roof Cost Per Square Foot by Region
The cost of asphalt roofing can differ considerably across the US. Geographic location influences material costs, labor rates, and even the type of asphalt shingle best suited for the climate. For instance, areas prone to severe weather might require more durable and expensive shingles. Generally, the South and Midwest tend to have lower costs than the Northeast and West Coast. A reasonable range for the average cost per square foot of a basic asphalt shingle roof installation might be between $3 and $8, although costs in some areas could fall outside this range. This variance reflects the interplay of regional economic factors and market conditions.
Asphalt Shingle Types and Costs
The type of asphalt shingle significantly impacts the overall cost. Different shingles offer varying degrees of durability, aesthetic appeal, and longevity.
Shingle Type | Average Cost Per Square Foot |
---|---|
3-Tab Shingles | $2.50 – $5.00 |
Architectural Shingles | $4.00 – $8.00 |
Note: These figures are estimates and can fluctuate based on regional variations, material quality, and labor costs. Higher-end architectural shingles, with enhanced durability and aesthetic features, command a premium.
Factors Contributing to Asphalt Roofing Cost Variability
Several key factors contribute to the variability in asphalt roofing costs. Understanding these helps homeowners make informed decisions and avoid unexpected expenses.
- Material Costs: The price of asphalt shingles themselves fluctuates based on raw material costs, manufacturing processes, and market demand. Premium shingles with enhanced features, such as thicker construction or improved weather resistance, naturally cost more.
- Labor Costs: Labor rates vary significantly by region and the complexity of the roofing job. Steeper roofs or those requiring extensive repairs increase labor costs. The experience and reputation of the roofing contractor also influence labor charges.
- Roof Complexity: The shape and size of the roof significantly affect the installation time and, consequently, the overall cost. Complex roof designs with multiple angles, valleys, and dormers demand more labor and materials.
- Underlayment and Other Materials: The cost of underlayment, flashing, and other necessary materials adds to the overall project expense. Higher-quality underlayments, offering better protection against moisture, can increase costs but provide long-term benefits.
- Permitting and Inspections: Obtaining necessary permits and undergoing inspections adds to the overall project cost. These requirements vary by location and the scope of the roofing work.
- Waste Removal: Disposal of old roofing materials can add a small but noticeable expense to the overall project.
- Contractor Overhead and Profit Margin: The contractor’s overhead costs and profit margin are incorporated into the final price. Choosing a reputable contractor with a transparent pricing structure is crucial.
Factors Affecting Asphalt Roof Cost
Several factors beyond the basic square footage significantly influence the final cost of an asphalt shingle roof. Understanding these variables allows homeowners to better budget for their roofing project and avoid unexpected expenses. These factors primarily relate to the complexity of the roofing job itself, the cost of materials disposal, and the hourly rates charged by different roofing contractors.
Roof Complexity and its Impact on Cost
The shape and design of a roof directly impact the labor and materials required for installation. Simple, flat roofs are generally the least expensive to cover, while complex roofs with multiple slopes, valleys, hips, and dormers increase both the time and materials needed, driving up the overall cost. For example, a steeply pitched roof requires more careful work and safety precautions, leading to higher labor charges. Valleys, where two roof slopes meet, often necessitate additional flashing and sealant to prevent leaks, adding to the expense. Similarly, hips (the external angle where two sloping roof surfaces meet) require specialized techniques and materials, further increasing the cost. The more intricate the roof design, the more time-consuming and potentially challenging the installation, resulting in a higher price per square foot.
Roof Removal and Disposal Costs
The cost of removing and disposing of an old roof is a significant, often overlooked, factor in the overall project expense. This cost varies depending on several factors, including the size of the roof, the type of roofing material being removed (asbestos removal, for example, is significantly more expensive and requires specialized handling), and local disposal regulations. The removal process itself involves careful dismantling of the old shingles, underlayment, and potentially other layers, which can be labor-intensive. Disposal fees are then incurred for transporting the waste to a landfill or recycling facility. For a large, multi-layered roof, these removal and disposal costs can easily amount to several hundred or even thousands of dollars, adding substantially to the overall roofing project budget. A homeowner might expect to pay between $1 and $3 per square foot for removal and disposal, but this can vary greatly depending on location and the complexity of the removal.
Labor Costs for Roofing Crews
The cost of labor is a major component of any roofing project. Labor rates vary significantly depending on the location, the experience and reputation of the roofing crew, and the current demand for roofing services. Experienced, reputable contractors often charge higher hourly rates than less experienced crews, but they may also offer superior workmanship and a stronger warranty. Highly specialized tasks, such as working on complex roof designs or dealing with difficult weather conditions, can also increase labor costs. Getting multiple quotes from different roofing contractors is essential to compare pricing and ensure you’re getting a fair price for the labor involved. Consider the trade-offs between cost and the contractor’s experience and reputation when making your decision. For instance, a lower-cost contractor might be significantly slower, ultimately increasing the overall project cost due to extended labor hours.
Material Costs Breakdown
Understanding the individual components contributing to the overall cost of an asphalt shingle roof is crucial for accurate budgeting and informed decision-making. This breakdown will analyze the price variations between different shingle brands and delve into the costs of essential supplementary materials.
Asphalt shingle costs vary significantly depending on the manufacturer, quality, and features. Premium shingles offer superior durability, aesthetics, and warranties compared to standard options, justifying their higher price point. The cost of underlayment, flashing, nails, and other accessories also adds to the total project expense. These costs, while seemingly minor individually, collectively represent a substantial portion of the overall roofing project.
Asphalt Shingle Brand Comparison
The following table compares the cost per square foot of several popular asphalt shingle brands, along with their respective warranty periods. Note that prices are approximate and can fluctuate based on location, retailer, and current market conditions. Warranties also vary depending on specific product lines and installation practices.
Brand | Approximate Cost per Square Foot | Warranty (Years) |
---|---|---|
CertainTeed Landmark® | $1.50 – $2.50 | 30-50 |
Owens Corning Duration® | $1.75 – $2.75 | 50 |
GAF Timberline HDZ® | $1.60 – $2.60 | 50 |
IKO Cambridge® | $1.25 – $2.25 | 30 |
Detailed Material Cost Breakdown
Beyond the shingles themselves, several other materials contribute significantly to the overall cost. Accurate cost estimation requires accounting for each component. Prices provided are estimates and can vary based on location, supplier, and quantity purchased.
Material | Approximate Cost per Square Foot | Description |
---|---|---|
Underlayment | $0.25 – $0.75 | Provides an extra layer of protection against moisture damage beneath the shingles. Different types exist, such as felt underlayment and synthetic underlayment, affecting the cost. |
Flashing | $0.10 – $0.50 (depending on area and type) | Metal sheets used to seal critical areas, such as valleys, chimneys, and vents, preventing water leakage. The complexity of the roof influences the quantity needed. |
Nails | $0.05 – $0.10 | Specialized roofing nails are essential for secure shingle attachment. Cost is relatively low but scales with the roof’s size. |
Starter Shingles | $0.10 – $0.20 | Provides a stable base for the first course of shingles. |
Ridge Cap Shingles | $0.15 – $0.30 | Specialized shingles used to cover the ridge of the roof. |
Sealant | $0.05 – $0.15 | Used to seal around flashing and other vulnerable areas. |
Standard vs. Premium Asphalt Shingles
The most significant price difference in asphalt shingle roofing often lies in the choice between standard and premium shingles. Standard shingles generally offer a shorter lifespan and less resistance to harsh weather conditions compared to premium options. Premium shingles usually incorporate advanced materials and manufacturing processes, resulting in enhanced durability, wind resistance, and aesthetic appeal. For example, a standard shingle might have a 20-year warranty, while a premium shingle could boast a 50-year warranty, reflecting the superior longevity and performance. This increased lifespan often offsets the higher initial cost over the long term. The choice depends on the homeowner’s budget and desired level of protection and aesthetic quality.
Labor Costs
Labor costs represent a significant portion of the overall asphalt roofing project expense, often comparable to or exceeding material costs. Understanding how these costs are calculated and what factors influence them is crucial for accurate budgeting and project planning. This section will detail the typical calculation methods and provide a range of labor costs based on project specifics.
Labor costs in asphalt roofing are typically calculated based on the number of square feet to be covered, the complexity of the job, and the prevailing hourly or daily wage rates for skilled roofing professionals in the specific region. Contractors often factor in additional time for tasks such as tear-off, underlayment installation, flashing, and cleanup. The more complex the roof, the higher the labor cost per square foot will be. For instance, a steeply pitched roof with multiple valleys and complex flashing details will require more time and specialized skills, leading to a higher labor cost than a simple, low-sloped roof.
Labor Cost Per Square Foot Ranges
Labor costs per square foot for asphalt roofing projects vary considerably depending on several factors. A simple re-roofing project on a low-slope roof might range from $1.50 to $3.00 per square foot, while a complex project involving a steep-slope roof, extensive repairs, or intricate flashing details could cost between $4.00 and $8.00 or even more per square foot. These figures are estimates and can fluctuate based on geographic location, labor market conditions, and the contractor’s overhead costs. For example, a project in a metropolitan area with a high cost of living will generally have higher labor costs than a similar project in a rural area. A large-scale project might benefit from economies of scale, potentially lowering the cost per square foot slightly.
Labor Costs for Different Roofing Installation Methods
Different asphalt roofing installation methods influence labor costs. A standard shingle installation, for instance, typically involves a straightforward process with predictable labor requirements. However, methods like modified bitumen roofing, which often require specialized equipment and expertise, will have a higher labor cost per square foot. Similarly, the installation of specialized underlayments or the inclusion of additional features such as ice and water shields can increase labor costs. For example, a project using a self-adhering modified bitumen membrane might cost more in labor due to the specialized handling and application techniques compared to a standard asphalt shingle installation. Contractors often adjust their pricing to reflect the additional time and skill required for less common installation methods.
Permits and Inspections
Obtaining the necessary permits and undergoing inspections are crucial steps in any asphalt roofing project. These processes, while adding to the overall cost, ensure the work is performed safely and according to building codes, ultimately protecting both the homeowner and the contractor. Failure to comply can result in significant delays and added expenses.
Permitting and inspection requirements vary depending on location (city, county, state), the scope of the roofing project, and the specific building codes in effect. It’s essential to understand these requirements before beginning any work to avoid costly setbacks.
Permitting Costs
The cost of obtaining building permits for asphalt roofing projects is variable, depending on factors such as the size of the roof, the complexity of the project, and the local government’s fee structure. Generally, expect to pay a base fee plus additional charges based on the square footage of the roof. For example, a small residential roof replacement might cost between $100 and $500 for the permit, while a larger commercial project could cost several thousand dollars. Some jurisdictions may also require separate permits for demolition or other aspects of the project, further increasing the total cost. It is always advisable to contact the local building department early in the planning process to obtain a precise estimate of permit fees and to understand the specific requirements for your project.
Inspection Processes and Costs
Inspections are typically conducted at various stages of the roofing project. A common sequence includes an initial inspection before work begins (to verify plans and site conditions), inspections during the installation process (to ensure proper installation techniques are being followed), and a final inspection upon completion (to confirm the roof meets all code requirements). While some jurisdictions include inspection fees within the permit cost, others charge separately for each inspection. These fees can range from $50 to $200 per inspection, depending on location and the complexity of the inspection. Failing an inspection can lead to delays while corrections are made and re-inspections are scheduled, incurring additional costs.
Cost Overruns Due to Permitting and Inspection Issues
Delays in obtaining permits can significantly impact project timelines and budgets. For example, if a permit application is incomplete or requires revisions, the project start date could be pushed back, leading to potential labor cost increases and material price fluctuations. Similarly, failing an inspection can result in rework, additional labor costs, and potentially even the need for specialized materials or expertise to rectify the issues. Consider a scenario where an inspection reveals improper underlayment installation. This would require removing and reinstalling the underlayment, adding significant cost and delaying the project’s completion. In a worst-case scenario, repeated inspection failures might necessitate the complete removal and reinstallation of the roofing system, incurring substantial expenses. Therefore, proactive planning, meticulous adherence to building codes, and clear communication with the building department are essential to mitigate these potential cost overruns.
Geographic Variations in Cost
Asphalt roofing costs, while influenced by factors discussed previously, are significantly impacted by geographical location. Variations in climate, material availability, and local labor markets create substantial differences in the final price per square foot across the United States. Understanding these regional differences is crucial for accurate budgeting and informed decision-making.
Regional differences in asphalt roofing costs stem from a complex interplay of factors. Climate significantly affects material lifespan and the need for specialized roofing techniques. Areas with harsh winters or intense sun exposure may require more durable, and therefore more expensive, roofing materials. Similarly, the availability of materials within a region influences pricing. Transportation costs, proximity to manufacturing facilities, and import/export regulations all play a role. Finally, labor costs vary widely across the country, reflecting differences in local economies, unionization rates, and the overall demand for skilled labor.
Regional Cost Comparisons
The following table presents estimated average costs per square foot for asphalt shingle roofing in three distinct regions of the U.S. These figures are averages and can vary based on the specific factors mentioned above, including the quality of materials and the complexity of the roof.
Region | Average Cost per Square Foot ($) | Contributing Factors |
---|---|---|
Northeast (e.g., New England) | $8 – $12 | Higher labor costs, potential for harsh winter conditions requiring more durable materials, potentially higher material transportation costs. |
South (e.g., Texas, Florida) | $6 – $10 | Generally lower labor costs compared to the Northeast, but potential for increased demand during hurricane season, and susceptibility to intense sun exposure. |
Midwest (e.g., Illinois, Iowa) | $7 – $11 | Labor costs are moderate, material availability is generally good, but extreme weather conditions (both heat and cold) can influence material choices. |
Illustrative Map of Regional Variations
Imagine a map of the contiguous United States. The Northeast region, encompassing states like Maine, Vermont, and New Hampshire, is shaded a darker blue, representing the higher cost range ($8-$12 per square foot). The South, including states such as Texas and Florida, is shaded a lighter blue, reflecting the lower end of the cost spectrum ($6-$10 per square foot). The Midwest, a region encompassing states like Illinois, Iowa, and Indiana, is shaded with a medium blue, signifying a cost range in between the Northeast and the South ($7-$11 per square foot). This is a simplified representation; actual costs would exhibit a more nuanced gradient across the country, influenced by the micro-economic factors at play within each state and even within specific localities. Coastal areas, for example, may experience higher costs due to increased demand and transportation challenges. Areas with a high concentration of skilled labor might see higher labor costs, offsetting lower material costs.
Impact of Roof Size on Cost
The total cost of an asphalt roof installation is directly influenced by the size of the roof. Larger roofs naturally require more materials and labor, leading to a higher overall expense. Understanding this relationship is crucial for accurate budgeting and project planning. This section will explore how roof size impacts cost and the concept of economies of scale in roofing projects.
The total cost of an asphalt roofing project generally increases linearly with the roof area. This means that if you double the roof size, you’ll roughly double the cost (excluding any unforeseen complications or significant price fluctuations in materials). This linear relationship is primarily due to the proportional increase in material requirements – more shingles, underlayment, and flashing are needed for larger roofs. Similarly, labor costs also increase proportionally as more time is required for installation. However, it’s important to note that this linear relationship isn’t always perfectly precise; economies of scale can slightly modify the overall cost.
Economies of Scale in Asphalt Roofing
Economies of scale refer to the cost advantages that arise from increased production or project size. In the context of asphalt roofing, while material costs increase proportionally, the labor costs per square foot can sometimes decrease slightly for larger projects. This is because certain fixed costs, such as project management and equipment setup, are spread across a larger area. For example, the cost of bringing a crew and equipment to a job site remains relatively constant regardless of the roof size; therefore, this fixed cost is diluted over a larger surface area. However, this effect is often marginal, and the overall cost still predominantly scales linearly with the roof area. Significant economies of scale are less likely to be observed in residential roofing projects compared to large-scale commercial projects.
Graphical Representation of Roof Size and Total Cost
Imagine a graph with roof size (in square feet) plotted on the horizontal (x) axis and total project cost (in dollars) plotted on the vertical (y) axis. The relationship would be represented by a line with a positive slope. The steeper the slope, the higher the cost per square foot. For instance, if a 1000 sq ft roof costs $10,000, and a 2000 sq ft roof costs $20,000, the line would be straight, demonstrating a consistent cost per square foot. However, slight deviations from this perfect linearity might be observed due to the minor influence of economies of scale. A slightly less steep slope for larger roof areas would visually represent the minor cost reduction per square foot due to these economies of scale. The graph would clearly illustrate that while there might be minor cost savings per square foot for larger projects, the overall project cost remains directly proportional to the roof’s surface area.
Warranty and Maintenance Costs
Understanding the warranty and potential maintenance costs associated with an asphalt roof is crucial for budgeting and long-term planning. While the initial installation cost is significant, ongoing expenses can significantly impact the overall cost of ownership over the roof’s lifespan. This section will Artikel typical warranty periods and discuss potential maintenance and repair costs.
Asphalt shingle manufacturers typically offer warranties ranging from 20 to 50 years, depending on the shingle type and quality. These warranties often cover defects in materials and workmanship, but they may not cover damage caused by extreme weather events, improper installation, or lack of maintenance. It’s vital to carefully review the specific terms and conditions of the warranty before making a purchase decision. For example, a 30-year warranty might cover material defects for the full 30 years but only cover labor for the first 10. Understanding these nuances is critical.
Warranty Periods for Asphalt Shingles
The length of an asphalt shingle warranty significantly impacts the perceived value and long-term cost of the roof. Shorter warranties, while often less expensive upfront, may lead to higher replacement costs sooner. Conversely, longer warranties offer greater peace of mind, although the initial cost of the shingles might be higher. The type of shingle also plays a role; premium shingles generally come with longer warranties than standard shingles. For example, a basic 3-tab shingle might offer a 20-year warranty, while a high-end architectural shingle could offer a 50-year warranty. This difference reflects the superior material quality and construction of the more expensive option.
Long-Term Maintenance Costs
Regular maintenance can significantly extend the lifespan of an asphalt roof and reduce the likelihood of unexpected repairs. This includes routine inspections (ideally twice a year, in spring and fall) to check for damaged or missing shingles, clogged gutters, and signs of moss or algae growth. Cleaning gutters regularly prevents water damage, and addressing moss or algae promptly prevents deterioration of the shingles. These preventative measures are significantly less expensive than major repairs. For instance, replacing a few damaged shingles costs a fraction of what a full roof replacement would cost.
Unexpected Repair Costs
Even with regular maintenance, unexpected repairs can arise. Severe weather events such as hailstorms, hurricanes, or strong winds can cause significant damage, requiring extensive repairs or even a complete roof replacement. These events are unpredictable and can result in substantial, unbudgeted expenses. For example, a hailstorm could damage hundreds of shingles, leading to a costly repair bill. Similarly, a tree falling onto the roof during a storm could necessitate a significant portion of the roof being replaced. Another example would be the unnoticed gradual deterioration of the underlayment, which might only be discovered during a routine inspection, potentially requiring more extensive repairs than simply replacing shingles. Such unforeseen events highlight the importance of having adequate homeowner’s insurance coverage.
Comparing Asphalt Roofing to Other Materials
Choosing the right roofing material involves careful consideration of various factors, including cost, durability, aesthetic appeal, and lifespan. Asphalt shingles are a popular choice due to their affordability, but other options like tile, metal, and wood offer distinct advantages and disadvantages. This section compares asphalt roofing to these alternatives, providing a comprehensive overview to aid in informed decision-making.
Asphalt Shingle Roofing Compared to Other Materials
Asphalt shingles consistently rank among the most economical roofing options. However, their lifespan is generally shorter than other materials, and their aesthetic versatility is limited compared to options like tile or wood shake. The following table summarizes the key differences in cost, durability, and aesthetics across various roofing materials. Note that prices are estimates and can vary significantly based on geographic location, material quality, and labor costs.
Material | Cost per Square Foot (Estimate) | Durability | Aesthetics | Lifespan (Years) |
---|---|---|---|---|
Asphalt Shingles | $2-$8 | Moderate; susceptible to damage from extreme weather and UV degradation | Limited variety; typically available in various colors and textures | 15-30 |
Clay Tile | $8-$20 | High; resistant to fire, wind, and impact damage | Wide variety; available in numerous colors, shapes, and textures; often associated with Mediterranean or Spanish styles | 50-100+ |
Metal Roofing (Steel or Aluminum) | $7-$20 | High; highly resistant to fire, wind, and impact damage; long lifespan | Increasing variety; available in various colors and profiles to mimic other materials or create a modern look | 50-75+ |
Wood Shake/Shingles | $10-$25 | Moderate to High (depending on treatment); susceptible to fire, rot, and insect damage; requires regular maintenance | Rustic and natural appearance; offers a unique aesthetic | 20-40 |
Advantages and Disadvantages of Each Roofing Material
The choice of roofing material is a significant investment that impacts both the aesthetic appeal and the longevity of a home. Understanding the advantages and disadvantages of each material is crucial for making an informed decision. For instance, while asphalt shingles offer a low initial cost, their shorter lifespan may lead to higher replacement costs over time. Conversely, while metal roofing boasts superior durability and longevity, its initial cost is considerably higher.
Finding Reliable Contractors
Choosing the right contractor is crucial for a successful asphalt roofing project. A reputable contractor ensures quality workmanship, uses appropriate materials, and adheres to safety standards, ultimately protecting your investment and preventing future headaches. Selecting a contractor involves careful research and due diligence.
Finding a qualified and trustworthy asphalt roofing contractor requires a multi-faceted approach. Thorough vetting will save you time, money, and potential future problems.
Contractor Research and Selection Methods
Several avenues exist for identifying potential contractors. Checking online directories, seeking referrals from trusted sources, and verifying licensing and insurance are essential steps. Utilizing online review platforms can provide insights into past customer experiences. Directly contacting several contractors to discuss your project is a vital part of the process.
Importance of Obtaining Multiple Quotes
Obtaining at least three quotes from different contractors is highly recommended. Comparing quotes allows for a comprehensive evaluation of pricing, materials, and proposed timelines. This competitive bidding process ensures you receive the most favorable terms and avoids overpaying for the services. Discrepancies between quotes should prompt further investigation to understand the rationale behind the differences. For example, one quote might specify higher-quality materials, while another might offer a faster turnaround time.
Key Aspects of Contractor Bid Review
Carefully reviewing contractor bids is essential. Key aspects to consider include the detailed breakdown of costs (materials, labor, permits), the proposed project timeline, the contractor’s experience and qualifications, references from previous clients, and the warranty offered. A well-structured bid should clearly Artikel all aspects of the project, leaving no room for ambiguity. Pay close attention to the specific materials being used, as higher-quality materials often correlate with a longer lifespan and better protection for your home. For instance, a bid specifying a 30-year architectural shingle will likely cost more than one using a standard 20-year shingle, but the investment will likely pay off in the long run. Also, ensure the contractor’s insurance covers potential liabilities and damages during the project. Requesting and verifying references allows you to assess the contractor’s past performance and reliability directly from previous clients.
Hidden Costs in Asphalt Roofing: Asphalt Roof Cost Per Square Foot
Planning a new asphalt roof involves more than just the upfront cost of materials and labor. Several hidden expenses can significantly inflate the final bill if not carefully considered during the budgeting process. Understanding these potential costs allows homeowners to create a more realistic budget and avoid unpleasant financial surprises during the project.
Unexpected expenses are a common occurrence in home renovation projects, and roofing is no exception. Thorough contingency planning is crucial to mitigate the financial impact of these unforeseen events. Allocating a specific percentage of the total budget for unexpected costs demonstrates responsible financial management and prevents potential project delays or compromises in quality.
Unforeseen Material Needs, Asphalt roof cost per square foot
Discovering additional material requirements during the roofing process is a frequent source of hidden costs. For example, unexpectedly damaged sheathing might necessitate repairs or replacements before new roofing can be installed, adding to the material expense. Similarly, discovering extensive rot or damage under the existing shingles, requiring more extensive repairs than initially anticipated, can significantly increase material costs. These extra materials, alongside the associated labor to install them, can add hundreds or even thousands of dollars to the overall project cost.
Unanticipated Structural Issues
Underlying structural problems can emerge during roof tear-off, leading to unexpected expenses. Issues such as decaying or damaged roof trusses, weakened rafters, or inadequate ventilation systems might require professional repairs before new roofing can be installed safely and effectively. The cost of addressing these structural problems can be substantially higher than the cost of the roofing materials themselves, potentially doubling or tripling the initial budget. For instance, a homeowner expecting a $10,000 roofing job might face an additional $5,000 to $15,000 in structural repairs if significant rot is discovered in the underlying framework.
Permitting and Inspection Fees
While permits and inspections are often included in initial estimates, additional fees can arise due to unforeseen complications. For example, if the initial permit application is incomplete or requires revisions, extra fees might be incurred. Similarly, if inspection reveals issues that need to be rectified before final approval, this can also lead to unexpected costs, delaying the project completion. These costs, although seemingly minor individually, can accumulate and noticeably impact the final project budget. In some localities, these fees can amount to several hundred dollars.
Waste Removal and Disposal
The disposal of old roofing materials is often overlooked. Depending on local regulations and the volume of waste generated, the cost of proper disposal can be substantial. Some contractors include this in their quote, but many do not, leaving homeowners responsible for managing and paying for the removal and disposal of the old roofing materials, adding an additional cost that can range from a few hundred to over a thousand dollars depending on the size of the roof and local disposal fees.
Contingency Planning for Unexpected Expenses
To effectively mitigate the risk of hidden costs, a contingency plan is essential. A reasonable approach is to allocate 10-20% of the total estimated project cost as a contingency fund. This fund acts as a buffer to absorb unexpected expenses, ensuring the project can proceed without compromising quality or causing significant financial strain. For example, if the initial estimate is $10,000, a contingency fund of $1,000 to $2,000 would be prudent. This proactive measure provides peace of mind and allows for flexibility in addressing unforeseen issues that may arise during the roofing process.
Clarifying Questions
Asphalt roof cost per square foot – What is the lifespan of an asphalt shingle roof?
The lifespan of an asphalt shingle roof typically ranges from 15 to 30 years, depending on the shingle quality, climate, and maintenance.
Can I install an asphalt roof myself?
While possible, DIY asphalt roof installation is generally not recommended due to safety concerns and the potential for costly mistakes. Professional installation ensures proper technique and warranty coverage.
How do I find a reputable roofing contractor?
Seek referrals, check online reviews, verify licenses and insurance, and obtain multiple bids before selecting a contractor. Confirm their experience with asphalt shingle installations.
What is included in a roofing contractor’s quote?
A comprehensive quote should detail material costs, labor charges, permits, waste removal, and any additional services. Clarify any exclusions upfront.