Cost Analysis of Asphalt Shingle Replacement
Replacing your asphalt shingles is a significant investment, and understanding the associated costs is crucial for budgeting and planning. This section provides a breakdown of average costs, influencing factors, and comparisons to help you make informed decisions.
Average Costs for Asphalt Shingle Replacement
The cost of asphalt shingle replacement varies considerably depending on several factors, primarily roof size and complexity. A smaller, simple roof will naturally cost less than a large, complex one with multiple gables, valleys, or dormers. Labor costs, material prices, and the need for permits all contribute to the overall expense. For example, a small, 1,000 square foot roof might cost between $8,000 and $12,000, while a large, complex 3,000 square foot roof could range from $24,000 to $40,000 or more. These figures are averages and can vary significantly based on geographic location and market conditions. Always obtain multiple quotes to compare pricing.
Pricing Structures of Roofing Contractors
Different roofing contractors utilize various pricing structures. Some charge by the square (100 square feet), others by the hour, and some offer fixed-price contracts for the entire project. Factors influencing price variations include the contractor’s experience and reputation, the type of shingles used, the complexity of the roof, the inclusion of additional services (such as tear-off and disposal of old materials), and the prevailing labor and material costs in the region. A highly experienced and reputable contractor may charge more per square than a less established one, but this often reflects higher quality workmanship and materials.
Cost-Effectiveness of Different Asphalt Shingle Types
The table below compares the cost-effectiveness of different asphalt shingle types, considering average cost, lifespan, and maintenance needs. Choosing the right shingle type is a balance between upfront cost and long-term value. Higher initial investment in a longer-lasting shingle may save money in the long run by reducing the frequency of replacements.
Shingle Type | Average Cost per Square | Lifespan (Years) | Maintenance Requirements |
---|---|---|---|
3-Tab | $100 – $150 | 15-20 | Minimal; occasional cleaning |
Architectural (Dimensional) | $150 – $250 | 25-30 | Minimal; occasional cleaning |
Luxury/Premium | $250+ | 30+ | Minimal; occasional cleaning |
Materials and Their Properties
Choosing the right asphalt shingles is crucial for a durable and aesthetically pleasing roof. The lifespan and overall performance of your roof are directly impacted by the materials used. Understanding the different types available and their properties will help you make an informed decision.
Asphalt shingle replacement – Asphalt shingles are the most common roofing material in North America, offering a balance of affordability, durability, and aesthetic appeal. They are composed primarily of asphalt, a petroleum-based material, and a reinforcing mat. This mat can be made from either fiberglass or organic felt, leading to two distinct shingle types.
Asphalt Shingle Types: Composition, Durability, and Aesthetics
Several types of asphalt shingles exist, each with its own characteristics. Three-tab shingles are the most basic and economical, featuring a simple three-tab design. Architectural shingles, also known as dimensional shingles, offer a more complex, textured appearance with thicker construction and enhanced durability. Luxury shingles often incorporate heavier asphalt saturation, enhanced weathering properties, and premium aesthetic features such as thicker profiles and more intricate designs. The choice depends on budget, desired aesthetic, and expected lifespan. For instance, a three-tab shingle might be suitable for a smaller budget and shorter lifespan expectation, while architectural shingles would be more appropriate for a longer-lasting, higher-quality roof.
Fiberglass vs. Organic Asphalt Shingles, Asphalt shingle replacement
The core difference lies in the reinforcing mat. Fiberglass shingles use a woven fiberglass mat, while organic shingles utilize a felt mat made from recycled paper saturated with asphalt. This fundamental difference significantly impacts the shingles’ properties.
Feature | Fiberglass Shingles | Organic Shingles |
---|---|---|
Weight | Lighter | Heavier |
Durability | More resistant to wind damage, generally longer lifespan | Less resistant to wind damage, shorter lifespan |
Moisture Resistance | Better resistance to moisture damage | More susceptible to moisture damage |
Cost | Generally more expensive upfront | Generally less expensive upfront |
Appearance | Wide variety of styles and colors | Fewer style options available |
Selecting Asphalt Shingles for Different Climate Conditions
Climate plays a significant role in shingle selection. Certain features are crucial for optimal performance in various weather conditions.
- High Wind Areas: Select shingles with a high wind resistance rating and consider using additional fasteners for enhanced security. The heavier weight of architectural shingles generally offers better wind resistance than three-tab shingles.
- Heavy Snowfall Areas: Choose shingles with a high snow load capacity and consider a steeper roof pitch to facilitate snow shedding. Shingles with a heavier weight and interlocking design can better withstand heavy snow accumulation.
- Hot, Sunny Climates: Opt for shingles with high reflectivity (cool roof technology) to reduce heat absorption and minimize attic temperatures. Darker colored shingles absorb more heat than lighter colored shingles, and this can affect attic temperatures in hot climates.
- Coastal Areas: Select shingles with superior resistance to salt spray and moisture damage. Some manufacturers offer shingles specifically designed for coastal environments with enhanced protection against corrosion and deterioration.
Installation Process and Techniques
Asphalt shingle roof replacement is a multi-stage process requiring skilled labor and adherence to best practices to ensure a durable and long-lasting roof. The entire process, from initial tear-off to final cleanup, demands precision and attention to detail at each step. This section details the typical steps involved in a complete asphalt shingle roof replacement project.
The installation process begins with a thorough tear-off of the existing roofing material. This involves carefully removing old shingles, underlayment, and any damaged or deteriorated components. Proper disposal of the waste material is crucial, adhering to local environmental regulations. Following the tear-off, the roof deck is inspected for any damage, such as rot, warping, or loose boards. Necessary repairs, including replacing damaged sections of plywood or adding additional sheathing for reinforcement, are undertaken before proceeding to the next stage.
Roof Deck Preparation and Underlayment Installation
Proper preparation of the roof deck is paramount to the success of the project. This includes thoroughly cleaning the deck of debris and ensuring all fasteners are securely in place. Any damaged areas must be repaired or replaced before installing the underlayment. The underlayment acts as a secondary water barrier, providing additional protection against leaks should the shingles fail. There are various types of underlayment available, including felt paper and synthetic options, each offering different levels of protection and durability. Proper installation involves overlapping the underlayment sheets to create a continuous waterproof layer, ensuring that all seams are securely fastened and sealed to prevent water penetration. The type and quality of underlayment significantly impact the roof’s longevity and resistance to moisture damage. For instance, using a high-quality synthetic underlayment offers superior protection compared to standard felt paper, potentially extending the roof’s lifespan by several years.
Asphalt Shingle Installation
Once the underlayment is installed, the asphalt shingles are applied. This process begins at the eaves (the lowest part of the roof) and progresses upward, following the manufacturer’s recommended installation guidelines. Each shingle course is carefully aligned and nailed securely to the roof deck, ensuring proper overlap to prevent water penetration. Special attention is given to the valleys, ridges, and hips of the roof, which are areas prone to water accumulation. These areas typically require additional underlayment and sealant to ensure complete water resistance. Proper shingle installation includes maintaining consistent shingle exposure, which is the visible portion of the shingle. This ensures a uniform and aesthetically pleasing finish while maintaining optimal protection. Failure to maintain consistent exposure can compromise the roof’s structural integrity and its ability to withstand extreme weather conditions.
Flashing and Trim Installation
Flashing, a thin metal sheet, is installed around chimneys, vents, and other roof penetrations to prevent water from entering the roof. Proper flashing installation is crucial in preventing leaks. The flashing is carefully installed, ensuring a watertight seal around all penetrations. The trim, including the rake boards, gable ends, and ridge caps, is installed to provide a finished look and added protection to the roof edges.
Final Cleanup and Inspection
After the shingle installation is complete, a thorough cleanup is conducted to remove any debris or leftover materials. A final inspection is then performed to ensure that all aspects of the installation meet the required standards. This includes verifying proper shingle alignment, nail placement, flashing installation, and overall roof integrity. Any necessary adjustments or repairs are made before the project is considered complete. A well-executed final inspection guarantees a high-quality, durable, and long-lasting roof.
Flowchart Illustrating Asphalt Shingle Replacement
The following flowchart illustrates the sequence of actions in a typical asphalt shingle replacement project:
[Start] –> [Tear-off of old shingles and underlayment] –> [Roof deck inspection and repair] –> [Underlayment installation] –> [Asphalt shingle installation] –> [Flashing and trim installation] –> [Final cleanup and inspection] –> [Project Completion]
Roofing Underlayment Options
Choosing the right roofing underlayment is crucial for the longevity and performance of your new asphalt shingle roof. Underlayment acts as a secondary water barrier, protecting your roof deck from moisture damage in case the shingles fail. Selecting the appropriate type depends on factors like climate, budget, and the desired level of protection.
Roofing underlayments are broadly categorized into felt underlayments and synthetic underlayments. Each type offers a unique set of properties and benefits, influencing its suitability for specific roofing projects.
Felt Underlayments
Felt underlayments, traditionally made from asphalt-saturated organic or fiberglass mats, are a cost-effective option. Organic felt is typically less expensive but degrades faster than fiberglass felt, which offers improved durability and UV resistance. However, both types are susceptible to tearing and are less effective in preventing water penetration compared to synthetic options. Their primary benefit lies in their affordability. Proper installation is essential to ensure their effectiveness as a secondary water barrier.
Synthetic Underlayments
Synthetic underlayments, typically made from polyethylene or polypropylene, offer superior performance compared to felt underlayments. They are more resistant to tearing, punctures, and water damage. Many synthetic underlayments also boast enhanced UV resistance, allowing them to withstand prolonged sun exposure without significant degradation. This extended lifespan translates to better long-term protection for your roof. While generally more expensive upfront, the increased durability often leads to cost savings in the long run by reducing the risk of future repairs or replacements. Some synthetic options also offer improved slip resistance, making them safer for installers to work with on steep roofs.
Comparison of Underlayment Options
The table below compares three common underlayment options, highlighting their key features and approximate costs. Note that costs can vary depending on the manufacturer, supplier, and regional factors.
Product Name | Material Type | Key Features | Cost (per square) |
---|---|---|---|
Standard Asphalt-Saturated Felt | Organic Felt | Affordable, readily available | $0.50 – $1.00 |
Fiberglass Felt | Fiberglass Felt | More durable than organic felt, better UV resistance | $1.00 – $1.50 |
Synthetic Underlayment (e.g., polyethylene) | Polyethylene | High tear strength, excellent water resistance, superior UV resistance | $1.50 – $3.00 |
Warranty and Insurance Considerations
Replacing your asphalt shingles is a significant investment, and understanding the warranty and insurance implications is crucial for protecting that investment and ensuring a smooth process. This section details the typical warranty coverage offered by manufacturers, the conditions that might void those warranties, and the importance of securing necessary permits and insurance.
Asphalt shingle manufacturers typically offer warranties that cover defects in materials and workmanship for a specified period. These warranties vary depending on the shingle type and manufacturer, but common durations include 20-30 years for the shingle’s structural integrity and a shorter period (often 10-15 years) for its aesthetic qualities like color fading. It is vital to carefully review the specific terms and conditions of the warranty provided with your chosen shingles.
Manufacturer Warranties and Voiding Conditions
Manufacturer warranties are designed to protect homeowners from defects in the shingles themselves. However, several factors can void these warranties. Common causes include improper installation (not following the manufacturer’s guidelines), damage caused by extreme weather events beyond the scope of the warranty (e.g., hurricane-force winds), neglect or lack of proper maintenance, and use of incompatible underlayment or other roofing materials. For example, a warranty might be voided if the shingles are not properly nailed, leading to premature failure, or if the homeowner fails to address minor damage promptly, allowing it to escalate into a larger problem. It’s crucial to keep a copy of your warranty and understand its limitations.
Permitting and Insurance Requirements
Obtaining the necessary permits before beginning any roofing work is essential. Building codes and regulations vary by location, but permits ensure that the work meets local standards and that the project is properly inspected. Failing to obtain permits can result in fines, delays, or even the requirement to redo the work. Moreover, adequate insurance coverage is crucial to protect both the homeowner and the roofing contractor. This typically includes general liability insurance for the contractor, covering potential accidents or injuries during the installation process, and potentially workers’ compensation insurance if the contractor employs others. Homeowners’ insurance should also cover potential damage to the property during the project. A reputable contractor will have the necessary insurance documentation readily available.
Common Warranty Clauses
Many roofing warranties contain specific clauses that Artikel the responsibilities of both the manufacturer and the homeowner. A common clause might specify that the warranty is only valid if the shingles are installed by a qualified and certified installer. Another clause might address limitations on coverage for damage caused by acts of God, such as hailstorms or tornadoes. A typical clause might state that the manufacturer’s liability is limited to the replacement of defective shingles, excluding labor costs for removal and reinstallation. Understanding these clauses is critical for resolving any potential warranty claims. For instance, a clause limiting coverage to material defects only would mean that labor costs for repairs resulting from a manufacturing defect may not be covered.
Choosing a Qualified Roofing Contractor
Selecting the right roofing contractor is crucial for a successful asphalt shingle replacement project. A qualified contractor ensures quality workmanship, adherence to building codes, and a smooth process from start to finish. This section will guide you through the key considerations when choosing a contractor for your roofing needs.
Contractor Qualifications and Credentials
Choosing a reputable contractor involves verifying their licensing, insurance, and experience. A properly licensed contractor demonstrates adherence to professional standards and provides a level of accountability. Comprehensive insurance, including workers’ compensation and liability coverage, protects you from potential financial risks associated with accidents or damages during the project. Thorough background checks and verification of licenses and insurance should be a standard part of the selection process. Finally, reviews and testimonials from past clients offer valuable insights into the contractor’s reliability, professionalism, and the quality of their work. Look for consistent positive feedback and address any negative reviews directly with the contractor to understand their response and resolution strategies.
Types of Contractor Contracts and Key Clauses
Several types of contracts exist for roofing projects, including fixed-price contracts, time-and-materials contracts, and cost-plus contracts. A fixed-price contract offers a predetermined total cost, providing budget certainty. Time-and-materials contracts charge for labor and materials used, making the final cost potentially variable. Cost-plus contracts involve reimbursing the contractor for all expenses plus a markup for profit. Key clauses to look for in any contract include a detailed scope of work, payment schedule, warranty information, start and completion dates, and dispute resolution mechanisms. The contract should clearly define the materials used, their quality, and any guarantees provided. Furthermore, it’s crucial to have a clear understanding of the payment terms, including the percentage of payment required upfront, progress payments, and the final payment upon project completion. Finally, the contract should Artikel a clear process for handling disputes or unexpected issues that may arise during the project. A well-defined dispute resolution mechanism can save time and money in the long run.
Obtaining and Evaluating Multiple Bids
Obtaining multiple bids from different contractors is a crucial step in ensuring a competitive price and selecting the best contractor for your needs. Begin by contacting at least three to five reputable contractors, providing them with a detailed description of your project requirements. Request detailed proposals that include a comprehensive breakdown of costs, materials, labor, and the project timeline. Compare the bids based on factors such as total cost, proposed materials, warranty offerings, and the contractor’s experience and reputation. Remember to carefully review each proposal for any discrepancies or unclear terms before making a decision. Don’t hesitate to ask clarifying questions to ensure you fully understand each bid. Consider factors beyond just price, such as the contractor’s communication style, responsiveness to your inquiries, and overall professionalism. The most cost-effective bid may not always be the best choice if the contractor lacks experience, proper licensing, or insurance. A balanced approach that considers both price and contractor qualifications is essential.
Environmental Impact of Asphalt Shingle Replacement
Asphalt shingle replacement projects, while necessary for maintaining roof integrity and protecting homes, have a significant environmental footprint. Understanding this impact is crucial for homeowners and contractors alike, allowing for informed decisions and the implementation of sustainable practices. This section will explore the environmental considerations associated with the entire lifecycle of asphalt shingles, from manufacturing to disposal.
Asphalt shingle disposal and recycling present considerable environmental challenges. Millions of tons of discarded shingles end up in landfills each year, contributing to land overuse and potential groundwater contamination from leaching materials. The composition of asphalt shingles – a mixture of asphalt, fiberglass, and mineral granules – makes them slow to decompose.
Disposal of Old Asphalt Shingles and Recycling Options
The disposal of old asphalt shingles is a major environmental concern. Landfills are often the default option, but this contributes to the depletion of natural resources and potential environmental hazards. However, several recycling options are becoming increasingly available. These include repurposing the shingles as aggregate in road construction, using them as a component in new asphalt products, or processing them into granules for use in other applications. The effectiveness of these recycling programs varies depending on location and the availability of appropriate processing facilities. Some municipalities have implemented programs to incentivize shingle recycling, while others are still exploring options. For example, some regions offer curbside pickup for roofing waste, making recycling more convenient and accessible. The growth of these initiatives suggests a growing awareness of the need for sustainable waste management practices in the roofing industry.
Environmental Impact of Asphalt Shingle Manufacturing and Transportation
The manufacturing process of asphalt shingles is energy-intensive, relying heavily on fossil fuels. The extraction and processing of raw materials, such as asphalt and fiberglass, contribute to greenhouse gas emissions. Furthermore, the transportation of these materials from manufacturing plants to distribution centers and ultimately to construction sites adds to the overall carbon footprint. The energy used in the transportation of these heavy materials adds to air pollution, and the extensive trucking required contributes to traffic congestion. For example, a large-scale roofing project might require multiple truck deliveries, each adding to the environmental impact. Choosing locally sourced materials can help mitigate the transportation-related environmental impact.
Minimizing the Environmental Footprint of Asphalt Shingle Replacement
Several strategies can help minimize the environmental impact of an asphalt shingle replacement project. Selecting shingles with a high percentage of recycled content reduces the demand for new materials and decreases landfill waste. Proper disposal and recycling of old shingles, through programs like those mentioned previously, is also crucial. Additionally, choosing a contractor committed to sustainable practices and efficient waste management can significantly reduce the project’s overall environmental footprint. For instance, a contractor might use specialized equipment to efficiently remove and transport waste, minimizing fuel consumption and transportation emissions. Furthermore, opting for energy-efficient installation methods can further reduce the overall environmental impact of the project.
Common Problems and Solutions
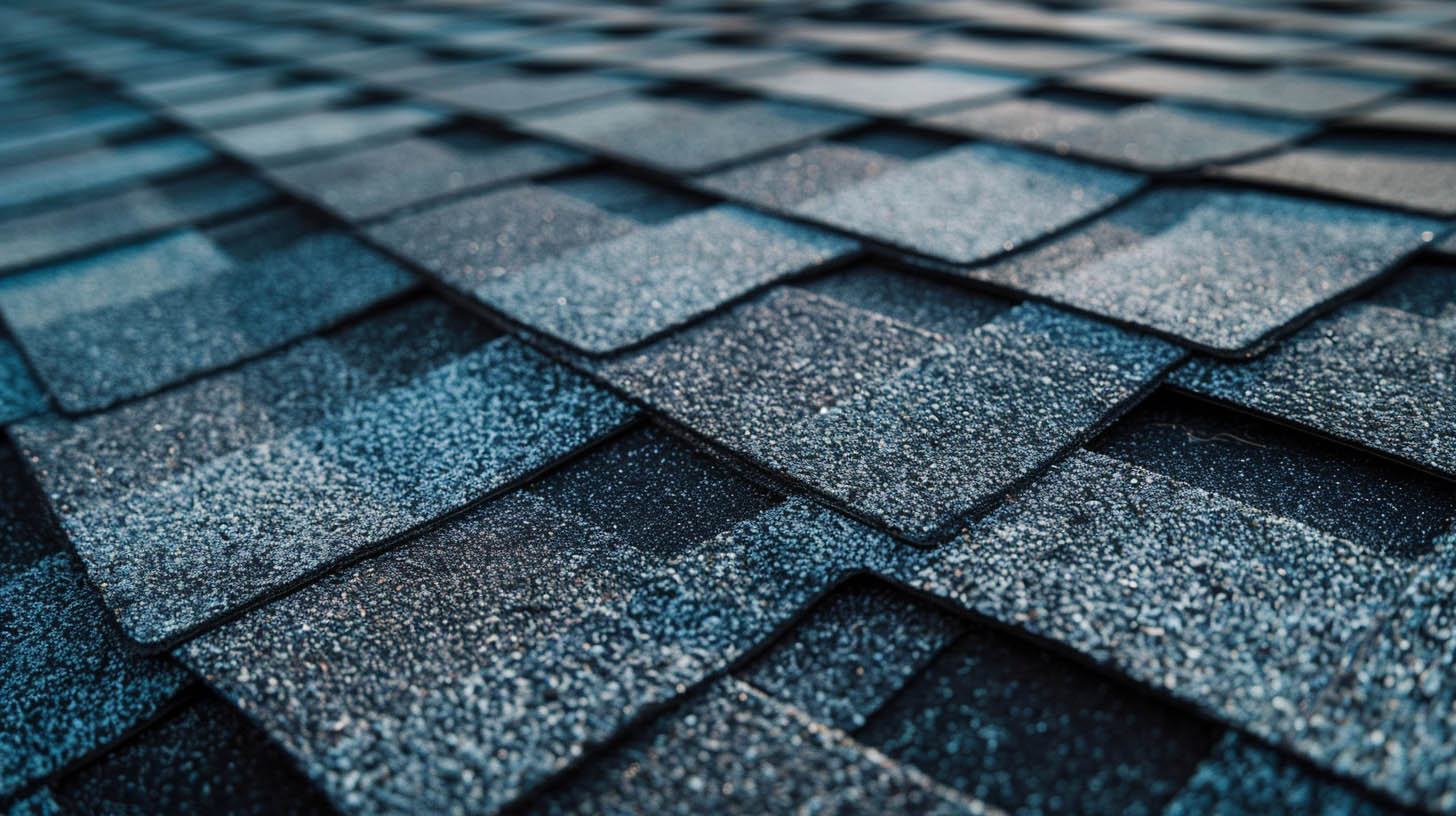
Asphalt shingle roof replacements, while improving your home’s protection and curb appeal, can sometimes present challenges. Understanding common problems and their solutions is crucial for a successful project and long-lasting roof. This section details typical issues encountered during asphalt shingle roof replacement and offers practical solutions to prevent and address them. Proper planning and skilled installation are key to minimizing these problems.
Shingle Curling and Blistering
Shingle curling, where the edges of shingles lift and curl upward, and blistering, where raised bumps appear on the shingle surface, are common problems often stemming from improper installation or material defects. These issues compromise the roof’s weather resistance, leading to leaks and premature deterioration.
- Problem: Improper nailing – Nails driven too deeply or too shallowly can cause shingles to curl or blister. Incorrect spacing between nails can also contribute.
- Solution: Ensure proper nailing techniques are followed during installation. Use the recommended nail length and spacing specified by the shingle manufacturer. Avoid overdriving or underdriving nails.
- Problem: Inadequate ventilation – Poor attic ventilation can trap moisture, causing shingles to lift and blister.
- Solution: Ensure adequate attic ventilation to prevent moisture buildup. This may involve installing ridge vents, soffit vents, or gable vents. Proper insulation also plays a crucial role in managing moisture levels.
- Problem: Defective shingles – Manufacturing defects or damage during transportation can lead to curling and blistering.
- Solution: Inspect shingles carefully upon delivery and before installation. Report any damaged or defective shingles to the supplier immediately. Use only high-quality shingles from reputable manufacturers.
Algae Growth
Algae growth, often appearing as dark streaks or discoloration on the shingles, is a common aesthetic problem that doesn’t necessarily compromise the structural integrity of the roof, but it detracts from the appearance and can indicate potential moisture issues.
- Problem: Shaded areas and moisture retention – Algae thrive in shaded, damp environments. Poor ventilation can exacerbate the problem.
- Solution: Improve ventilation to reduce moisture. Consider trimming overhanging branches to increase sunlight exposure. Regular cleaning with a specialized algae-removing solution can also help.
- Problem: Use of untreated wood – Untreated wood underlayment can provide a nutrient source for algae growth.
- Solution: Use treated wood or a non-organic underlayment to prevent algae growth.
- Problem: Lack of preventative treatment – Some shingles are treated with algae-resistant chemicals. The absence of this treatment increases susceptibility.
- Solution: Select shingles that include algae-resistant treatment during the selection process. This is a preventative measure that can save considerable time and effort in the long run.
Water Leaks
Water leaks are a serious problem that can lead to significant damage to the home’s interior. They often result from improper installation or damage to the roofing system.
- Problem: Flashing issues – Improperly installed flashing around chimneys, vents, and other roof penetrations can lead to leaks.
- Solution: Ensure proper flashing installation. Use high-quality flashing materials and follow manufacturer instructions carefully. Regular inspection of flashing is vital.
- Problem: Damaged shingles – Cracked, broken, or missing shingles create pathways for water entry.
- Solution: Regularly inspect the roof for damaged shingles and replace them promptly. A preventative inspection is beneficial after any severe weather event.
- Problem: Inadequate underlayment – Insufficient or damaged underlayment can allow water to penetrate the roof deck.
- Solution: Use a high-quality underlayment that provides adequate protection. Ensure proper installation of the underlayment to prevent gaps or overlaps.
Maintenance and Longevity: Asphalt Shingle Replacement
Proper maintenance significantly extends the lifespan of an asphalt shingle roof, delaying costly repairs and premature replacement. Regular inspections and timely attention to minor issues can prevent small problems from escalating into major, and expensive, headaches. This section details a recommended maintenance schedule and identifies signs indicating the need for repair or replacement.
Regular maintenance is key to maximizing the lifespan of your asphalt shingle roof, often adding years to its useful life. Neglecting maintenance, on the other hand, can lead to accelerated deterioration and significantly reduce the roof’s longevity. A proactive approach to roof care translates to significant cost savings in the long run.
Routine Maintenance Schedule
A simple, regular maintenance schedule can help detect and address problems before they become serious. This schedule Artikels tasks homeowners should perform to keep their roofs in optimal condition.
- Annual Inspection (Spring/Fall): Conduct a thorough visual inspection of the roof from the ground and, if safely possible, from the attic. Look for missing, damaged, or curled shingles; signs of moss or algae growth; and any signs of leaks or water damage. Pay close attention to valleys, flashing around chimneys and vents, and areas prone to wind damage.
- Gutter Cleaning (Twice Yearly): Clean gutters and downspouts of debris at least twice a year (spring and fall). Clogged gutters can lead to water damage and ice dams in colder climates.
- Tree Trimming (As Needed): Keep tree branches trimmed away from the roof to prevent damage from falling limbs and to reduce the accumulation of leaves and debris.
- Moss and Algae Removal (As Needed): Remove moss and algae growth promptly to prevent damage to the shingles and underlying materials. A gentle pressure washing may be sufficient, or a specialized moss and algae treatment may be necessary.
Signs Indicating Repair or Replacement
Several clear signs indicate the need for asphalt shingle repair or replacement. Ignoring these signs can lead to more extensive and costly damage.
- Missing or Damaged Shingles: Missing or severely damaged shingles are obvious signs requiring immediate attention. Wind damage, aging, and impact from falling objects are common causes.
- Curling or Cupping Shingles: Shingles that curl upward (cupping) or downward (curling) indicate deterioration and potential moisture penetration. This is often a sign of aging or moisture damage.
- Granule Loss: Significant granule loss exposes the underlying asphalt, making the shingles more vulnerable to damage from the elements. This often indicates the shingles are nearing the end of their lifespan.
- Leaks and Water Damage: Water stains on ceilings or walls, damp insulation, or musty odors are clear indicators of a roof leak requiring immediate professional attention.
- Sagging Roofline: A noticeable sagging or unevenness in the roofline suggests structural issues requiring immediate professional assessment. This could indicate significant underlying damage.
Preventing Costly Repairs and Premature Replacement
Proactive maintenance significantly reduces the likelihood of costly repairs and premature roof replacement.
Regular inspections, prompt attention to minor issues, and proper gutter maintenance can add years to the life of your asphalt shingle roof and save you thousands of dollars in the long run.
For example, addressing a minor leak promptly prevents water damage from spreading to the roof decking and attic, potentially saving thousands of dollars in repairs. Similarly, regular gutter cleaning prevents water damage to the fascia and soffit, reducing the need for expensive repairs or replacements. A roof that is properly maintained and regularly inspected can easily outlast its expected lifespan.
Question & Answer Hub
How long does asphalt shingle replacement typically take?
The duration varies depending on roof size and complexity, but generally ranges from a few days to several weeks.
Can I replace shingles myself?
While possible for smaller repairs, a complete roof replacement is best left to experienced professionals due to safety and complexity.
What is the lifespan of asphalt shingles?
Lifespan varies depending on shingle type, climate, and maintenance; expect 15-30 years.
How often should I inspect my roof?
At least twice a year, spring and fall, checking for damage, missing shingles, or signs of wear.