Types of Roofing Shingles and Their Price Ranges
Choosing the right roofing shingles involves considering a balance of aesthetics, durability, and budget. Different shingle types offer varying levels of protection, lifespan, and initial cost. Understanding these factors is crucial for making an informed decision.
Asphalt Shingles
Asphalt shingles are the most common type due to their affordability and wide availability. They come in a variety of styles, colors, and thicknesses, impacting both their price and performance. Three-tab asphalt shingles are the most basic and least expensive, while architectural (dimensional) shingles offer a more upscale look and greater durability. Factors such as the shingle’s weight, composition (fiberglass or organic), and warranty length also influence pricing. Generally, three-tab asphalt shingles range from $0.50 to $1.50 per square foot, while architectural shingles cost between $1.50 and $4.00 per square foot, installed. Higher-end architectural shingles with enhanced features like thicker material or impact resistance can exceed this range.
Wood Shingles
Wood shingles, typically made from cedar or redwood, offer a natural and aesthetically pleasing look. However, they are more expensive than asphalt shingles and require more maintenance due to their susceptibility to rot, insect damage, and fire. The cost of wood shingles varies significantly depending on the type of wood, thickness, and quality, ranging from $4.00 to $10.00 or more per square foot, installed. Their longer lifespan, if properly maintained, can offset the higher initial cost over the long term. Regular treatment with fire retardant and protective sealants is essential to prolong their life.
Tile Shingles
Tile shingles, including clay and concrete, are known for their exceptional durability and longevity. They are significantly more expensive than asphalt or wood shingles but offer superior resistance to weather damage and fire. Clay tiles generally cost more than concrete tiles. Installation costs are also higher due to the weight and specialized handling required. Expect to pay between $8.00 and $25.00 or more per square foot, installed, depending on the type of tile and installation complexity. The higher upfront cost is often justified by their extremely long lifespan – often exceeding 50 years.
Metal Shingles
Metal roofing shingles, usually made from aluminum, steel, copper, or zinc, represent a high-end roofing option. They are exceptionally durable, resistant to fire, wind, and hail, and boast a very long lifespan. The initial cost is substantial, typically ranging from $10.00 to $30.00 or more per square foot, installed. However, the superior longevity and low maintenance requirements often make them a cost-effective choice in the long run, particularly in areas prone to severe weather. The price variation depends heavily on the metal type and the complexity of the roof design.
Shingle Comparison Table
The following table provides a general comparison of the average costs and lifespan of different shingle types. Remember that actual costs can vary significantly based on location, labor costs, and specific product choices.
Shingle Type | Lifespan (Years) | Average Cost per Square (Installed) |
---|---|---|
Asphalt (3-tab) | 15-20 | $75-$150 |
Asphalt (Architectural) | 25-30 | $150-$400 |
Wood | 30-50+ (with maintenance) | $400-$1000+ |
Clay Tile | 50-100+ | $800-$2500+ |
Concrete Tile | 50-75 | $600-$1500+ |
Metal | 50-75+ | $1000-$3000+ |
Factors Influencing Shingle Costs
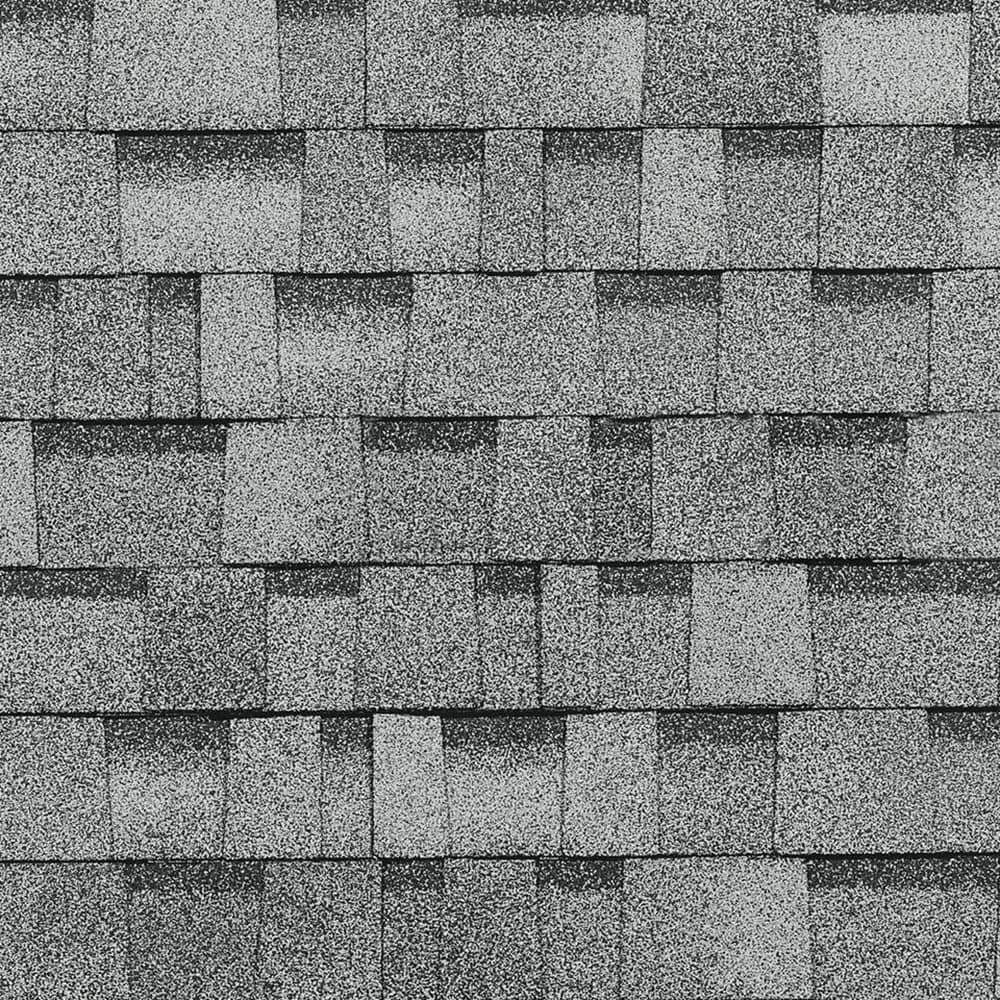
Several key factors interact to determine the final cost of roofing shingles and their installation. Understanding these factors can help homeowners make informed decisions and budget effectively for their roofing projects. This section will explore the significant influences on the overall price.
Shingle Quality and Pricing, Best price for roofing shingles
The quality of roofing shingles directly impacts the overall cost. Higher-quality shingles, typically made with more durable materials and advanced manufacturing processes, command higher prices. For example, architectural shingles, known for their dimensional appearance and enhanced weather resistance, are generally more expensive than standard three-tab shingles. The longevity of the shingles is a key factor; a longer lifespan, though initially more expensive, can translate to lower long-term costs due to reduced replacement needs. Features such as impact resistance, wind resistance, and algae resistance also influence price, as these enhanced features add to the manufacturing complexity and cost. Premium shingles often include warranties that reflect their superior quality and extended lifespan.
Labor Costs and Their Impact
Labor costs constitute a significant portion of the total roofing project expense. The complexity of the roof, its size, and the accessibility of the work area all influence labor time and therefore the overall cost. Steeper roofs, roofs with intricate designs, or those requiring specialized equipment or safety measures will inherently command higher labor costs. Furthermore, the prevailing wage rates in a specific geographic location, the contractor’s experience and reputation, and the demand for roofing services at a given time all affect the labor component of the final price. For instance, a contractor with a proven track record and high demand might charge a premium compared to a less experienced contractor.
Geographic Location and Material Costs
Geographic location significantly influences roofing shingle costs. Transportation costs for materials vary depending on distance from manufacturing plants and distribution centers. Areas with high transportation costs tend to have higher shingle prices. Additionally, local building codes and regulations can influence material choices and installation methods, indirectly impacting costs. For example, areas prone to hurricanes might require stronger, more expensive shingles to meet stricter building codes. The availability of skilled labor also varies geographically, influencing labor costs as previously discussed.
Material Availability and Installation Complexity
The availability of specific shingle types can impact pricing. High demand for a particular shingle style or color, coupled with limited supply, can lead to price increases. Similarly, the complexity of the roof installation can affect costs. A roof with multiple valleys, dormers, or chimneys requires more time and specialized skills, leading to increased labor costs. Unexpected issues encountered during installation, such as discovering underlying roof damage, can also significantly increase the final cost. These unforeseen complications can add considerable time and materials to the project, impacting the overall budget.
Finding the Best Deals on Roofing Shingles
Securing the best price for your roofing shingles requires a strategic approach that combines thorough research, smart shopping, and effective negotiation. This section will guide you through the process of finding the most competitive prices while ensuring you’re working with reputable suppliers.
Comparing prices from various suppliers is crucial for obtaining the best deal. Different vendors, including home improvement stores and roofing contractors, often offer varying prices for the same shingle type and quantity. This variation can stem from factors such as bulk purchasing discounts, ongoing sales, and regional pricing differences. By comparing multiple quotes, you can identify significant savings opportunities.
Reputable Supplier Identification and Scam Avoidance
Identifying trustworthy suppliers is paramount to avoid potential scams and ensure the quality of your roofing materials. Several key indicators can help you distinguish reputable businesses from unreliable ones. Look for established businesses with a proven track record, verifiable licenses and insurance, and positive customer reviews. Be wary of suppliers offering prices significantly lower than competitors without a clear explanation. Request references and check the Better Business Bureau (BBB) for any complaints or negative feedback. A detailed contract outlining the scope of work, payment terms, and warranty information should always be a requirement before commencing any project. Avoid making significant upfront payments without a clear understanding of the deliverables.
Negotiating Prices with Suppliers
Negotiating prices is a common practice in the roofing industry. Don’t be afraid to ask for discounts, especially when purchasing in bulk or during off-peak seasons. Having multiple quotes from different suppliers strengthens your negotiating position, allowing you to leverage competitive offers. Highlight your budget constraints while expressing your interest in their products or services. Consider bundling services, such as shingle installation with the material purchase, to potentially negotiate a lower overall price. Always get everything in writing to avoid future misunderstandings.
Resources for Finding Discounted Roofing Materials
Several resources can assist in finding discounted roofing materials. Home improvement stores frequently offer seasonal sales and promotional discounts on building materials. Online marketplaces and auction sites may also offer deals on surplus or discontinued shingles, but exercise caution and verify the supplier’s reputation before purchasing. Local roofing supply yards can offer competitive pricing, particularly for larger projects. Joining homeowner associations or online forums can provide insights into local deals and recommendations from other homeowners. Consider purchasing materials during the off-season (typically fall and winter) when demand is lower, potentially leading to better pricing.
Understanding Roofing Shingle Warranties
Choosing roofing shingles involves a significant investment, and understanding the warranty is crucial for protecting that investment. A comprehensive warranty offers peace of mind, knowing you’re covered against potential defects and premature shingle failure. Ignoring the warranty details can lead to unexpected and costly repairs down the line.
Shingle warranties vary significantly in their terms and conditions, affecting both the short-term and long-term costs associated with your roof. A thorough understanding of these differences allows homeowners to make informed decisions based on their budget and long-term goals.
Warranty Types and Coverage
Roofing shingle warranties typically include two main components: a manufacturer’s warranty and a workmanship warranty. The manufacturer’s warranty covers defects in the shingles themselves, such as manufacturing flaws or material defects that lead to premature failure. This warranty is usually provided by the shingle manufacturer and covers the materials, regardless of who installed them. The workmanship warranty, on the other hand, is provided by the roofing contractor and covers the quality of the installation. This protects against issues arising from improper installation techniques, such as inadequate nailing or incorrect flashing.
The length and coverage of these warranties vary widely depending on the shingle type and manufacturer. Some manufacturers offer limited warranties, covering only a few years, while others offer extended warranties that can last for decades. For example, a basic warranty might cover only material defects for a period of 10 years, while a premium warranty might offer coverage for up to 50 years, including labor costs for replacement. The specific terms of each warranty, including what is and is not covered, should be carefully reviewed before making a purchase.
Impact of Warranties on Long-Term Cost
The initial cost of shingles with a longer, more comprehensive warranty may be higher than those with shorter warranties. However, this higher upfront cost can be offset by the reduced risk of expensive repairs or premature replacement. For instance, a homeowner opting for a 50-year warranty might avoid the significant cost of a full roof replacement within 10-20 years, which could easily cost tens of thousands of dollars.
Conversely, choosing a shingle with a limited warranty might result in significant savings initially, but it also increases the risk of incurring substantial repair or replacement costs earlier than anticipated. Consider the potential long-term savings against the initial higher cost when comparing warranties. A cost-benefit analysis, considering the potential for premature failure and repair costs, is essential. This should include factoring in the expected lifespan of the roof and the associated costs over that time period. For example, a homeowner in a region prone to severe weather might find a longer warranty particularly beneficial to mitigate the risks of storm damage.
DIY vs. Professional Installation
Choosing between DIY and professional roofing shingle installation involves weighing cost, risk, and skill level. While DIY can seem appealing for budget-conscious homeowners, professional installation offers expertise and warranty protection. This section will compare the costs and risks associated with each approach, providing a clear picture to help you make an informed decision.
The primary difference between DIY and professional installation lies in the overall cost. While DIY initially appears cheaper due to the absence of labor fees, unforeseen complications and mistakes can quickly escalate expenses. Professional installers, on the other hand, possess the experience and tools to complete the job efficiently and correctly, minimizing the risk of costly errors and future repairs.
Cost Breakdown: DIY vs. Professional Installation
A comprehensive cost comparison requires considering several factors. For a DIY project, you’ll need to account for the cost of materials, tools, permits (if required), and the value of your time. Professional installation costs typically include labor, materials (sometimes), and disposal fees. A rough estimate for a 2000 square foot roof might see DIY material costs ranging from $5,000 to $10,000, while professional installation could range from $10,000 to $25,000 depending on location, materials selected, and the complexity of the roof. This wide range underscores the importance of obtaining multiple quotes from reputable contractors.
Potential Risks and Benefits of DIY Installation
DIY installation offers the potential for significant cost savings if the project is completed successfully. However, it carries considerable risks. Improper installation can lead to leaks, premature shingle failure, structural damage, and even voiding manufacturer warranties. Lack of experience can result in longer project timelines, increased material waste, and potential injuries. Conversely, professional installation guarantees adherence to building codes, proper techniques, and often comes with a warranty covering workmanship.
Tools and Materials Needed for DIY Installation
Undertaking a DIY roofing project demands a significant investment in tools and materials. Essential tools include a roofing nail gun (preferably pneumatic), a measuring tape, a chalk line, a utility knife, safety glasses, work gloves, a ladder (or scaffolding for larger roofs), and various hand tools like hammers and pry bars. Materials needed include the shingles themselves, underlayment, roofing felt, flashing, nails, and possibly sealant. The exact quantity of each will depend on the roof’s size and complexity. It’s crucial to purchase high-quality materials to ensure longevity and prevent future issues. Failing to have the correct tools and materials can significantly impact the project’s timeline and cost-effectiveness.
Long-Term Costs of Roofing Shingles
The initial cost of roofing shingles is only one part of the overall expense. Understanding the long-term costs, encompassing maintenance, repairs, and eventual replacement, is crucial for making an informed decision. Different shingle types have varying lifespans and maintenance needs, significantly impacting the total cost of ownership over the years. Failing to account for these factors can lead to unexpected and substantial expenses down the line.
The total cost of ownership for roofing shingles encompasses the initial purchase price, installation fees, regular maintenance, potential repairs, and ultimately, the cost of replacement. This total cost varies considerably depending on the type of shingle chosen, the size and complexity of the roof, and the local climate. Accurately calculating this total cost allows homeowners to make a financially sound decision that aligns with their budget and long-term financial goals.
Shingle Lifespan and Associated Repair Costs
Different shingle types boast different lifespans. Asphalt shingles, for example, typically last 15-30 years, while more expensive options like tile or slate can last 50 years or more. This lifespan directly impacts repair costs. A shorter-lived shingle will require more frequent repairs and, ultimately, replacement sooner than a longer-lasting one. For instance, asphalt shingles might require minor repairs like replacing a few damaged shingles due to wind or hail every few years, whereas a well-maintained tile roof may need minimal intervention over its extended lifespan. These repair costs, while seemingly small individually, accumulate over time, significantly affecting the overall cost. For a 2000 square foot roof, minor repairs on asphalt shingles might cost $500-$1000 every 5 years, whereas a tile roof might only need such repairs once every 15-20 years, at a potentially higher cost per incident due to specialized labor.
Maintenance Requirements and Costs
Regular maintenance plays a crucial role in extending the lifespan of any roofing material and minimizing repair costs. This includes tasks like cleaning debris from gutters and valleys, inspecting the roof for damage after storms, and addressing minor issues promptly. While some homeowners might handle basic maintenance themselves, more extensive inspections or repairs often necessitate hiring a professional roofer. The cost of professional maintenance varies depending on location, the extent of the work, and the roofing material. For example, annual cleaning and inspection for an asphalt shingle roof might cost between $100-$300, whereas a more complex tile roof might require more specialized and expensive maintenance. Neglecting regular maintenance can lead to premature deterioration and significantly increase the cost of repairs or even necessitate a complete roof replacement earlier than anticipated.
Calculating Total Cost of Ownership
Calculating the total cost of ownership requires a comprehensive approach. It involves summing the initial purchase price, installation costs, projected maintenance expenses over the shingle’s lifespan, anticipated repair costs, and finally, the cost of replacement. A simple formula to estimate this is:
Total Cost of Ownership = Initial Cost + Installation Cost + (Annual Maintenance Cost x Lifespan) + (Repair Cost per Incident x Number of Incidents) + Replacement Cost
For example, let’s consider two scenarios: a 2000 square foot roof using asphalt shingles versus clay tiles. Asphalt shingles might cost $5000 for materials and $3000 for installation, with annual maintenance of $200 and an expected lifespan of 20 years. Assuming two major repair incidents at $1000 each and a replacement cost of $8000 after 20 years, the total cost would be approximately $22,400. Clay tiles, on the other hand, might cost $20,000 for materials and $5000 for installation, with less frequent maintenance and repair needs over a 50-year lifespan, and a replacement cost of $25,000. Despite the higher initial cost, the overall cost over 50 years could be lower due to the extended lifespan and reduced maintenance/repair expenses. This example highlights the importance of considering long-term factors beyond the initial investment.
Environmental Impact of Roofing Shingles
Choosing roofing shingles involves more than just aesthetics and cost; it also carries significant environmental implications. The manufacturing process, lifespan, and eventual disposal of shingles all contribute to their overall environmental footprint. Understanding these impacts allows for informed decisions that minimize the negative effects on our planet.
The environmental impact of roofing shingles varies greatly depending on the material used. Factors such as energy consumption during manufacturing, the use of recycled content, the durability and lifespan of the shingle, and the ease of recycling or disposal at the end of its life all play crucial roles. Asphalt shingles, for instance, are widely used due to their affordability, but their production is energy-intensive and they are not easily recyclable. Conversely, more sustainable options, such as metal or certain types of composite shingles, may have a lower overall environmental impact.
Asphalt Shingle Environmental Impact
Asphalt shingles, the most common roofing material, are primarily composed of asphalt, fiberglass, and mineral granules. The manufacturing process requires significant energy, contributing to greenhouse gas emissions. The extraction and processing of raw materials, such as petroleum for asphalt, also have environmental consequences. Furthermore, asphalt shingles are not readily recyclable and often end up in landfills, adding to waste volume. While some manufacturers are incorporating recycled materials into their asphalt shingles, the overall sustainability of this material remains a concern. For example, a study by the University of California, Berkeley, found that the embodied carbon of asphalt shingles is significantly higher than that of other roofing materials.
Metal Roofing Environmental Impact
Metal roofing, typically made from steel or aluminum, offers a more environmentally friendly alternative. While the initial energy consumption in manufacturing is relatively high, metal roofs have a significantly longer lifespan than asphalt shingles, reducing the frequency of replacements and the associated environmental impact. Moreover, metal roofing is highly recyclable, minimizing landfill waste. The use of recycled content in metal roofing production also contributes to its overall sustainability. For instance, a significant portion of the steel used in many metal roofs is recycled steel, reducing the demand for newly mined iron ore.
Sustainable Shingle Options and Their Sustainability
Several other shingle options offer increased sustainability compared to traditional asphalt shingles. These include:
- Composite Shingles: Often made from recycled materials, composite shingles offer a blend of durability and environmental friendliness. The use of recycled plastic or wood fibers in their composition reduces reliance on virgin materials. However, the manufacturing processes and the longevity of these shingles should still be considered in their overall environmental impact assessment.
- Clay and Concrete Tiles: These are durable and long-lasting, but their manufacturing requires significant energy and resources. However, their longevity often offsets the initial environmental cost.
- Wood Shingles: Sourced from sustainably managed forests, wood shingles can be a relatively eco-friendly option. However, their susceptibility to damage and shorter lifespan compared to other materials can lead to more frequent replacements.
It’s important to note that the sustainability of any shingle material depends on various factors, including the manufacturing process, transportation distances, and end-of-life management. A life cycle assessment (LCA) is often used to comprehensively evaluate the environmental impact of a product, considering all stages from raw material extraction to disposal. By considering these factors and choosing sustainable materials and installation practices, homeowners can minimize the environmental impact of their roofing choices.
Impact of Roof Size and Complexity on Pricing
The total cost of roofing shingles is significantly influenced by both the size and complexity of the roof. Larger roofs naturally require more materials and labor, leading to higher overall expenses. Similarly, complex roof designs with multiple angles, valleys, and dormers increase the time and skill required for installation, further impacting the final price.
Roof size is calculated by the square footage of the roof’s surface area. This measurement directly impacts the amount of shingles needed, a major component of the overall cost. More complex roofs, however, require more than just additional materials. The intricate design necessitates specialized techniques and often more experienced installers, resulting in a higher labor cost.
Roof Size’s Influence on Material Costs
The relationship between roof size and material cost is straightforward: a larger roof requires more shingles. For example, a 1,500 square foot roof will require approximately 15 squares of shingles (a square is 100 square feet), while a 3,000 square foot roof will need double that amount. This direct proportionality leads to a substantial increase in material expenses as the roof area expands. The cost per square of shingles will remain relatively constant, but the total cost will increase linearly with the square footage.
Roof Complexity’s Influence on Labor Costs
Complex roof designs significantly increase labor costs. Features like multiple valleys (where two roof slopes meet), hips (where two sloping roof planes meet at an external angle), ridges (the horizontal line at the highest point of a roof), and dormers (a vertical window projection from a sloping roof) all add to the installer’s workload. These features require more precise cuts, additional safety measures, and often more specialized skills, leading to a higher hourly rate or increased overall labor time. For instance, a simple gable roof will be significantly cheaper to install than a complex mansard roof with multiple dormers and valleys.
Hypothetical Scenario: Simple vs. Complex Roof
Consider two hypothetical roofs:
* Roof A (Simple): A 1,500 square foot gable roof with a simple design. The installation might take a crew of two experienced roofers approximately two days.
* Roof B (Complex): A 1,500 square foot roof with multiple valleys, hips, dormers, and a complex pitch. This installation might require a larger crew of three to four roofers and take at least four days to complete, potentially longer depending on weather conditions and access difficulties.
Even though both roofs have the same square footage, the complexity of Roof B results in significantly higher labor costs. The increased labor time, the need for specialized skills, and potential material waste due to intricate cuts all contribute to a substantially higher final price for Roof B compared to Roof A, despite having the same surface area. The difference in total cost could easily range from 20% to 50% or even more, depending on the specific complexity of the design and the location.
Seasonal Pricing Variations for Roofing Shingles: Best Price For Roofing Shingles
The cost of roofing shingles, like many building materials, fluctuates throughout the year due to changes in demand and supply. Understanding these seasonal variations can help homeowners save money by purchasing at the most opportune time. Several factors contribute to these price swings, impacting the overall cost of your roofing project.
Seasonal demand significantly affects shingle prices. The roofing industry experiences peak activity during warmer months (spring and summer) when weather conditions are favorable for installation. This increased demand leads to higher prices as suppliers and contractors respond to the surge in orders. Conversely, during the colder months (autumn and winter), demand typically decreases, resulting in potentially lower prices. This is because fewer homeowners undertake roofing projects during inclement weather, and contractors may offer discounts to secure work during the slower season.
Demand and Supply Dynamics
The interplay of supply and demand directly impacts shingle pricing. During peak seasons, the high demand often outstrips the supply, leading to price increases. Conversely, during the off-season, lower demand may lead to price reductions as suppliers try to move inventory. This dynamic is further influenced by factors like material availability, transportation costs, and the overall economic climate. For example, a particularly harsh winter might delay spring projects, leading to a temporary spike in prices as contractors catch up on backlogged work. Conversely, a mild winter could lead to earlier-than-usual spring projects, potentially easing the price increases usually associated with the peak season.
Optimal Purchasing Times
Generally, the best time to purchase roofing shingles is during the off-season, typically in the late autumn or early winter. During these months, contractors often have more scheduling flexibility and may be willing to negotiate prices to secure jobs. Furthermore, suppliers may offer discounts to reduce their inventory before the new year. However, it is crucial to weigh the potential savings against the extended timeline for installation. If the homeowner requires immediate roofing work, the slightly higher prices of the peak season might be a necessary compromise. Homeowners should always compare prices from multiple suppliers and contractors regardless of the season to ensure they are getting the best possible deal.
Financing Options for Roofing Projects
Securing funding for a new roof can significantly impact the overall project timeline and your budget. Several financing options are available, each with its own advantages and disadvantages. Carefully considering these options will help you choose the best fit for your financial situation and roofing needs.
Best price for roofing shingles – The cost of a new roof can be substantial, making financing a necessary consideration for many homeowners. Understanding the various financing avenues available allows for informed decision-making, ensuring a manageable payment plan while avoiding unnecessary financial strain.
Home Improvement Loans
Home improvement loans are specifically designed to fund projects like roof replacements. These loans typically offer fixed interest rates and repayment terms ranging from several months to several years. The interest rate will depend on your credit score and the loan amount. For example, a homeowner with excellent credit might secure a loan with a 5% interest rate over 5 years, while someone with a lower credit score might face a higher rate of 8% over the same period. The monthly payments are predictable, making budgeting easier. However, the total cost of the loan, including interest, will be higher than the initial loan amount.
Credit Cards
Using a credit card offers immediate access to funds, but carries a high interest rate if not paid off quickly. While convenient, this option is generally less desirable for larger projects like roof replacements due to the potential accumulation of substantial interest charges. For instance, if a $10,000 roof replacement is put on a credit card with a 18% APR and only minimum payments are made, it could take years to pay off and result in thousands of dollars in added interest. This option is best suited for smaller, unexpected repairs rather than a full roof replacement.
Personal Loans
Personal loans, similar to home improvement loans, offer fixed interest rates and repayment terms. However, they are not specifically earmarked for home improvements and may come with higher interest rates than loans specifically designed for home renovations. A personal loan could be a viable option if you can’t qualify for a home improvement loan or if you prefer a more flexible repayment schedule. It’s crucial to compare interest rates and fees from multiple lenders before choosing this option.
Payment Plans from Contractors
Some roofing contractors offer in-house financing options, often involving a down payment and monthly installments. These plans may be more flexible than traditional loans, but the interest rates and terms can vary significantly between contractors. It is essential to carefully review the contract and understand all the associated fees and charges before agreeing to a payment plan. This option can be attractive for its convenience, but always compare it to other financing options to ensure you are receiving the best possible terms.
HELOCs (Home Equity Lines of Credit)
A HELOC uses the equity in your home as collateral. It offers flexibility, allowing you to borrow and repay funds as needed. However, it carries risks, including the possibility of losing your home if you cannot repay the loan. A HELOC can be a good option if you have substantial equity in your home and need funds for other home improvement projects besides the roof. The interest rate is typically variable, meaning your monthly payments can fluctuate.
Illustrative Examples of Shingle Costs for Different Roof Sizes
Understanding the cost of roofing shingles involves more than just the price per shingle. Factors like roof size, complexity, labor costs, and material quality significantly impact the final expense. The following examples illustrate the potential cost variations for different roof sizes, offering a clearer picture of what homeowners might expect. Note that these are estimates, and actual costs may vary depending on location, contractor, and specific project details.
To accurately estimate costs, consider consulting with multiple roofing contractors in your area for personalized quotes. Remember to compare not only price but also the quality of materials, warranties offered, and the contractor’s reputation.
Small Roof Shingle Cost Example (1000 square feet)
This example represents a smaller home or a single-story structure with a relatively simple roof design. The lower square footage translates to reduced material and labor costs.
- Roof Size: 1000 square feet
- Shingle Type: 3-tab asphalt shingles (budget-friendly option)
- Material Cost: $2,000 – $3,000 (This includes the shingles, underlayment, and basic flashing.)
- Labor Cost: $3,000 – $5,000 (This includes tear-off, disposal, installation, and cleanup.)
- Total Estimated Cost: $5,000 – $8,000
Medium Roof Shingle Cost Example (2000 square feet)
This example represents a typical suburban home with a moderately complex roof design, potentially including multiple slopes or valleys.
- Roof Size: 2000 square feet
- Shingle Type: Architectural asphalt shingles (offers improved durability and aesthetics)
- Material Cost: $4,000 – $6,000 (Higher-quality shingles and increased material quantity drive up costs.)
- Labor Cost: $6,000 – $10,000 (Increased labor hours due to larger roof area and potential complexity.)
- Total Estimated Cost: $10,000 – $16,000
Large Roof Shingle Cost Example (3500 square feet)
This example represents a larger home, possibly a two-story house with a complex roof design, including multiple dormers, valleys, and ridges. The increased size and complexity significantly impact both material and labor costs.
- Roof Size: 3500 square feet
- Shingle Type: High-end architectural or composite shingles (offers superior durability, longevity, and aesthetics)
- Material Cost: $7,000 – $10,500 (High-quality materials and increased quantity significantly increase costs.)
- Labor Cost: $10,500 – $17,500 (Extensive labor hours due to the large size and complexity of the roof.)
- Total Estimated Cost: $17,500 – $28,000
FAQs
What is the average lifespan of asphalt shingles?
The average lifespan of asphalt shingles is 15-30 years, depending on quality and climate.
Can I install roofing shingles myself?
While DIY installation is possible, it’s generally recommended to hire professionals for safety and warranty reasons. DIY can void warranties.
What are the common warranty types for roofing shingles?
Common warranty types include manufacturer warranties covering defects and workmanship warranties provided by installers.
How often should I inspect my roof?
Regular roof inspections, at least twice a year (spring and fall), are recommended to identify potential problems early.
What are the environmental considerations when choosing roofing shingles?
Consider recycled content, energy efficiency, and the shingle’s end-of-life disposal options when choosing environmentally friendly shingles.