Initial Assessment & Planning
Installing a metal roof over existing asphalt shingles requires careful planning and preparation to ensure a successful and safe project. A thorough initial assessment is crucial to identify potential challenges and develop a comprehensive plan. This will minimize unforeseen complications and maximize efficiency during the installation process.
Preliminary Site Inspection
Before commencing any work, a comprehensive site inspection is necessary. This involves a visual assessment of the roof’s condition, including the existing asphalt shingles, the underlying decking, and the overall structure. Inspect for any signs of damage, such as rot, warping, or pest infestation. Check the condition of the flashing around chimneys, vents, and skylights. Note the pitch of the roof and the presence of any obstacles, such as trees or power lines, that might affect the installation process. Measuring the roof’s dimensions accurately is vital for material estimation. Finally, documenting the findings with photographs is highly recommended.
Project Plan: Materials, Tools, and Safety Precautions
A detailed plan outlining the required materials, tools, and safety precautions is essential for a smooth and safe installation. Accurate material calculations, based on the roof’s dimensions and the chosen metal roofing system, are paramount. This includes the metal roofing panels, underlayment, flashing, fasteners, and sealant. Tools required range from basic hand tools like hammers and screwdrivers to specialized tools such as a roofing nail gun and a metal shear. Safety equipment, including hard hats, safety harnesses, and fall protection systems, is non-negotiable. A detailed safety plan should also address potential hazards like working at heights and handling sharp materials. For example, a checklist system for each step of the installation can minimize the risk of accidents. A plan for waste disposal and environmental considerations should also be included.
Asphalt Shingle Removal and Disposal
Safe and environmentally responsible removal of the existing asphalt shingles is a crucial step. Begin by carefully removing any fragile or damaged shingles to prevent accidental falls. Work from the top down, removing shingles in manageable sections. Use caution to avoid damaging the underlying decking. Dispose of the removed shingles responsibly. Many municipalities offer curbside pickup for construction debris, or you can consider using a licensed waste disposal company. Recycling options may also be available, depending on your location. Remember to properly protect the surrounding landscaping during the removal process to minimize environmental impact. Consider using tarps or other protective coverings to contain debris. Following local regulations and guidelines for waste disposal is crucial to ensure environmental compliance. For instance, some areas require the separation of asphalt shingles from other types of construction waste.
Underlayment & Preparation
Installing a new metal roof over existing asphalt shingles requires careful preparation, and the use of appropriate underlayment is crucial for a long-lasting and leak-proof roof. Underlayment acts as a secondary water barrier, protecting your roof deck from water intrusion in case the metal roofing system is compromised. Proper installation ensures the longevity and effectiveness of your new roof.
The selection and installation of underlayment are critical steps in this process. Different types of underlayment offer varying levels of protection and performance characteristics, impacting both the installation process and the final roof’s durability. Careful consideration of the existing roof condition and climate is essential in choosing the right underlayment.
Underlayment Types and Selection
Several types of underlayment are suitable for installing a metal roof over asphalt shingles. The choice depends on factors such as budget, climate, and the condition of the existing roof. Common options include felt paper, synthetic underlayments, and rubberized asphalt underlayments. Felt paper, a traditional and relatively inexpensive option, provides basic water protection. Synthetic underlayments, often made from polypropylene or other durable materials, offer superior tear resistance, UV protection, and better water shedding capabilities compared to felt paper. Rubberized asphalt underlayments combine the waterproofing properties of asphalt with added strength and durability. For metal roofs installed over asphalt shingles, a synthetic underlayment is generally recommended due to its superior performance and longevity. It offers better protection against punctures and tears that can occur during the metal roof installation process.
Underlayment Installation Process
Before beginning underlayment installation, ensure the existing asphalt shingles are in good condition and securely fastened. Any loose or damaged shingles should be repaired or replaced. Start by rolling out the underlayment, beginning at the lowest point of the roof. Overlap each sheet according to the manufacturer’s instructions; typically, a minimum of 4 inches of overlap is recommended. Secure the underlayment using roofing staples or nails at regular intervals, ensuring complete adhesion to the roof deck. Maintain consistent spacing and penetration depth to avoid damaging the underlayment. Pay particular attention to valleys and other critical areas, ensuring complete coverage and secure fastening. Proper installation of underlayment involves working in a systematic manner, starting from the bottom and working your way up, ensuring adequate overlap and secure fastening at every stage.
Addressing Roof Deck Irregularities
Before installing the underlayment, a thorough inspection of the existing roof deck is necessary. Any significant irregularities, such as protruding nails, damaged plywood, or excessive warping, should be addressed before proceeding. Protruding nails or fasteners should be removed or driven down flush with the surface. Damaged sections of plywood should be replaced with new material, ensuring a smooth and even surface for the underlayment. For minor warping or unevenness, the use of appropriate shims can help create a more level surface. Addressing these issues before installing the underlayment prevents potential problems with the metal roofing system’s long-term performance and prevents unevenness that can lead to issues with the metal roofing’s watertight seal. A smooth and even roof deck ensures a consistent and secure installation of the underlayment and, ultimately, the metal roofing system.
Metal Roof Installation Techniques
Installing a metal roof over existing asphalt shingles requires careful consideration of several factors, including the type of metal roofing panels chosen and the appropriate fastening methods. The selection process significantly impacts the longevity, aesthetic appeal, and overall cost-effectiveness of the project. Proper installation techniques are crucial to ensure a weathertight and durable roof system.
Metal Roofing Panel Types and Their Suitability
Several metal roofing panel types are suitable for installation over asphalt shingles. The most common include standing seam and corrugated panels. Each offers unique advantages and disadvantages that should be carefully weighed before making a decision. The choice often depends on factors such as budget, aesthetic preferences, and the specific characteristics of the building.
Panel Type | Advantages | Disadvantages | Installation Complexity |
---|---|---|---|
Standing Seam | Long lifespan, excellent weather resistance, aesthetically pleasing, low maintenance, good for steep slopes | Higher initial cost, requires specialized tools and expertise for installation | Moderate to High |
Corrugated | Cost-effective, readily available, relatively easy to install, durable | Less aesthetically pleasing than standing seam, prone to dents and scratches, may require more frequent maintenance | Low to Moderate |
Fastening Methods for Metal Roofing Panels
Secure and weathertight fastening is paramount for any metal roof installation. The specific method employed depends heavily on the chosen panel type. Improper fastening can lead to leaks, premature failure, and significant repair costs.
For standing seam panels, concealed fastening systems are commonly used. These systems utilize clips and hidden fasteners, creating a clean, seamless appearance and preventing water penetration. The panels interlock, creating a strong, weather-resistant seal. Proper alignment and consistent spacing of the clips are crucial for optimal performance.
Corrugated panels, on the other hand, typically require exposed fasteners. These are driven directly through the panel and into the roof deck. The choice of fastener is critical, and stainless steel screws with a weatherproof sealant washer are commonly used to ensure a watertight seal and resist corrosion. Over-tightening should be avoided to prevent panel damage. Fasteners should be spaced according to manufacturer’s recommendations to ensure proper support and prevent panel buckling. Appropriate underlayment, such as a self-adhering membrane, is vital beneath the corrugated panels to further prevent leakage.
Flashing and Sealants
Proper flashing and sealant application are crucial for a long-lasting and leak-proof metal roof installed over existing asphalt shingles. Neglecting these details can lead to significant water damage and costly repairs. This section details critical areas requiring flashing, best practices for installation, and appropriate sealant types.
Critical Flashing Areas
Flashing is essential to prevent water penetration at points where the roof plane intersects other surfaces. These intersections represent vulnerabilities that require careful attention to detail during installation. Failure to properly flash these areas can lead to leaks and compromise the integrity of the entire roofing system.
- Chimneys: The area where the roof meets the chimney is a high-risk area for leaks. Flashing should extend several inches up the chimney and several inches onto the roof, creating a watertight seal. Properly installed step flashing, which overlaps each shingle course, is critical.
- Valleys: Valleys, where two roof slopes meet, are prone to water accumulation. A continuous valley flashing system, typically made of metal, should be installed beneath the roofing material to channel water away from the intersection.
- Vents: Roof vents, such as plumbing vents and exhaust vents, require flashing to seal the openings and prevent water intrusion. The flashing should fit snugly around the vent pipe and extend up and over the vent.
- Dormer Walls: The intersection of a dormer wall with the main roof requires careful flashing. Flashing should be installed to seal the gap between the dormer and the roof surface.
- Roof Penetrations: Any other penetrations in the roof, such as skylights or satellite dishes, must be properly flashed to prevent leaks. These should be carefully sealed with appropriate flashing materials that are compatible with both the metal roofing and the underlying asphalt shingles.
Best Practices for Flashing Installation, Installing metal roof over asphalt shingles
Successful flashing installation hinges on meticulous preparation and attention to detail. Improper installation can easily negate the protective benefits of flashing, leading to water damage.
- Proper Overlap: All flashing pieces should overlap sufficiently to ensure a watertight seal. The extent of overlap depends on the type of flashing and the specific application, but a minimum of 4 inches is generally recommended.
- Sealant Use: While flashing provides the primary barrier against water, sealant should be used to further secure the joints and seams. The sealant should be compatible with both the flashing material and the roofing materials.
- Surface Preparation: The surfaces to which the flashing is applied must be clean and dry. Any debris or loose materials should be removed before installation to ensure proper adhesion.
- Fastening: Flashing should be securely fastened to the roof using appropriate fasteners. The number and placement of fasteners will depend on the type of flashing and the specific application.
- Caulk Application: Use a high-quality, weather-resistant caulk to seal any gaps or seams in the flashing. This provides an extra layer of protection against water intrusion.
Sealant Selection and Application
The choice of sealant is critical to ensure a durable and watertight seal. Different sealants possess varying properties, making some more suitable for certain applications than others.
- Butyl Sealant: Butyl sealant is a popular choice for metal roofing due to its excellent adhesion, flexibility, and durability. It’s particularly effective in bridging gaps and accommodating movement in the roofing system. It should be applied in a continuous bead, ensuring complete coverage of the joint.
- Silicone Sealant: Silicone sealant offers good weather resistance and flexibility, but it may not adhere as well to all surfaces as butyl sealant. It’s often used for sealing smaller gaps and cracks. Ensure proper surface preparation before application.
- Polyurethane Sealant: Polyurethane sealants are known for their fast curing time and excellent adhesion. However, they can be less flexible than butyl or silicone, making them less suitable for areas with significant movement. Application requires precision to avoid excess buildup.
Ridge Cap and Trim Installation: Installing Metal Roof Over Asphalt Shingles
Installing ridge caps and trim pieces is the final, crucial step in ensuring a weathertight and aesthetically pleasing metal roof. Proper installation protects the underlying roof structure from water damage and enhances the overall appearance of your home. This section details the process for both ridge cap and trim installation, emphasizing techniques for proper alignment and weather sealing.
Installing metal roof over asphalt shingles – Ridge caps are long, interlocking pieces that cover the peak of the roof, providing a watertight seal at the highest point. Trim pieces, such as rake trim (along the gable ends) and eave trim (along the roof overhangs), protect the edges of the roof from the elements and give a finished look. Correct installation of both ridge caps and trim requires precision and attention to detail.
Ridge Cap Installation
Installing ridge caps begins with ensuring the underlying metal roofing panels are properly fastened and aligned. Ridge caps are typically designed to interlock, creating a strong and weather-resistant seam. Start at one end of the ridge and carefully align the first ridge cap piece, ensuring it overlaps the underlying panels sufficiently. Secure the cap using appropriate fasteners, typically self-tapping screws, spaced according to manufacturer’s instructions. Subsequent ridge cap pieces are then interlocked and fastened in the same manner, working your way across the entire ridge. Maintaining consistent overlap and proper fastener placement is essential for preventing leaks. Overlapping each piece by the recommended amount, usually an inch or two, is critical for water shedding. Finally, inspect the completed ridge for any gaps or misalignments. Any issues should be addressed immediately.
Trim Installation
Rake and eave trim pieces serve different but equally important functions. Rake trim protects the exposed edges of the roofing panels at the gable ends, preventing water from seeping into the roof structure. Eave trim protects the edges of the roof overhang, preventing water damage and adding a finished, clean look. Both are typically installed after the ridge caps are in place.
Rake Trim Installation
Rake trim is usually installed by first securing the trim to the fascia board using appropriate fasteners. Ensure the trim is flush with the fascia and aligned properly with the roofing panels. Overlapping the trim over the roofing panels slightly ensures a weathertight seal. Consistent spacing of fasteners is important to prevent warping or damage to the trim.
Eave Trim Installation
Eave trim is usually installed by securing it to the edge of the roof sheathing, overlapping the lower edge of the roofing panels. This provides a neat, finished look and protects the exposed edges of the roofing panels from the elements. Similar to rake trim, ensure consistent spacing of fasteners and a tight fit against the sheathing. Proper sealing at the junction between the trim and the roofing panels is vital to prevent leaks.
Visual Representation of Ridge Cap and Trim Installation
Imagine a triangular roof. At the peak, the ridge cap runs horizontally, interlocking pieces forming a continuous, sealed line. The ridge cap slightly overlaps the last row of roofing panels. On the sloped sides, the roofing panels are neatly aligned, and along the bottom edge (eaves), the eave trim is securely fastened, protecting the edge of the roofing panels. At the gable ends (vertical sides of the triangle), the rake trim is neatly fitted to the fascia board, covering the exposed edges of the roofing panels. The entire assembly – ridge cap, roofing panels, eave trim, and rake trim – creates a unified, weather-resistant system. The visual effect should be one of clean lines and complete coverage, minimizing exposed edges.
Safety Procedures Throughout the Installation
Metal roofing installation involves working at significant heights and handling heavy materials, demanding a rigorous commitment to safety. Failing to prioritize safety can lead to serious injuries or fatalities. This section details crucial safety measures to ensure a safe and successful project.
Safe practices must be integrated into every stage of the project, from initial planning to final cleanup. A thorough risk assessment before starting work is essential, identifying potential hazards and implementing control measures to mitigate them. This proactive approach significantly reduces the likelihood of accidents.
Working at Heights Safety Precautions
Working at heights presents significant risks. Falls are a leading cause of injury in roofing projects. Therefore, the use of appropriate fall protection equipment is mandatory. This includes the use of harnesses, anchor points securely attached to the structure, and safety lines to prevent falls. Furthermore, scaffolding or ladders should be inspected regularly for stability and damage before use, and workers should always maintain three points of contact when climbing or working on ladders. Proper training in the use of fall arrest systems is crucial for all personnel involved. Regular safety meetings should reinforce the importance of these procedures and address any concerns. For example, a robust safety plan might specify that a designated spotter be present whenever someone is working at a significant height, ensuring immediate assistance if needed.
Personal Protective Equipment (PPE) Requirements
Appropriate Personal Protective Equipment (PPE) is crucial for protecting workers from potential hazards during metal roof installation. The selection of PPE should be based on a thorough risk assessment, ensuring that the equipment is appropriate for the specific tasks and environmental conditions.
- Hard hats: To protect against falling objects.
- Safety glasses or goggles: To protect eyes from debris and UV radiation.
- Hearing protection: To mitigate noise pollution from power tools.
- Work gloves: To protect hands from cuts and abrasions.
- Fall arrest harness and system: To prevent falls from heights.
- Steel-toed boots: To protect feet from dropped objects and sharp materials.
- Cut-resistant clothing: To protect against sharp metal edges.
Handling and Storing Metal Roofing Materials
Metal roofing materials are heavy and can be sharp. Improper handling and storage can lead to injuries and damage to the materials. Careful planning and execution are essential to prevent accidents.
- Use appropriate lifting equipment: Heavy sheets should be lifted using mechanical aids like forklifts or hoists to avoid strain injuries. Manual lifting should only be undertaken when the weight is manageable and with proper lifting techniques.
- Store materials properly: Materials should be stored in a dry, level area, protected from the elements. They should be stacked neatly and securely to prevent them from falling or shifting. Sharp edges should be protected to prevent cuts.
- Transport carefully: When transporting materials, ensure they are secured to prevent shifting or falling during transit. Use appropriate vehicles and tie-down methods.
- Regular inspections: Regularly inspect materials for damage before and during installation. Damaged materials should be immediately removed from the worksite.
Addressing Potential Challenges
Installing a metal roof over existing asphalt shingles presents unique challenges. The success of the project hinges on careful pre-installation assessment and proactive problem-solving. Ignoring potential issues can lead to delays, increased costs, and compromised roof longevity. This section Artikels common problems and their solutions.
Uneven Roof Surfaces and Damaged Shingles are common issues encountered when installing a metal roof over existing asphalt shingles. These irregularities can significantly impact the installation process and the final result, potentially leading to leaks or premature wear. Addressing these issues before beginning the metal roof installation is crucial for a successful and long-lasting outcome.
Uneven Roof Surfaces
Uneven roof surfaces, often caused by age, settling, or previous repairs, can create difficulties in achieving a proper and secure installation of the metal roofing panels. These inconsistencies can lead to panel buckling, gaps, and compromised weather sealing. To address uneven surfaces, a thorough assessment is needed to determine the extent of the problem. Minor irregularities might be addressed by using shims under the metal panels to create a level surface. For more significant unevenness, the underlying decking may require repair or replacement before the metal roof can be installed. This may involve replacing damaged or warped plywood sections with new, appropriately sized pieces, ensuring a smooth and level base for the metal roofing. In some cases, leveling compounds may be used to fill in smaller depressions and create a more uniform surface. However, it’s crucial to allow these compounds to fully cure before proceeding with the metal roof installation to ensure proper adhesion and prevent future problems.
Damaged Shingles
Damaged or deteriorated asphalt shingles present a significant obstacle to a successful metal roof installation. Loose, cracked, or missing shingles not only compromise the existing roof’s integrity but also create uneven surfaces that interfere with the proper installation of the metal roofing. Before installing the metal roof, all damaged shingles must be removed and replaced. This ensures a smooth, even surface for the new metal panels and prevents potential leaks or damage to the new roof. Furthermore, repairing any underlying decking damage caused by the deteriorated shingles is equally important to ensure a robust and durable foundation for the metal roof.
Dealing with Unexpected Issues
During the installation process, unforeseen issues may arise. These might include discovering hidden structural damage, encountering unexpected obstacles under the existing roofing, or experiencing weather-related delays. A proactive approach is crucial. Maintaining open communication with the homeowner is essential to discuss any unexpected findings and their implications on the project timeline and budget. Careful documentation of the issue, including photographic evidence, is crucial for resolving disputes or adjusting the project scope. Seeking professional advice from a structural engineer or roofing specialist might be necessary for complex problems. Flexibility and a problem-solving mindset are essential to successfully navigate these challenges and ensure the project’s successful completion.
Post-Installation Inspection & Maintenance
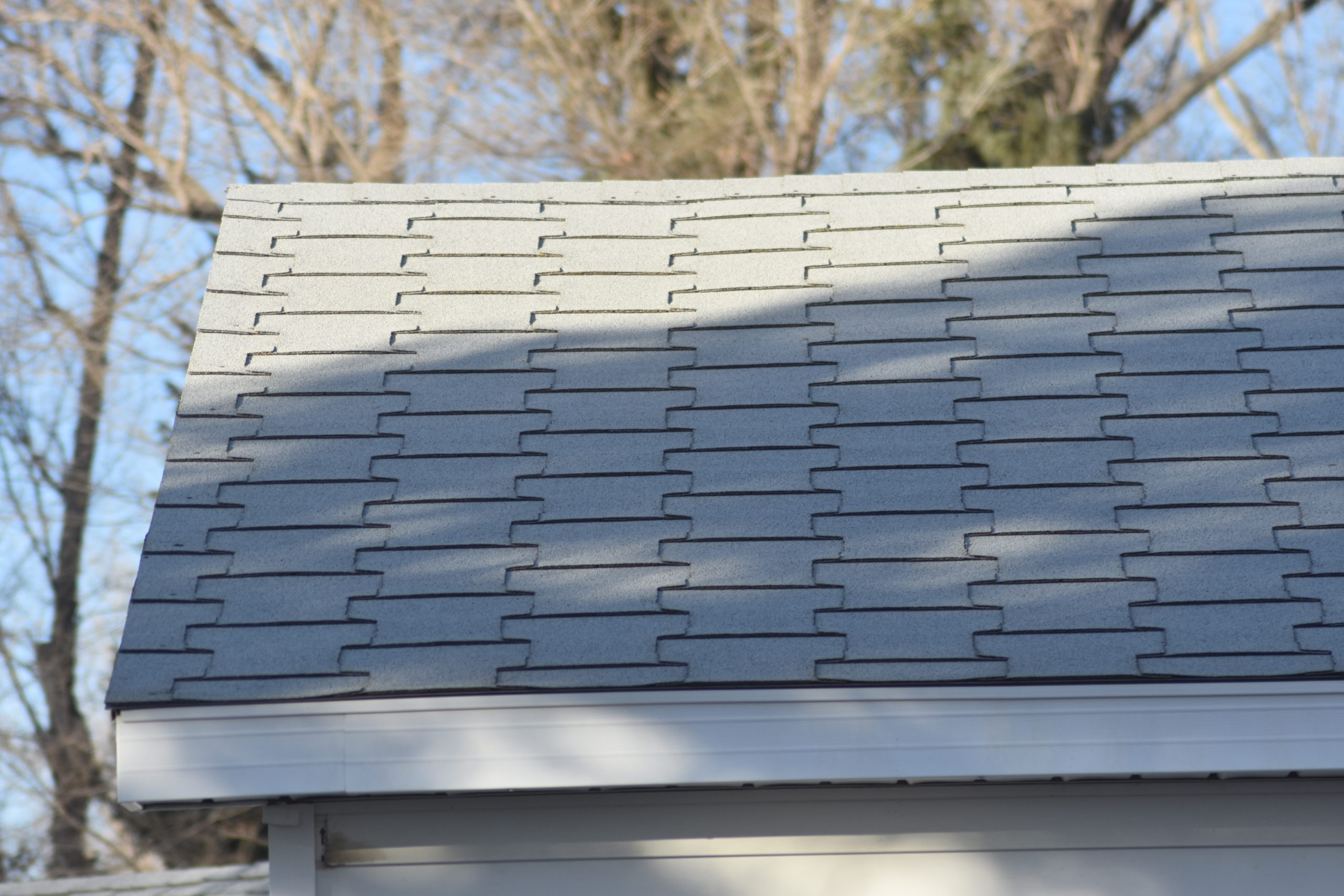
A thorough post-installation inspection is crucial to ensure the metal roof’s longevity and effectiveness. This process verifies the quality of workmanship and identifies any potential issues before they escalate into costly repairs. Regular maintenance will further extend the lifespan of your investment, protecting it from the elements and maintaining its aesthetic appeal.
A comprehensive post-installation inspection will pinpoint any defects or areas needing attention, allowing for prompt rectification and preventing future problems. This proactive approach significantly contributes to the long-term performance and value of your metal roof.
Post-Installation Inspection Checklist
This checklist provides a structured approach to thoroughly examining the newly installed metal roof. Each item should be carefully checked to ensure the roof meets the required standards of quality and safety.
- Overall Appearance: Inspect the roof for any noticeable damage, such as dents, scratches, or missing panels. Check for uniformity in panel alignment and overall aesthetic appeal.
- Flashing and Sealants: Verify the proper installation and sealing of all flashings around chimneys, vents, and other penetrations. Look for any gaps or signs of leakage.
- Ridge Cap and Trim: Examine the ridge cap and trim for proper alignment, secure fastening, and absence of gaps or damage. Ensure the end caps are correctly installed and sealed.
- Fasteners: Check the security of all fasteners. Loose or missing fasteners can compromise the roof’s integrity and lead to leaks.
- Gutters and Downspouts: Inspect gutters and downspouts for proper drainage and ensure they are securely attached and free from obstructions.
- Underlayment: If visible, check the underlayment for any damage or improper installation. This is particularly important in areas with flashings.
- Water Runoff: Observe water runoff during a rainfall to identify any areas where water is pooling or leaking. This can indicate issues with panel alignment or flashing.
Routine Maintenance Tasks
Regular maintenance is key to preserving the integrity and lifespan of your metal roof. These simple tasks, performed annually or biannually, will help prevent problems and ensure your roof remains in optimal condition.
- Debris Removal: Regularly clear leaves, branches, and other debris from the roof surface and gutters. Accumulated debris can cause water to pond and lead to damage.
- Visual Inspection: Conduct a visual inspection of the entire roof at least twice a year, looking for any signs of damage, such as dents, rust, or loose fasteners. Pay close attention to areas prone to damage, such as valleys and flashings.
- Fastener Check: Periodically check the tightness of all fasteners. Tighten any loose fasteners to prevent them from working loose and causing leaks.
- Gutter Cleaning: Clean gutters and downspouts at least twice a year to ensure proper water drainage. Clogged gutters can lead to water damage and ice dams in colder climates.
- Painting or Coating (if applicable): If your metal roof is painted or coated, consider repainting or recoating as needed to maintain its appearance and protect it from the elements. This is especially important in coastal areas or regions with harsh weather conditions.
Addressing Potential Post-Installation Problems
Prompt identification and resolution of problems after installation are critical. Ignoring minor issues can lead to significant and costly repairs down the line.
- Leaks: Leaks are often indicated by water stains on ceilings or walls. Locate the source of the leak by carefully inspecting the roof, paying close attention to flashings, seams, and fasteners. Repair leaks promptly using appropriate sealants or by replacing damaged components.
- Rust: Rust can develop on metal roofs over time, particularly in areas with high humidity or salt spray. Clean and treat rust spots immediately to prevent further corrosion. Consider applying a rust-inhibiting primer and paint to protect the affected area.
- Loose or Missing Fasteners: Loose or missing fasteners can compromise the roof’s structural integrity and lead to leaks. Tighten loose fasteners or replace missing ones promptly using the same type and size of fastener originally used.
- Panel Damage: Damaged panels can be repaired or replaced as needed. For minor dents, a gentle hammer and dolly can sometimes be used to reshape the panel. Severely damaged panels will require replacement.
Cost Considerations and Budgeting
Installing a metal roof over existing asphalt shingles is a significant investment, but one that can offer long-term benefits in terms of durability and energy efficiency. Understanding the associated costs is crucial for effective budgeting and project planning. This section provides a breakdown of typical expenses and offers strategies for cost-effective solutions.
The total cost of a metal roof installation over existing asphalt shingles varies widely depending on several factors, including the size of the roof, the type of metal chosen (e.g., steel, aluminum, copper), the complexity of the roof design (e.g., multiple valleys, dormers), labor costs in your region, and the need for additional work such as removing the old shingles. It’s essential to obtain multiple detailed quotes from reputable contractors before making a decision.
Typical Cost Breakdown for Metal Roof Installation Over Asphalt Shingles
The following table presents a sample cost breakdown. Remember that these figures are estimates and can vary considerably based on the factors mentioned above. Always obtain personalized quotes from contractors in your area.
Material | Quantity | Unit Cost | Total Cost |
---|---|---|---|
Metal Roofing Panels | 20 squares (approx. 2000 sq ft) | $200 – $400 per square | $4000 – $8000 |
Underlayment | 20 squares | $20 – $40 per square | $400 – $800 |
Flashing (various types) | As needed | Varies widely | $500 – $1500 |
Fasteners (screws, nails) | As needed | $50 – $150 | $50 – $150 |
Ridge Cap & Trim | As needed | Varies widely | $300 – $800 |
Labor | Per square or per day | $500 – $1000 per square | $10,000 – $20,000 |
Waste Removal | One-time fee | $200 – $500 | $200 – $500 |
Permits (if required) | One-time fee | $100 – $500 | $100 – $500 |
Total Estimated Cost | $15,550 – $35,850 |
Note: This table provides a range of costs. The actual cost will depend on the specific materials chosen, the size and complexity of the roof, and the contractor’s labor rates.
Finding Cost-Effective Solutions
While prioritizing quality materials and workmanship is essential, several strategies can help you find cost-effective solutions without compromising the longevity and performance of your metal roof.
Consider purchasing materials in bulk to negotiate better prices. Explore different metal roofing options; steel is generally more affordable than aluminum or copper. Opting for a simpler roof design can also reduce material and labor costs. Finally, thoroughly research and compare quotes from multiple reputable contractors to secure the best value for your investment. Remember to factor in the long-term cost savings associated with a durable metal roof, which can significantly outweigh the initial investment.
General Inquiries
Can I install a metal roof myself?
While possible, installing a metal roof is a complex project best left to experienced professionals unless you have significant roofing experience. Improper installation can lead to leaks and damage.
How long does a metal roof over asphalt shingles last?
A properly installed metal roof can last 50 years or more, significantly longer than asphalt shingles. The lifespan depends on the metal type and environmental factors.
What are the permit requirements for installing a metal roof?
Building permits are usually required for major roofing projects. Check with your local building department for specific regulations and requirements in your area.
What is the best time of year to install a metal roof?
Spring and fall are generally ideal times for roof installation, as temperatures are moderate and the risk of extreme weather is lower.