Cost Comparison
Choosing between metal and asphalt shingle roofing involves a significant financial commitment. While initial costs might favor asphalt shingles, a comprehensive cost analysis considering lifespan, maintenance, and potential repairs reveals a more nuanced picture. This section will compare the upfront and long-term costs associated with both roofing types, helping you make an informed decision.
Material and Installation Costs
The initial cost of a metal roof is generally higher than that of an asphalt shingle roof. Metal roofing materials, including panels, fasteners, and underlayment, typically range from $5 to $12 per square foot, depending on the metal type (steel, aluminum, copper) and finish. Installation adds another $5 to $15 per square foot, bringing the total installed cost to $10 to $27 per square foot. Asphalt shingle roofing, in contrast, ranges from $3 to $8 per square foot for materials, and installation costs typically add $2 to $5 per square foot, resulting in a total installed cost of $5 to $13 per square foot. These figures are estimates and can vary based on geographic location, labor costs, and the complexity of the roof. For example, a 2000 square foot roof could see a difference of $10,000 to $28,000 between metal and asphalt shingle installations.
Long-Term Cost Savings and Expenses
The longevity of a metal roof significantly impacts its long-term cost-effectiveness. Metal roofs can last 50 years or more with proper maintenance, whereas asphalt shingle roofs typically last 15-30 years. This extended lifespan translates to fewer replacements over the lifetime of a home, offsetting the higher initial investment. Asphalt shingles, however, require more frequent repairs and replacements, leading to recurring expenses over time. For instance, a homeowner might need to replace an asphalt shingle roof twice within a 50-year period, incurring significant costs each time. The cumulative cost of these replacements could easily surpass the initial investment in a metal roof.
Maintenance Costs Over 20 Years
Over a 20-year period, the maintenance costs for asphalt shingle roofs are considerably higher than for metal roofs. Asphalt shingles are susceptible to damage from wind, hail, and UV degradation, requiring periodic repairs or replacements of damaged shingles. These repairs can range from minor patching to larger-scale replacements, adding up to significant costs over two decades. Regular cleaning is also necessary to remove debris and prevent algae growth. Metal roofs, while requiring less frequent maintenance, may still need occasional cleaning and the occasional repair of minor dents or scratches. However, the overall maintenance costs for metal roofs are significantly lower, often requiring only minimal attention throughout the 20-year period. For a typical home, one might expect to spend several hundred dollars on asphalt shingle maintenance over 20 years, compared to perhaps a few hundred dollars for a metal roof. These figures are estimates and can vary greatly depending on weather conditions and the homeowner’s diligence in maintenance.
Installation Process
Installing a metal roof over existing asphalt shingles is a significant undertaking requiring careful planning and execution. This process involves several key steps, from safely removing the old roofing material to securely fastening the new metal roofing. Proper techniques ensure a long-lasting and leak-proof roof.
Asphalt Shingle Removal
Safe and efficient removal of the old asphalt shingles is crucial for a successful metal roof installation. Begin by thoroughly inspecting the existing roof structure for any damage or weaknesses. This is best accomplished from the ground and using binoculars to identify potential issues. Safety harnesses and fall protection equipment are essential for all workers involved in this phase. Shingles should be removed carefully, starting from the peak and working your way down. Dispose of the old shingles responsibly, according to local regulations. Consider using a roofing tear-off tool to help remove the shingles more efficiently and safely. After shingle removal, inspect the underlying sheathing for any damage and make necessary repairs before proceeding. Thoroughly clean the roof deck of any debris, nails, or loose particles before installing the underlayment.
Underlayment Installation
Once the old shingles are removed and the roof deck is prepared, a new underlayment should be installed. This provides an additional layer of protection against water damage. Common types of underlayment include synthetic felt and rubberized asphalt. The underlayment should be laid according to the manufacturer’s instructions, ensuring proper overlap and secure fastening. Staple guns are typically used to secure the underlayment, with staples placed approximately every 6 inches along the edges and every 12 inches in the field. Careful attention to detail is necessary to ensure a continuous and watertight barrier.
Metal Roofing Installation
The metal roofing panels are then installed over the underlayment. The installation method varies depending on the type of metal roofing (standing seam, corrugated, etc.). Generally, panels are installed starting at the bottom edge of the roof and working upwards, overlapping each panel according to the manufacturer’s specifications. Self-tapping screws are typically used to secure the panels to the underlayment. It’s crucial to use the correct type and length of screws for the specific metal roofing and underlayment materials. Proper spacing of the fasteners is essential to prevent leaks and to allow for thermal expansion and contraction of the metal. The final step involves sealing any exposed edges or seams with appropriate sealant to prevent water penetration.
Fastener Selection
Choosing the correct fasteners is paramount to the longevity and structural integrity of the new metal roof. The type and quantity of fasteners needed depend on several factors, including the type of metal roofing, the type of underlayment, and the local climate. The following table provides a general guideline:
Material | Fastener Type | Quantity (per square foot) |
Standing Seam Metal Roofing | Self-tapping screws with EPDM washers | 8-12 |
Corrugated Metal Roofing | Self-tapping screws | 10-15 |
Synthetic Underlayment | Staples | 6-8 per square foot |
Asphalt Underlayment | Staples or roofing nails | 4-6 per square foot |
Safety Precautions
Roofing work is inherently dangerous. It is imperative to prioritize safety throughout the entire installation process. This includes, but is not limited to, the use of fall protection equipment (harnesses, lifelines, and anchor points), proper footwear, safety glasses, and gloves. Workers should be properly trained and experienced in roofing installation techniques. Regular breaks should be taken to prevent fatigue, and the worksite should be kept clean and free of debris to minimize tripping hazards. All workers should be aware of and comply with all relevant safety regulations and guidelines.
Durability and Lifespan
Choosing between a metal roof and an asphalt shingle roof involves considering their respective lifespans and how well they withstand various weather conditions. Metal roofing generally boasts significantly greater longevity and resilience compared to asphalt shingles, although the specific lifespan can vary depending on several factors.
Metal roofs and asphalt shingle roofs exhibit different levels of durability and longevity when subjected to various environmental stresses. Understanding these differences is crucial for making an informed roofing decision, as the long-term cost-effectiveness of each option is directly tied to its lifespan and maintenance requirements.
Lifespan Comparison Under Varying Weather Conditions
The expected lifespan of a metal roof significantly surpasses that of an asphalt shingle roof. A properly installed metal roof can last 50 years or more, sometimes even exceeding 75 years, while asphalt shingles typically last 15-30 years, depending on the quality of the shingles and the climate. In harsh climates with extreme temperature fluctuations, heavy snowfall, or intense sun exposure, the difference in lifespan becomes even more pronounced. For example, an asphalt shingle roof in a region with frequent hailstorms might require replacement within 10-15 years, while a metal roof in the same location could easily last twice as long, minimizing the need for costly and disruptive replacements.
Resistance to Extreme Weather Events
Metal roofing demonstrates superior resistance to extreme weather events compared to asphalt shingles. Its strength and durability make it highly resistant to high winds, capable of withstanding hurricane-force gusts that would easily damage or destroy asphalt shingles. Similarly, metal roofs are far more resistant to hail damage. While hail can dent a metal roof, it is less likely to cause significant damage compared to asphalt shingles, which can be easily cracked or broken by hail impacts. Heavy snow loads are also better managed by metal roofs due to their higher strength and ability to shed snow more effectively. Asphalt shingles can become brittle and prone to cracking under heavy snow, especially when combined with ice.
Impact of UV Exposure on Longevity
Ultraviolet (UV) radiation from the sun is a significant factor affecting the longevity of both metal and asphalt shingle roofs. Asphalt shingles are particularly susceptible to UV degradation. Prolonged exposure to sunlight causes the asphalt to become brittle and the color to fade, reducing the shingles’ lifespan and increasing their vulnerability to damage from other weather events. Metal roofing, while not immune to UV degradation, is far more resistant. High-quality metal roofs often feature protective coatings that significantly mitigate the effects of UV radiation, ensuring the roof retains its structural integrity and aesthetic appeal for many years. The color of a metal roof might fade slightly over time, but the underlying material remains largely unaffected.
Aesthetic Considerations
Metal roofing offers a diverse range of aesthetic options, often surpassing the variety available with traditional asphalt shingles. The interplay of color, profile, and material can significantly impact a home’s curb appeal and overall architectural harmony. Understanding these options allows homeowners to make informed decisions that enhance their property’s visual attractiveness.
Metal Roofing Styles and Colors Compared to Asphalt Shingles
Asphalt shingles typically offer a limited palette of colors, mostly earth tones and muted shades. Metal roofing, however, boasts a far wider spectrum. Colors range from classic earth tones mimicking traditional roofing materials to vibrant and modern shades, including blues, greens, reds, and even metallic finishes. Furthermore, the profiles themselves contribute significantly to the aesthetic. Asphalt shingles are largely limited to three-tab or architectural styles, while metal roofing offers standing seam, corrugated, ribbed, and even shake-style profiles, each with a unique visual impact. The ability to customize metal roofing with various finishes, such as stone-coated options that mimic the texture of natural slate or wood shakes, further expands the aesthetic possibilities beyond what asphalt shingles can provide.
Metal Roofing and Architectural Styles
Metal roofing complements a surprising variety of architectural styles. A standing seam metal roof, for instance, can add a sleek, modern touch to a contemporary home, while a shake-style metal roof can enhance the rustic charm of a farmhouse or cabin. Corrugated metal roofing can provide an industrial-chic aesthetic to loft-style homes or urban dwellings. The color choice also plays a significant role; a dark gray or charcoal metal roof can add a dramatic element to a Victorian-style home, whereas a lighter color might better suit a Mediterranean or Spanish-style house. Careful consideration of the roof’s profile and color allows for a seamless integration of the metal roofing with the existing architectural design.
Visual Representation of Metal Roofing Profiles and Suitability
Imagine a series of images showcasing different homes and their metal roofing.
Image 1: A contemporary home with clean lines and large windows. The roof is topped with a sleek, standing seam metal roof in a dark charcoal gray. The clean lines of the standing seam profile perfectly complement the home’s modern architecture, creating a sophisticated and unified look.
Image 2: A charming farmhouse with a rustic facade. Its roof is covered in a shake-style metal roofing, painted a warm, earthy brown. The texture and color of the metal shakes mimic the look of natural wood shakes, enhancing the home’s rustic charm without compromising on durability.
Image 3: A craftsman-style bungalow with intricate detailing. The roof features a ribbed metal panel in a deep, rich green. The subtle texture of the ribbed profile adds visual interest without overpowering the home’s detailed architecture. The green complements the natural surroundings and enhances the home’s cozy aesthetic.
Image 4: A Mediterranean-style villa with stucco walls and arched doorways. The roof is covered with a tile-style metal roofing in a terracotta color. This mimics the look of traditional clay tiles, creating a harmonious blend with the home’s architectural style and warm climate aesthetic.
These examples demonstrate the versatility of metal roofing in enhancing the aesthetic appeal of various architectural styles. The careful selection of profile and color allows for a cohesive and visually pleasing design that complements the home’s existing features.
Environmental Impact
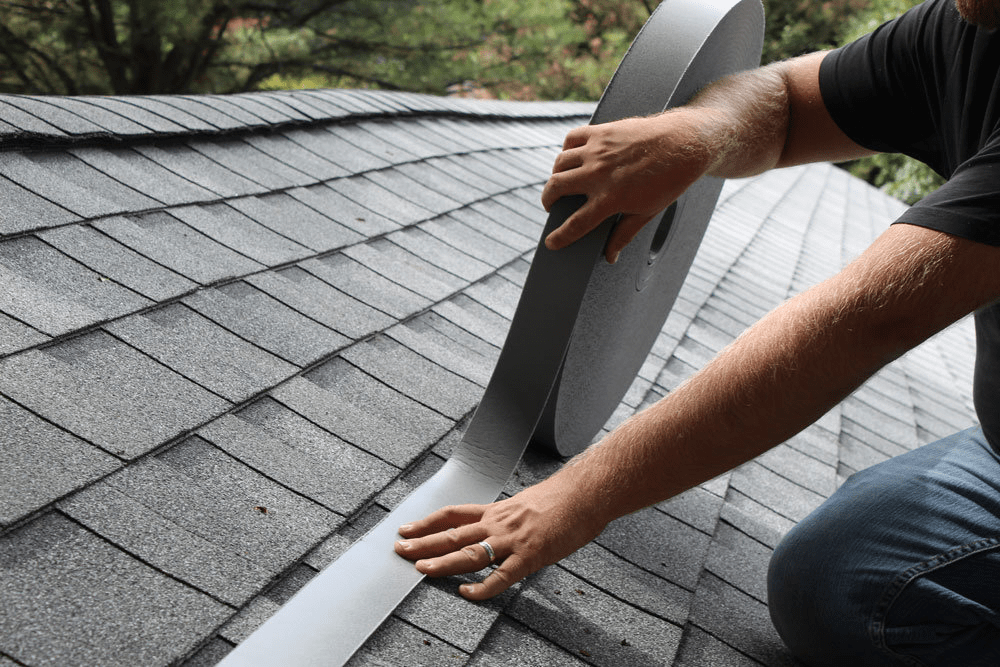
Choosing between metal and asphalt shingle roofing involves considering their respective environmental footprints throughout their entire lifecycle, from raw material extraction and manufacturing to transportation, installation, and ultimately, disposal or recycling. Both options present trade-offs, and the optimal choice depends on various factors, including regional resources and disposal infrastructure.
The environmental impact of metal and asphalt shingle roofing is multifaceted, encompassing several key stages. Manufacturing processes for both materials consume energy and resources, and transportation adds to carbon emissions. End-of-life management, including disposal or recycling, also significantly impacts the environment. A comprehensive assessment necessitates comparing these impacts across the lifecycle of each roofing material.
Manufacturing and Transportation
Metal roofing generally requires more energy to manufacture than asphalt shingles due to the energy-intensive processes involved in steel production. However, the energy intensity of asphalt shingle production is also significant, considering the extraction and processing of petroleum-based components and the manufacturing of fiberglass mats. Transportation impacts vary depending on the distance materials travel from manufacturing plants to installation sites. Metal roofing, due to its higher density, might have slightly higher transportation costs per unit area compared to asphalt shingles. However, the overall environmental impact is influenced by the transportation mode (truck, train, ship) and the distance covered. A local source of either roofing material would reduce the environmental impact of transportation.
Recyclability and End-of-Life Management
Metal roofing possesses a significant advantage in recyclability. Steel is readily recyclable, and many scrap metal recycling programs exist. This contributes to a lower environmental burden at the end of the roof’s lifespan. In contrast, asphalt shingles are less easily recyclable. While some recycling programs exist, they are less widespread, and a significant portion of asphalt shingles ends up in landfills, contributing to waste accumulation and potential environmental contamination from leaching of components. The percentage of asphalt shingles recycled remains considerably lower than that of steel roofing.
Potential Environmental Benefits and Drawbacks
Metal roofing offers several potential environmental benefits, primarily its recyclability and longer lifespan, reducing the frequency of replacement and associated waste generation. Its durability also means less frequent repair and maintenance, further minimizing environmental impact. However, the energy-intensive manufacturing process remains a drawback. Asphalt shingles are generally less expensive initially, making them accessible to a broader range of consumers. However, their shorter lifespan and lower recyclability contribute to a larger environmental footprint over the long term. Furthermore, the petroleum-based components of asphalt shingles contribute to reliance on fossil fuels and associated greenhouse gas emissions. The manufacturing process also involves the release of volatile organic compounds (VOCs). The choice between metal and asphalt shingles should involve careful consideration of these competing factors.
Energy Efficiency: Metal Roofing Over Asphalt Shingles
Metal roofing and asphalt shingles present distinct differences in their energy efficiency, significantly impacting a building’s heating and cooling costs. Understanding these differences is crucial for homeowners considering a roof replacement, as the long-term savings from improved energy efficiency can offset the higher initial investment of a metal roof.
Metal roofing generally offers superior energy efficiency compared to asphalt shingles. This advantage stems primarily from its reflective properties and its ability to maintain a more stable internal temperature.
Reflective Properties of Metal Roofing and Energy Consumption
Metal roofing materials, particularly those with lighter colors, possess high solar reflectance. This means they reflect a significant portion of the sun’s radiant energy back into the atmosphere, preventing it from being absorbed by the roof and transferred into the building’s interior. Asphalt shingles, on the other hand, absorb a much larger percentage of solar radiation, leading to increased heat gain in warmer months. The difference can be substantial. For example, a light-colored metal roof might reflect up to 80% of solar radiation, while a dark-colored asphalt shingle roof might reflect only 10-15%. This significantly reduces the amount of heat transferred into the building, lessening the burden on air conditioning systems and resulting in lower cooling costs. In colder months, the thermal mass of metal roofing helps to retain heat more effectively than asphalt shingles, reducing heating costs. This effect is less pronounced than the cooling benefits, but it still contributes to overall energy savings. Studies have shown that metal roofing can lead to energy savings of 10-25% annually, depending on factors like climate, roof color, and building insulation.
Impact of Roofing Type on Heating and Cooling Costs
The impact on heating and cooling costs is directly related to the reflective properties and thermal mass of each roofing material. A home with a metal roof will experience lower cooling bills during summer months due to the reduced heat transfer into the building. This translates to less strain on the air conditioning system, potentially leading to a longer lifespan for the unit and reduced maintenance costs. While the heating cost savings during winter may be less dramatic, the improved insulation properties of metal roofing, especially when coupled with proper attic insulation, still contribute to lower energy consumption and reduced heating bills compared to asphalt shingles. The magnitude of these savings will vary based on factors like geographic location, climate conditions, and the specific type of metal roofing and asphalt shingles used. However, in many cases, the long-term energy savings associated with metal roofing can outweigh the higher initial installation cost.
Comparison of Energy Efficiency Between Metal Roofing and Asphalt Shingles
Feature | Metal Roofing | Asphalt Shingles |
---|---|---|
Solar Reflectance | High (up to 80%, depending on color) | Low (10-15%, depending on color) |
Heat Absorption | Low | High |
Impact on Cooling Costs | Significantly reduces cooling costs | Increases cooling costs |
Impact on Heating Costs | Moderately reduces heating costs | Increases heating costs (less pronounced than cooling cost increase) |
Overall Energy Efficiency | Superior | Lower |
Maintenance Requirements
Regular maintenance is crucial for extending the lifespan and preserving the integrity of any roof, regardless of whether it’s made of asphalt shingles or metal. A proactive approach to maintenance can prevent costly repairs and ensure your roof continues to protect your home effectively for years to come. This section Artikels recommended maintenance schedules and common problems for both roofing types.
Regular Maintenance Schedules
A well-defined maintenance schedule helps identify and address potential issues before they escalate into significant problems. For both metal and asphalt shingle roofs, annual inspections are recommended, ideally during spring and fall. These inspections should focus on identifying loose or damaged components, checking for signs of leaks, and assessing the overall condition of the roofing material.
Asphalt Shingle Roof Maintenance
Regular maintenance for asphalt shingle roofs involves inspecting for missing, cracked, or curled shingles. Look for signs of granule loss, which indicates shingle degradation. Clean debris, such as leaves and branches, from the roof surface to prevent moisture buildup and damage. Moss or algae growth should be addressed promptly to prevent further deterioration. Regular cleaning can extend the lifespan of an asphalt shingle roof significantly. For example, a homeowner who diligently cleans their roof twice a year might add several years to its lifespan compared to someone who neglects maintenance.
Metal Roof Maintenance
Metal roofs, while durable, also require regular attention. Inspect the panels for signs of rust, dents, or loose fasteners. Check the sealant around flashing and chimneys for cracks or deterioration. Clean debris and remove any leaves or branches that accumulate on the roof surface. Regular cleaning is particularly important in areas prone to heavy snowfall or high winds, as these conditions can dislodge debris and damage the roof. For instance, a coastal homeowner might need to clean their metal roof more frequently due to salt spray and wind-blown debris.
Common Problems and Solutions
Both asphalt shingle and metal roofs are susceptible to specific problems. Understanding these issues and their solutions is vital for effective roof maintenance.
Asphalt Shingle Roof Problems and Solutions
Common problems with asphalt shingle roofs include shingle damage from wind, hail, or aging, and leaks around chimneys or valleys. Damaged shingles should be replaced immediately. Leaks can be addressed by resealing flashing or replacing damaged underlayment. Proper ventilation is also critical to prevent moisture buildup and premature shingle deterioration. Poor ventilation can lead to significant problems like mold growth and structural damage.
Metal Roof Problems and Solutions
Metal roofs are known for their durability but can still experience issues such as rust, dents, and loose fasteners. Rust can be addressed through spot repairs or repainting. Dents can often be repaired without replacing entire panels. Loose fasteners should be tightened to prevent leaks. Proper installation is crucial for preventing many common metal roof problems. A poorly installed metal roof is more prone to leaks and damage from extreme weather conditions.
Identifying and Addressing Potential Leaks
Identifying and addressing leaks promptly is crucial for preventing extensive damage to your home’s interior.
Leak Identification and Repair in Asphalt Shingle Roofs
Leaks in asphalt shingle roofs are often indicated by water stains on ceilings or walls, damp spots in the attic, or missing or damaged shingles. Inspecting the attic after a rainfall can help pinpoint the leak’s location. Minor leaks can sometimes be repaired by replacing damaged shingles or sealing cracks. However, significant leaks may require professional assistance. For example, a leak originating from a damaged chimney flashing would necessitate professional repair.
Leak Identification and Repair in Metal Roofs, Metal roofing over asphalt shingles
Leaks in metal roofs can be more challenging to identify, as water may travel along the panels before entering the house. Inspecting seams, fasteners, and flashing is crucial. Leaks are often indicated by water stains or rust. Repairing leaks in metal roofs often involves resealing seams, replacing damaged panels, or tightening loose fasteners. In some cases, professional assistance may be necessary, particularly for complex leaks or those requiring specialized tools. For example, a leak in a standing seam metal roof might require specialized tools and expertise to address effectively.
Weight and Structural Considerations
Metal roofing offers significant advantages, but its weight is a crucial factor to consider before installation, especially when replacing asphalt shingles. Understanding the weight difference and its implications on your existing roof structure is essential for a safe and successful project. Failing to account for this can lead to structural damage and costly repairs.
Metal roofing is considerably heavier than asphalt shingles. While the exact weight varies depending on the metal type (steel, aluminum, copper), gauge, and profile, a metal roof can weigh anywhere from 50 to 150 pounds per square (100 square feet), compared to approximately 200-300 pounds for a standard asphalt shingle roof over the entire roof. However, the *additional* weight of the metal roof over the existing asphalt shingles is the critical factor. This added weight necessitates a careful evaluation of your roof’s structural capacity.
Roof Structural Assessment
Assessing the structural integrity of a roof before installing a metal roof over asphalt shingles involves a thorough inspection by a qualified professional. This inspection should include a visual examination for signs of rot, decay, or damage to the existing rafters, trusses, and sheathing. A structural engineer may be needed to conduct load calculations to determine if the roof can safely support the additional weight. This calculation considers factors like the existing roof’s age, the type of framing members, and the current snow load capacity in your region. Signs of weakness, such as sagging rafters or cracked sheathing, should prompt further investigation and likely necessitate reinforcement.
Necessary Structural Reinforcements
If the assessment reveals that the existing roof structure cannot support the added weight of a metal roof, various reinforcements may be necessary. These might include:
- Adding additional rafters or trusses to increase the load-bearing capacity of the roof system. This is particularly important for older homes or those with weaker framing members.
- Replacing damaged or deteriorated roof sheathing with new, stronger material. Plywood or OSB sheathing is commonly used, and the thickness may need to be increased depending on the load calculations.
- Installing additional bracing or support members to strengthen the existing framing. This could involve adding collar ties, knee braces, or other structural components to improve stability.
- Strengthening existing supports. This might involve using metal straps or other reinforcement methods to secure weak points in the structure.
The specific reinforcements needed will depend on the results of the structural assessment and the weight of the chosen metal roofing system. It is crucial to work with experienced professionals to ensure that the reinforcement work is properly executed and meets all building codes and safety standards. Failing to adequately reinforce the roof structure before installing a metal roof can result in structural failure, potentially causing significant damage and posing a safety hazard. A poorly reinforced roof can lead to sagging, leaks, and even collapse. Therefore, the expense of proper structural assessment and reinforcement is a worthwhile investment in the long-term safety and integrity of your home.
Insurance Implications
Choosing between metal and asphalt roofing can significantly impact your homeowner’s insurance premiums. While both are common roofing materials, insurers assess their risk profiles differently, leading to variations in coverage and cost. Understanding these differences is crucial for making an informed decision.
Insurance premiums are influenced by a variety of factors, including the roofing material’s durability, fire resistance, and the overall risk of damage from weather events. Metal roofing, due to its superior longevity and fire resistance, often results in lower premiums compared to asphalt shingles. Conversely, the higher initial cost of metal roofing might not be immediately reflected in a lower premium, but the long-term savings on repairs and replacements can indirectly benefit you.
Impact of Roofing Material on Insurance Premiums
Metal roofing’s inherent strength and resistance to fire, high winds, and hail often lead to lower insurance premiums. Insurance companies recognize the reduced risk associated with this type of roofing and may offer discounts or lower rates. Conversely, asphalt shingles, being more susceptible to damage from these factors, might result in higher premiums, particularly in areas prone to severe weather. The premium difference can vary widely depending on the specific insurer, location, and the details of the policy. For example, a homeowner in a hurricane-prone region might see a more substantial premium reduction by switching to metal roofing than a homeowner in a region with milder weather.
Potential Benefits and Drawbacks of Insurance Coverage
A significant benefit of metal roofing is the potential for reduced premiums and potentially lower deductibles. This is a direct financial advantage that can offset the higher initial investment in the roofing material. The longer lifespan of metal roofing also contributes to lower long-term insurance costs, as fewer claims are likely to be filed due to roof damage. However, a potential drawback is the higher upfront cost of installation, which might not be immediately reflected in insurance savings. Furthermore, while metal roofing offers superior protection against many types of damage, it’s still crucial to have comprehensive coverage for events such as extreme wind damage that could cause structural issues.
Relevant Insurance Policy Clauses
Insurance policies often contain clauses specifying coverage limitations based on roofing material. For instance, a policy might include a clause detailing the extent of coverage for damage caused by hail, differentiating between the repair costs for asphalt shingles and the potentially less extensive repairs needed for a metal roof. Another relevant clause could relate to fire damage; metal roofing’s superior fire resistance could lead to more favorable terms or a higher payout in case of a fire. It’s crucial to review your specific policy and discuss any concerns with your insurance provider to ensure complete understanding of the coverage related to your chosen roofing material. Some insurers may offer specific endorsements or riders for premium adjustments based on the type of roofing.
Sound Insulation
Metal roofing and asphalt shingle roofing offer different levels of sound insulation, a crucial factor for homeowners concerned about noise reduction. The inherent properties of each material, along with the installation methods, significantly impact their ability to dampen external sounds. Understanding these differences is essential for making an informed roofing choice.
Metal roofing, while often perceived as noisy, can provide surprisingly good sound insulation when installed correctly. The sound dampening capabilities are influenced by the type of metal, its thickness, and the presence of insulation layers beneath the roofing system. Conversely, asphalt shingles, being a more porous material, generally offer better inherent sound absorption than metal, though this can vary depending on the shingle type and underlayment. However, neither material completely eliminates external noise.
Comparison of Sound Insulation Properties
Metal roofing panels, especially those with a thicker gauge, can effectively reduce the transmission of high-frequency sounds like rain and hail. However, their solid nature can amplify lower-frequency sounds such as wind and distant traffic. Asphalt shingles, with their more porous and layered structure, tend to absorb sound more effectively across a broader frequency range, leading to a generally quieter interior experience. The effectiveness of both materials is also heavily dependent on the quality of underlayment and insulation used during installation. A well-insulated roof, regardless of the material, will significantly improve sound dampening.
Strategies for Improving Sound Insulation
Several strategies can enhance the sound insulation properties of both metal and asphalt shingle roofs. For metal roofs, the addition of a layer of rigid insulation between the roof decking and the metal panels is highly effective in reducing noise transmission. This insulation acts as a sound barrier, preventing sound waves from traveling directly into the living space. The use of a sound-dampening underlayment beneath the metal panels also contributes significantly to noise reduction. For asphalt shingle roofs, a thicker layer of underlayment, such as a rubberized membrane, can improve sound absorption. The density and type of the underlayment directly influence its sound-dampening capacity. Adding extra insulation within the attic space also contributes to better overall soundproofing.
Impact of Rain, Hail, and Wind Noise
Rain noise is significantly affected by the roofing material. Metal roofs, due to their reflective nature, can amplify the sound of raindrops, particularly during heavy downpours. Asphalt shingles, being more porous and absorbent, tend to muffle the sound of rain more effectively. Hail, on the other hand, can impact both types of roofs, producing noticeable noise. While the impact on asphalt shingles might be somewhat absorbed, the harder surface of a metal roof can lead to a louder and more resonant sound. Wind noise is another concern. While the solid nature of metal roofing can create a drumming or whistling sound, asphalt shingles, being more flexible, generally handle wind noise better, although very high winds can still generate noticeable noise with both materials. Proper installation, including sealing all gaps and seams, is crucial for minimizing wind noise with both roofing types.
Warranty and Guarantees
Choosing between metal roofing and asphalt shingles involves careful consideration of the warranties offered by manufacturers. Understanding the terms and conditions of these warranties is crucial for protecting your investment and ensuring you receive the expected lifespan and performance from your new roof. Significant differences exist between the types and lengths of warranties offered for each material.
Manufacturers typically offer different warranty types for metal roofing and asphalt shingles, impacting the overall cost-benefit analysis. These warranties can cover defects in materials and workmanship, ensuring the consumer’s protection against premature failure. However, several factors can affect the validity of these warranties, and it’s essential to understand them before making a purchase decision.
Warranty Types and Coverage
Metal roofing warranties generally cover longer periods than asphalt shingle warranties. Metal roofs often come with a 30- to 50-year warranty, sometimes even longer, covering issues like rust, holes, and paint fading. Asphalt shingle warranties, on the other hand, typically range from 20 to 30 years, primarily focusing on the shingle’s structural integrity against granule loss and wind damage. However, these warranties often have limitations and exclusions, such as damage caused by extreme weather events or improper installation. Some manufacturers offer warranties that cover both materials and labor, while others only cover materials.
Factors Affecting Warranty Validity
Several factors can invalidate or limit the coverage provided by a roofing warranty. Proper installation is paramount; a poorly installed roof, regardless of the material, may void the warranty. Regular maintenance, including cleaning debris and addressing minor issues promptly, is also often a condition of the warranty. Furthermore, damage caused by extreme weather events (hurricanes, hailstorms), acts of God, or neglect may not be covered. Warranties usually specify the conditions under which they remain valid, including compliance with manufacturer’s installation guidelines and maintenance schedules. Understanding these conditions is vital to ensure warranty protection.
Example Warranty Clauses
A typical metal roofing warranty might include clauses specifying the manufacturer’s responsibility for replacing defective panels due to rust or manufacturing flaws within a specified timeframe, typically 30-50 years. However, it may exclude damage caused by improper installation, impacts from falling objects, or damage resulting from extraordinary weather events beyond a specific wind speed. Conversely, an asphalt shingle warranty might stipulate a 20-30 year guarantee against granule loss, but explicitly state that damage caused by wind exceeding a specified velocity will not be covered. Some warranties might contain clauses limiting liability to the cost of replacement materials, excluding labor costs. It is vital to carefully review all clauses, including limitations and exclusions, before signing any warranty agreement. Understanding these clauses will allow for informed decision-making when choosing a roofing material.
Essential FAQs
Metal roofing over asphalt shingles – Can I install metal roofing over damaged asphalt shingles?
No. Damaged shingles must be repaired or replaced before installing a metal roof. Underlying damage can compromise the integrity of the new roof.
How does the weight of a metal roof affect my home’s structure?
Metal roofing is heavier than asphalt shingles. A structural engineer should assess your roof’s ability to support the added weight before installation.
What are the common maintenance needs for a metal roof over asphalt shingles?
Regular inspections for leaks, debris removal from gutters, and occasional cleaning are typically sufficient. The underlying asphalt shingles will require less maintenance than a standalone asphalt roof.
Does installing a metal roof over asphalt shingles void my home insurance?
It shouldn’t, but it’s crucial to inform your insurance provider about the modification. They may require an inspection to ensure proper installation.