Average Costs
The cost of a new asphalt shingle roof varies significantly depending on several factors. Understanding these factors and their impact on the overall price is crucial for budgeting and planning your roofing project. This section provides an overview of average costs, influencing factors, and a cost breakdown to help you better understand the investment involved.
New asphalt roof cost – Asphalt shingle roofing remains a popular choice due to its affordability and relatively long lifespan. However, regional differences in labor rates, material availability, and even the complexity of the roof itself contribute to considerable price variations across the United States. The following table offers a glimpse into these variations.
Average Asphalt Roof Costs by Region and Factors
The following table presents estimated average costs for a new asphalt shingle roof. These figures are approximate and should be considered a starting point for your own research and budgeting. Remember to obtain multiple quotes from reputable contractors in your area for a more accurate estimate.
Region | House Size (sq ft) | Roof Complexity | Average Cost (USD) |
---|---|---|---|
Northeast (e.g., New England) | 1500 | Average | $12,000 – $18,000 |
Southeast (e.g., Florida, Georgia) | 1500 | Average | $10,000 – $15,000 |
Midwest (e.g., Illinois, Ohio) | 1500 | Average | $11,000 – $17,000 |
Southwest (e.g., Arizona, California) | 1500 | Average | $13,000 – $19,000 |
Northwest (e.g., Oregon, Washington) | 1500 | Average | $14,000 – $20,000 |
Northeast (e.g., New England) | 2500 | High (complex design, multiple slopes) | $20,000 – $30,000+ |
Southeast (e.g., Florida, Georgia) | 2500 | High (complex design, multiple slopes) | $17,000 – $25,000+ |
Factors Influencing Asphalt Roof Installation Prices
Several factors contribute to the variability in asphalt roof installation prices. Understanding these factors will help you to better interpret quotes and make informed decisions.
These factors include, but are not limited to: House size (larger roofs require more materials and labor), roof complexity (multiple slopes, dormers, valleys increase labor costs), material quality (higher-end shingles offer longer warranties and better performance but come at a higher price), labor costs (regional variations and contractor demand significantly impact labor expenses), permits and inspections (costs vary by location and the extent of required inspections), removal of existing roofing (if necessary, this adds to the overall cost), and waste disposal fees (proper disposal of old roofing materials is important and contributes to the overall expense).
Typical Cost Components
The total cost of a new asphalt roof is typically broken down into several key components. A clear understanding of these components ensures transparency and helps in accurate budgeting.
These components typically include: Materials (shingles, underlayment, flashing, nails, etc.), Labor (the cost of the roofing crew’s time and expertise), Permits (fees required for obtaining necessary building permits), Tear-off (cost of removing the old roofing system, if needed), Waste removal (disposal of old roofing materials), and Other expenses (such as cleanup, potential repairs to underlying decking).
Material Costs
The cost of materials represents a significant portion of your total asphalt roofing project expense. Understanding the price variations between different shingle types and the impact of shingle quality on longevity is crucial for making informed decisions and budgeting effectively. This section details the factors influencing material costs and provides a comparison of common asphalt shingle options.
Asphalt shingle prices vary considerably depending on the type of shingle and its quality. Higher-quality shingles generally offer superior durability, weather resistance, and aesthetic appeal, but come with a higher upfront cost. However, this increased initial investment often translates to a longer lifespan and reduced long-term maintenance expenses.
Asphalt Shingle Types and Price Differences
Three-tab shingles are the most economical option, typically offering a lifespan of 15-20 years. Architectural shingles, also known as dimensional shingles, are thicker and more complex in design, providing a more upscale appearance and a longer lifespan (20-30 years or more) due to their increased durability and weather resistance. The added layers and dimensional design contribute to their higher cost. Other specialty shingles, such as those with enhanced features like impact resistance or algae resistance, will command even higher prices reflecting their advanced properties.
Shingle Quality and Lifespan’s Influence on Project Cost
The quality of asphalt shingles directly impacts the overall cost of the roofing project. While lower-quality shingles may seem cheaper initially, their shorter lifespan means more frequent replacements, increasing the total cost over the building’s lifetime. Higher-quality shingles, despite their higher upfront cost, often prove more economical in the long run due to their extended durability and reduced need for repairs or premature replacements. For instance, a home requiring a roof replacement every 15 years will incur significantly higher costs compared to a home with a high-quality roof lasting 30 years. This long-term perspective is crucial for cost-effective decision-making.
Asphalt Shingle Price Comparison
The following table illustrates the approximate price per square foot for different asphalt shingle types. These prices are estimates and can vary based on location, supplier, and current market conditions. Remember that a “square” in roofing terms refers to 100 square feet.
Shingle Type | Price per Square Foot (USD) |
---|---|
3-Tab Shingles (Standard) | $0.50 – $1.50 |
Architectural Shingles (Mid-Range) | $1.50 – $3.00 |
Architectural Shingles (Premium) | $3.00 – $5.00+ |
Specialty Shingles (Impact Resistant, Algae Resistant) | $4.00 – $7.00+ |
Labor Costs
Labor costs represent a significant portion of the overall expense for a new asphalt roof installation. Understanding the factors that influence these costs is crucial for accurate budgeting and informed decision-making. These factors vary considerably, impacting the final price you’ll pay.
Labor costs are determined by several key variables. Geographic location plays a significant role, as labor rates in densely populated urban areas tend to be higher than in rural regions due to increased demand and higher cost of living. The experience and reputation of the roofing contractor also significantly affect labor costs. Highly experienced and reputable contractors often command higher hourly rates due to their expertise, efficiency, and proven track record. Finally, the complexity of the project itself directly impacts labor time and, consequently, cost. A complex roof design, requiring specialized techniques or extensive repairs, will naturally necessitate more labor hours compared to a simpler, straightforward installation.
Factors Influencing Labor Costs
Several interconnected factors influence the final labor costs associated with an asphalt roof installation. These factors work in concert to determine the total labor expense. Understanding these factors enables homeowners to better anticipate and manage project costs.
Geographic Location: Wage rates for skilled labor vary widely across different regions. Major metropolitan areas generally have higher labor costs than smaller towns or rural areas. This is primarily due to differences in the cost of living, demand for skilled workers, and competition among contractors. For example, a roofing crew in New York City might charge significantly more per hour than a comparable crew in a smaller city in the Midwest.
Contractor Experience: The experience level of the roofing contractor directly impacts labor costs. Experienced contractors, possessing extensive knowledge and skills, often command higher hourly rates due to their efficiency and reduced risk of errors. Inexperienced contractors may offer lower rates, but the potential for delays, mistakes, and rework could ultimately increase the total project cost. A seasoned professional, for instance, might complete a roof installation more quickly and accurately, minimizing potential material waste and labor overruns.
Project Complexity: The complexity of the roofing project is a critical factor determining labor hours and costs. A simple, single-layer roof installation on a standard-sized house will naturally require less labor than a complex multi-layer roof on a large or unusually shaped building. Additional factors like the need for extensive repairs, removal of existing roofing materials, or intricate design features all contribute to increased labor time and cost. For instance, a roof requiring significant repairs to underlying sheathing or significant amounts of tear-off will increase the total labor hours.
Sample Roofing Contract: Labor Costs and Payment Schedule
A well-defined contract outlining labor costs and payment schedules is crucial for both the homeowner and the contractor. This contract should clearly specify all aspects of the project, ensuring transparency and preventing misunderstandings. Below is a sample outlining key elements:
Contract for Asphalt Roof Installation
Between: [Homeowner Name and Address] and [Contractor Name and Address]
Project: Asphalt roof installation at [Address]
Labor Costs: $[Total Labor Cost] (This amount includes [Number] hours of labor at $[Hourly Rate] per hour. Additional hours will be billed at $[Hourly Rate] per hour. This total includes tear-off, installation of underlayment, and installation of the asphalt shingles.)
Payment Schedule:
- 25% upon signing of contract.
- 25% upon completion of tear-off and underlayment installation.
- 25% upon completion of shingle installation.
- 25% upon final inspection and project completion.
Other terms and conditions: [Include details about permits, warranties, dispute resolution, etc.]
Signatures:
Hourly Rates: Experienced vs. Inexperienced Contractors
Hourly rates for roofing contractors vary significantly based on experience. Experienced contractors typically charge higher hourly rates reflecting their expertise, efficiency, and lower risk of errors. Inexperienced contractors may offer lower rates, but this can be offset by potential delays, mistakes, and the need for rework.
Experienced Contractor: Experienced contractors often charge between $[Lower Bound] and $[Upper Bound] per hour, reflecting their skill, efficiency, and established reputation. Their higher hourly rate is often justified by the speed and quality of their work, leading to overall cost savings.
Inexperienced Contractor: Inexperienced contractors might charge between $[Lower Bound] and $[Upper Bound] per hour. While the initial cost may seem lower, the risk of mistakes, delays, and the need for corrections could significantly increase the overall project cost.
Permitting and Inspections
Obtaining the necessary permits and passing inspections are crucial steps in any roofing project, including asphalt roof installations. These processes ensure the work meets local building codes and safety standards, protecting both the homeowner and the contractor. Understanding the associated costs and potential complications is essential for accurate budgeting and project planning.
Permitting and inspections involve a series of steps, each with its own associated fees. These fees vary significantly depending on the location, the size of the project, and the complexity of the work involved. In addition to the direct costs, there can be indirect costs associated with delays caused by permit processing or inspection failures. These delays can lead to extended project timelines and increased labor costs.
Permitting Costs, New asphalt roof cost
Permitting costs typically include application fees, plan review fees, and any additional fees associated with specific requirements. Application fees are often a flat rate set by the municipality, while plan review fees can vary based on the complexity of the project. For example, a simple asphalt shingle roof replacement might have a lower plan review fee than a complex project involving significant structural modifications. Some municipalities also charge additional fees for expedited review if the homeowner needs the permit processed quickly. In some cases, an engineer may be required to review and stamp the plans, adding to the overall cost. For instance, in a city like Austin, Texas, permit application fees for a roofing project might range from $100 to $500, while plan review fees could add another $200 to $500 depending on the project scope. These costs are usually paid upfront before work can begin.
Inspection Costs
Inspection costs are typically included in the overall permit fee, but additional inspections may be required depending on the project’s progress. These inspections ensure compliance with building codes at various stages of construction. For example, an initial inspection might be required before any work begins, a mid-project inspection to verify proper installation techniques, and a final inspection once the project is complete. Failure to pass an inspection may result in the need for corrective work and additional inspection fees. These fees, while often smaller than permit application fees, can add up, especially if multiple inspections are required due to minor issues. Imagine a scenario where an inspector finds a small discrepancy in the underlayment installation. This could require a costly correction and a follow-up inspection, adding both time and money to the overall project.
Permit Requirements and Inspection Processes
Permit requirements and inspection processes vary widely across different municipalities. Some cities may have stricter requirements than others, leading to higher costs and more stringent inspections. For example, a coastal city might have stricter requirements for wind resistance, leading to a more detailed permit application and more frequent inspections. Conversely, a rural area might have simpler requirements, resulting in lower costs and fewer inspections. Furthermore, some municipalities utilize online permit applications and scheduling systems, while others rely on in-person submissions and appointments. The efficiency of the permitting and inspection processes can significantly impact the overall project timeline and cost. For example, a city with a streamlined online system might have a faster turnaround time for permit approvals, minimizing project delays, while a city with a slower, less efficient system could lead to significant delays and additional expenses.
Roof Size and Complexity
The overall cost of a new asphalt roof is significantly influenced by its size and complexity. Larger roofs naturally require more materials and labor, leading to higher expenses. Similarly, complex roof designs with multiple levels, dormers, valleys, and unusual angles increase both the time and skill required for installation, further impacting the final cost. Understanding these factors is crucial for accurate budgeting.
The cost of an asphalt roof isn’t simply a matter of square footage. While square footage forms the base of the calculation, various complexity factors must be considered to arrive at a realistic estimate. These factors add to the labor costs, potentially increasing the overall expense substantially.
Estimating Costs Based on Roof Size and Complexity
A simplified approach to estimating asphalt roof costs incorporates a base cost per square foot, adjusted for complexity. This base cost can be obtained from local contractors or online resources, and will vary depending on material choices (e.g., 3-tab vs. architectural shingles). Complexity is then factored in as a percentage increase to the base cost.
A basic formula could be: Total Cost = (Roof Square Footage * Base Cost per Square Foot) * (1 + Complexity Factor)
For example, if the base cost is $5 per square foot and the roof is 2000 square feet with a complexity factor of 0.25 (25% increase due to multiple valleys and a complex shape), the estimated cost would be: ($5/sq ft * 2000 sq ft) * (1 + 0.25) = $12,500. This is a simplified model; actual costs may vary depending on several other factors.
Factors Influencing Cost Based on Roof Pitch and Shape
The pitch and shape of a roof significantly affect the labor involved in installation. Steeper pitches make working conditions more challenging and potentially slower, while unusual shapes require more precise cuts and potentially specialized techniques.
Roof Feature | Impact on Cost | Example |
---|---|---|
Roof Pitch | Steeper pitches increase labor costs due to safety measures and slower installation. | A roof with a 12/12 pitch will likely cost more than a 4/12 pitch roof of the same size. |
Number of Levels | Multiple levels necessitate more complex scaffolding and increased labor time. | A two-story house with a complex roofline will generally be more expensive than a single-story home. |
Dormers | Dormers add extra complexity to the roofline, requiring precise measurements and cuts. | Each dormer adds to the overall material and labor costs. |
Valleys | Valleys require careful flashing installation to prevent leaks, adding to both material and labor costs. | Multiple valleys, especially those with sharp angles, increase cost significantly. |
Hips and Ridges | Complex hip and ridge lines increase the time required for installation. | A roof with many intersecting planes will cost more than a simple gable roof. |
Additional Costs
Beyond the base cost of materials and labor for your new asphalt shingle roof, several additional expenses can significantly impact your overall budget. Careful consideration of these potential costs is crucial for accurate financial planning and avoiding unexpected surprises during the project. Understanding these factors allows for more effective budgeting and a smoother roofing installation process.
Tear-Off of Old Roofing
Removing your existing roof is often a necessary first step. The cost of tear-off depends on several factors, including the size and complexity of the roof, the number of layers of existing shingles, and the accessibility of the work area. A steep or complex roof will naturally increase labor costs. Disposal fees for the old roofing materials are also factored into the tear-off cost. For example, a tear-off on a standard-sized, single-story home might cost between $1,000 and $3,000, but this can increase substantially for larger or more complex projects, or if hazardous materials like asbestos are discovered.
Underlayment Costs
Underlayment is a crucial waterproofing layer installed beneath the shingles. While often included in initial quotes, it’s important to clarify the type and quality of underlayment being used. Synthetic underlayments, offering superior protection against moisture, are generally more expensive than traditional felt. The area of the roof significantly influences the underlayment cost. A larger roof will naturally require more material, increasing the overall expense. For instance, a high-quality synthetic underlayment might add $500-$1500 to the project, depending on roof size.
Roof Ventilation
Adequate ventilation is essential for a long-lasting roof. Poor ventilation can lead to moisture buildup, causing premature shingle degradation and structural damage. Costs associated with ventilation improvements may include installing ridge vents, soffit vents, or other ventilation components. The complexity of the ventilation system and the existing roof structure can significantly impact the cost. For a typical home, adding or improving ventilation might range from $300 to $1,000, depending on the necessary upgrades.
Unexpected Issues and Budgeting for Contingencies
Unforeseen problems during a roofing project are not uncommon. Discovering rotted decking, damaged sheathing, or unexpected structural issues requires additional repairs and increases the overall cost. For example, replacing a section of severely rotted decking could easily add several hundred dollars to the project. To mitigate the financial impact of such surprises, it is wise to include a contingency budget of 10-20% of the estimated total cost. This buffer allows for unexpected repairs without derailing the entire project. For a $10,000 roofing project, a 15% contingency would be $1,500, providing a safety net for unforeseen circumstances.
Contractor Selection: New Asphalt Roof Cost
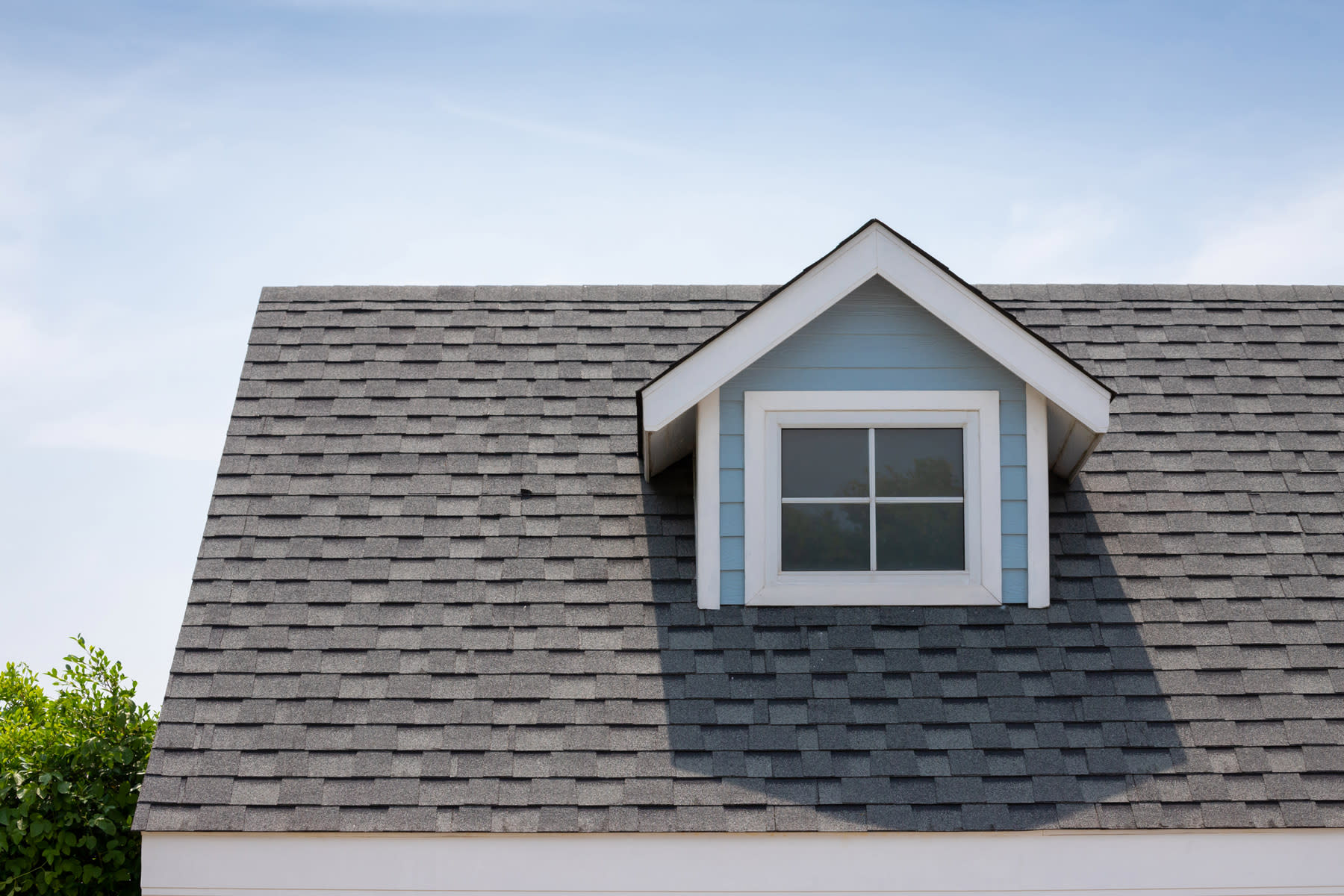
Choosing the right roofing contractor is crucial for a successful and long-lasting asphalt roof installation. The selection process should be thorough and involve careful consideration of several factors, ultimately leading to a confident decision. This section will guide you through the process of selecting a contractor who meets your needs and budget.
Choosing between a large, established roofing company and a smaller, local contractor involves weighing several benefits. Each type of business offers distinct advantages and disadvantages.
Large Roofing Companies versus Smaller, Local Contractors
Large roofing companies often boast extensive experience, a large workforce, and established processes. This can translate to faster project completion times and access to a wider range of materials. However, they may be less personally invested in your project and might charge higher prices due to overhead costs. Smaller, local contractors, on the other hand, often provide more personalized service and may offer more competitive pricing. They might have a deeper understanding of local building codes and weather conditions. However, they may have limited resources and a smaller workforce, potentially resulting in longer project timelines. The best choice depends on your individual priorities and project requirements. Consider factors such as the size and complexity of your roof, your budget, and your preferred level of personal interaction with the contractor.
The Importance of Obtaining Multiple Bids and Comparing Proposals
Obtaining at least three bids from different contractors is a critical step in the roof replacement process. This allows for a comprehensive comparison of pricing, materials, and services offered. Each bid should detail the scope of work, materials to be used, payment schedule, warranty information, and the contractor’s experience and qualifications. Simply focusing on the lowest price can be a mistake; a detailed comparison of all aspects of the proposals is essential to ensure you are making an informed decision. For example, one contractor might offer a lower price but use inferior materials, ultimately leading to higher costs in the long run. Comparing bids helps identify inconsistencies and ensures you are receiving fair value for your investment.
Contractor Evaluation Checklist
Before making a final decision, thoroughly evaluate each contractor using the following checklist:
- Licensing and Insurance: Verify that the contractor holds the necessary licenses and insurance (general liability and workers’ compensation) to operate legally and protect you from potential liabilities.
- Experience and References: Check their years of experience in asphalt roofing and request references from previous clients to assess their work quality and customer service.
- Detailed Proposal: Ensure the proposal clearly Artikels the scope of work, materials to be used (including brand and specifications), payment schedule, warranty information, and project timeline.
- Written Contract: A comprehensive written contract should be signed before work begins. This contract should include all the details discussed in the proposal, as well as dispute resolution procedures.
- Communication and Responsiveness: Assess the contractor’s responsiveness to your inquiries and their overall communication style. Clear and consistent communication throughout the project is essential.
- Permitting and Inspections: Confirm that the contractor will handle all necessary permits and inspections required by local authorities.
- Cleanliness and Safety: Inquire about their cleanup procedures and safety protocols to ensure a safe and tidy work environment.
- Warranty: Carefully review the warranty offered on both materials and workmanship. Understand the terms and conditions of the warranty to ensure you are protected in case of defects.
Financing Options
Securing funding for a new asphalt roof can significantly impact your overall project budget and timeline. Several financing options exist, each with its own advantages and disadvantages. Understanding these options will allow you to make an informed decision that best suits your financial situation.
Financing your roof replacement often involves exploring loans and payment plans offered by various financial institutions or directly through roofing contractors. These options can make a large upfront expense more manageable, but it’s crucial to carefully compare interest rates, repayment terms, and any associated fees to avoid unexpected costs down the line. The total cost of your project, including interest and fees, could increase depending on the chosen financing method.
Loan Options
Several loan types can finance a new asphalt roof. These include home equity loans, which utilize the equity in your home as collateral, and personal loans, which are unsecured and based on your creditworthiness. Home improvement loans specifically designed for renovations, including roofing projects, are also available from banks and credit unions. The interest rates and repayment terms vary significantly across these options, and careful comparison shopping is recommended. For example, a home equity loan might offer a lower interest rate but requires you to have substantial equity in your home. Conversely, a personal loan might be easier to obtain but may carry a higher interest rate.
Payment Plans
Many roofing contractors offer in-house financing options or payment plans. These plans often involve spreading the cost of the project over several months or years, usually with fixed monthly payments. While this can make the project more affordable in the short term, it’s vital to review the terms carefully, including any interest charges or penalties for late payments. For instance, a contractor might offer a 12-month payment plan with 0% interest, but this may be contingent upon good credit. Other plans might involve a higher interest rate than traditional loans.
Comparison of Financing Methods
The table below compares the pros and cons of different financing methods for a new asphalt roof. It is important to remember that these are general comparisons and specific terms will vary based on your creditworthiness, the lender, and the contractor.
Financing Method | Pros | Cons |
---|---|---|
Home Equity Loan | Potentially lower interest rates, tax-deductible interest (in some cases) | Requires home equity, risk of foreclosure if payments are missed |
Personal Loan | Easier to qualify for than a home equity loan, no risk to your home | Typically higher interest rates than home equity loans |
Contractor Payment Plan | Convenience, potentially simpler application process | May have higher interest rates or fees compared to traditional loans, potential for penalties for late payments |
Credit Card | Immediate access to funds | Very high interest rates, potential for debt accumulation |
Impact of Financing on Total Project Cost
The chosen financing method can significantly affect the total cost of your new asphalt roof. Interest charges, fees, and potential penalties for late payments can add hundreds or even thousands of dollars to the initial project estimate. For example, a $10,000 roofing project financed over 5 years with a 10% interest rate could result in a total cost exceeding $16,000. Therefore, carefully comparing interest rates, repayment terms, and associated fees from multiple lenders and contractors is essential before making a decision.
Warranty and Maintenance
Investing in a new asphalt roof is a significant financial commitment, and protecting that investment requires understanding the role of warranties and the importance of regular maintenance. A comprehensive warranty provides crucial protection against defects in materials and workmanship, while proactive maintenance significantly extends the lifespan of your roof and minimizes the risk of costly repairs.
A strong warranty offers peace of mind, ensuring that any manufacturing defects or installation errors are addressed by the manufacturer or contractor. This protection is typically divided into two main categories: material warranties and workmanship warranties. Material warranties cover defects in the asphalt shingles themselves, while workmanship warranties cover issues arising from improper installation. Understanding the specific terms and limitations of each is vital.
Warranty Coverage and Limitations
Warranty coverage varies significantly depending on the manufacturer and the specific roofing materials used. Material warranties typically range from 20 to 50 years, often with prorated coverage after a certain number of years. This means that while the manufacturer may cover 100% of the replacement cost for defects within the first few years, the coverage percentage decreases over time. Workmanship warranties, provided by the roofing contractor, are usually shorter, typically ranging from 1 to 10 years, and cover issues like leaks resulting from faulty installation. Limitations often include exclusions for damage caused by events outside the contractor’s control, such as extreme weather events or acts of nature. For example, a warranty might not cover damage from a hurricane, even if the installation was flawless. Carefully review the fine print of your warranty documentation to understand these limitations completely. It’s also advisable to obtain warranties in writing, detailing specific coverage periods and exclusions.
Recommended Maintenance Practices
Regular maintenance is key to extending the life of your asphalt roof. A well-maintained roof will require fewer repairs and will last considerably longer than a neglected one. A simple annual inspection is highly recommended. This inspection should involve checking for missing or damaged shingles, inspecting flashing around chimneys and vents for leaks, and ensuring proper gutter and downspout function to prevent water damage. Removing debris such as leaves, branches, and moss is also crucial, as these can trap moisture and accelerate deterioration. During the inspection, look for signs of wear and tear such as curled or cracked shingles, granules accumulating in gutters, or any signs of water damage on the roof or in the attic. Addressing these issues promptly can prevent minor problems from escalating into major, costly repairs. Consider hiring a professional roofing contractor for an inspection every few years to ensure a thorough assessment and identification of any potential problems. Proactive maintenance is far more cost-effective than emergency repairs.
Commonly Asked Questions
What is the lifespan of an asphalt shingle roof?
The lifespan of an asphalt shingle roof varies depending on the shingle quality, climate, and maintenance, but generally ranges from 15 to 30 years.
Do I need homeowner’s insurance to cover roof replacement?
Most homeowner’s insurance policies cover roof damage due to unforeseen events like storms or hail. However, normal wear and tear is typically not covered.
Can I finance a new roof?
Yes, many financing options are available, including home equity loans, personal loans, and financing plans offered by roofing contractors.
How do I find a reputable roofing contractor?
Check online reviews, request multiple bids, verify licensing and insurance, and ask for references.